Advances in heating and cooling systems
Boilers and chillers have a complementary relationship. While one technology heats things up and the other cools things down, they both are designed to improve building operations cost-effectively.
What’s more, while both types of equipment are hardly new, they are continually being improved to meet efficiency, maintenance and regulatory goals.
Advances in boilers
The latest boilers are designed for thermal efficiency, feature modular designs to save space and emit low emission levels. Many use programmable logic controllers (PLCs) and are connected to building automation systems (BASs). They also are built to meet government regulations.
For example, the CBEX Elite firetube boiler from Cleaver-Brooks, Thomasville, Ga., is designed to lower NOx (nitrogen oxide) emissions and maximize energy-efficiency. At 30 ppm NOx, the boiler can maintain a constant 3 percent O2 over its entire operating range. This means that efficiency stays constant and does not fall off when the boiler operates at low loads.
“In addition, the CBEX Elite achieves 10-to-1 ratio turndown, which means it cycles less and is more efficient than traditional firetube designs,” says Gregg Achtenhagen, P.E., LEED AP BD+C, senior manager for packaged boiler systems.
You may also like |
Using BIM to devise an HVAC plan |
HVAC design requirements for medical spaces |
Richard D. Hermans on the evolution of health care ventilation |
|
Recently, Cleaver-Brooks introduced the C2X-HE condensing economizer for high-pressure steam boilers up to 800 HP. The system reportedly is ideal for hospitals with large domestic water loads or a high percentage of make-up water. In certain applications, it can increase system efficiency up to 94 percent, according to Achtenhagen.
“New legislation requires high-efficiency boilers, 92 percent and higher, to reduce fuel consumption over the life of the boiler,” says Ross McCartney, director of marketing and product management, Patterson-Kelley, East Stroudsburg, Pa.
To meet those requirements, the company has developed a line of Sonic stainless steel condensing boilers that deliver up to 97 percent thermal efficiency and can fit through a standard-size door. “This allows hospitals to upgrade their old low-efficiency boilers without knocking down walls. The Sonic line is available in 650 MBTUs [million BTUs] through 4,000 MBTUs and also in a domestic water version up to 1,000 MBTUs,” McCartney says.
Hurst Boiler & Welding Co. Inc., Coolidge, Ga., offers the StackMaster economizer, which is designed to boost boiler efficiency. In effect, the stack economizer acts as a waste heat-recovery device, ensuring that available heat does not go unused. Instead, heat is recovered to preheat the boiler’s make-up water. “One could think of this as a built-in feedwater heater that ensures that the make-up water used to replenish the boiler is preheated to near boiling temperatures, so that the boiler does not have to expend as much energy heating it to steam,” says Ray Pierce, national sales manager.
Laars Heating Systems Co., Rochester, N.H., offers the MagnaTherm, which is available as a boiler or volume water heater. It is 95 percent thermally efficient, and offers modulating-condensing operation in 1.6-, 2-, 2.5-, 3-, 3.5- and 4-million BTU/hour sizes. “MagnaTherm offers a 5-to-1 ratio turndown, slim vertical design with removable top section, a stainless steel heat exchanger and multiple voltage options to easily match building service,” says Chuck O’Donnell, director of marketing.
The system features a Vari-Prime pump control that seamlessly matches boiler firing rate to pump flow, reducing pumping costs by up to 70 percent. The onboard control balances combustion, air flow and water flow to optimize boiler efficiency, O’Donnell adds.
Hospitals, though, can pose challenges to boiler manufacturers. “One of the biggest issues for boilers in hospitals today is that some personnel don’t know their load, or under what conditions they use the most or least steam,” says Jason L. Bell, PMP, regional manager, Miura America Co. Ltd., Rockmart, Ga. Miura manufactures water meters, gas meters and computer systems that help to tabulate and keep track of boiler usage and efficiency.
“In many cases, the hospital’s boiler system was originally sized for outdated technology,” Bell says. “In fact, 80 percent of our customers are only using 50 percent of their capacity. The real challenge is helping personnel understand that they must invest in a study, or some sort of data gathering, to make sure that we are installing what they need, and not wasting any capital.”
Achtenhagen says more hospitals are using PLCs for both boilers and deaerators. In addition, more health care facilities are measuring oil, gas, feedwater and steam flow at each boiler and deaerator as well as the plant as a whole.
“These meters are connected to a boiler or master panel PLC,” Achtenhagen explains. “When combined with supervisory control and data acquisition or a BAS, they enable operators to better understand overall energy usage. By monitoring trends, operators can see when equipment is not operating as efficiently as possible and take action.”
Looking at future advances for hospital boilers, McCartney says combination units will be a key development. “Hospitals are always looking to reduce operating costs. I believe that smaller footprints and combination equipment (boiler and hot water heater in the same unit) will be a major trend. This will help to reduce the initial capital investment and ongoing maintenance costs. It also will reduce the space required for mechanical rooms,” he notes.
Bell sees a future in which boiler operators and engineers do real-time monitoring and measuring of water use, gas use and efficiency, and use a monitoring system that is interactive enough to recommend changes on how to save money over time. Such a system would predict maintenance issues, and ensure that the correct inventory of spare or consumable parts is available, and automatically order a new part when it needs to be replaced. “We are able to provide these services, as they are readily available, but it’s not being budgeted for by our customers,” he says.
Innovations in chillers
The latest chillers are designed to reduce maintenance requirements, deliver operating efficiency across a wide range and reduce the impact of greenhouse gas emissions via the use of low-pressure refrigerant. Some chillers operate as heat-recovery systems.
Among new systems available to hospitals, the Magnitude series of water-cooled chillers from Daikin Applied, Minneapolis, features magnetic bearings that are oil-free, thus reducing maintenance requirements.
“In large hospital campuses, this is important because the facility is almost always operating at peak performance and it can be difficult to take a chiller offline for maintenance,” says Donald Decker, director of health care national accounts. “Magnitude chillers serve larger facilities with models rated for up to 1,500 tons, a direct response to requirements we’ve seen from the health care field to more efficiently cool larger campuses.
“We’ve recently seen more construction of smaller health care facilities, such as outpatient surgical centers, as alternatives to large hospital campuses,” Decker adds. “That trend is driving demand for air-cooled chillers such as Daikin’s Pathfinder chiller with variable-volume ratio technology. Air-cooled chillers are a viable alternative for hospitals because they help to eliminate concerns related to cooling towers and the maintenance needs of those installations.”
Trane, Davidson, N.C., has expanded its Series S CenTraVac chiller line with the new CVHM model. It provides hospitals with a design that reduces the impact of greenhouse gas emissions through reduced energy consumption and the use of low-pressure, low global-warming potential (GWP) refrigerant, according to Mike Patterson, product manager, centrifugal chillers. The new model operates with R-514A next-generation refrigerant with a GWP of less than 2.
In addition, the Series S CenTraVac features AdaptiSpeed technology, which integrates a specific-speed, direct-drive compressor; a permanent magnet motor; and adaptive frequency drive. “The Series S specific-speed compressor features the industry’s first mixed-flow impeller design. Offering the best attributes of radial and axial designs, the system enables the compressor to deliver better efficiency across a wider operating range,” according to Patterson.
Ralph Breisch, executive vice president of Multistack, Sparta, Wis., sees growing interest in heat-recovery chillers. He says Multistack has pioneered a chiller specifically designed to operate as a heat-recovery system. “The Multistack DHRC [dedicated heat-recovery chiller] system has onboard intelligent controls that are capable of maximizing the amount of simultaneous hot and cold water generation. The DHRC controls the chiller operation in real time, based on both chilled-water and hot-water demand.”
In the area of air-cooled chillers, Multistack’s newest offering is the Model ARA air-cooled chiller with integral full-heat recovery, which delivers hot water temperatures up to 135 F. The system provides real-time control of both chilled- and hot-water supply temperatures. It has three modes of operation: cooling only, heating only, and simultaneous heating and cooling.
Johnson Controls, Milwaukee, offers the YORK YMC² centrifugal chiller, which can operate at a wide range of load and head conditions. The water-cooled, oil-free, magnetic bearing chiller maintains smooth operation at high and low loads, according to Chris Paraskevakos, vice president, global product management, chiller solutions.
“The YORK YMC² can run inverted, which is sometimes called ‘running upside down.’ This means the chiller can operate when ‘entering’ condenser water temperatures are below the ‘leaving’ chilled water temperature,” Paraskevakos says.
“This means the chiller can meet specific requirements in lieu of waterside economizers and achieve high-efficiency values, as low as 0.1 kilowatt/ton at part load. This wide operating range allows the chiller to achieve 80 percent greater efficiency than similar constant-speed chillers at the same off-design conditions,” he adds.
Danfoss Turbocor Compressors, Tallahassee, Fla., offers products ranging from oil-free compressors to balancing valves and variable-frequency drives. The company recently introduced the VTT [variable twin turbo] series of oil-free compressors featuring IntraFlow technology, which provides high full- and part-load efficiency.
“The VTT series enables manufacturers to build high-efficiency chillers up to 4,200 TR [tons of refrigeration] of cooling capacity with high system reliability,” says Jose Alvares, vice president of sales and marketing. “Due to the compressors’ unloading capabilities, the VTT series is ideal for buildings that operate 24/7, such as hospitals.”
Danfoss also has expanded its TG series of oil-free Danfoss Turbocor compressors that utilize ultralow GWP refrigerants and enable chiller manufacturers to build climate friendly and sustainable solutions that support refrigerant regulations — such as those under the EPA’s Significant New Alternatives Policy Program — for reducing direct and indirect CO2 emissions.
With the ongoing phase-out of hydrochlorofluorocarbons (HCFCs), refrigerants are a major issue when it comes to chiller operation. “The right choices for refrigerants today are R134a, R410A and R1233zd. Because of the imminent phase-out date for HCFCs, there is significant business risk in buying an HCFC-dependent chiller today,” Decker says.
HCFCs R134a and R410A can be sold in new chillers until Jan. 1, 2024, in the U.S.; there is currently no time limit on availability of either R134a or R410A for servicing existing equipment, Decker adds. In addition to being readily available and well-vetted, they provide the best value, are safe and efficient, he says.
Regardless of how quickly the industry can shift to low-GWP refrigerants, the available low-GWP options are limited with few-to-no nonflammable options for some commercial applications, according to Paraskevakos.
“This poses a challenge to health care facilities because contractors and owners who are not accustomed to using these types of refrigerants will not anticipate the costs of the added safety considerations, or are limited by building codes prohibiting the use of flammable refrigerants,” he says. “Safety standards such as ASHRAE 15 and its equivalents in other regions are in various stages of revision. We are likely to see special considerations and possible limitations on the use of flammable refrigerants in some application types.”
Preparing for the future
For health facilities professionals preparing to purchase new HVAC equipment, it is well worth researching and investing in boilers and chillers that not only meet today’s needs, but tomorrow’s as well.
Planning for future needs may require more resources but will avoid headaches later.
Neal Lorenzi is a freelance writer based in Mundelein, Ill.
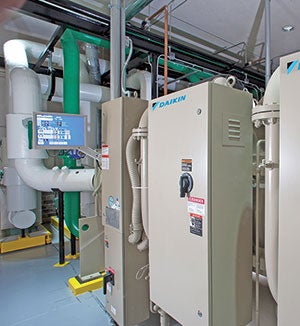
Under Control
The Magnitude chiller’s compressor controls its response in power loss situations to avoid being offline for extended periods of time. Daikin Applied
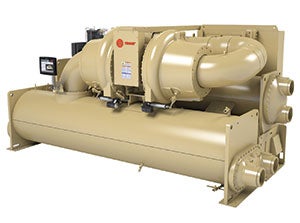
Energy saver
The Series S CenTraVac chiller line reduces the impact of greenhouse gas emissions through reduced energy consumption and the use of low-pressure, low-GWP refrigerant. Trane

Switch hitter
The MagnaTherm, available as a boiler or volume water heater, is 95 percent thermally efficient. Laars Heating Systems
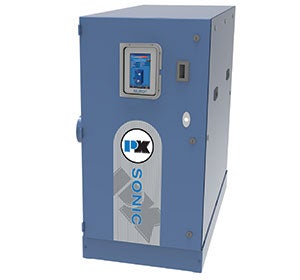
Multipurpose supply
The Mid-Size Sonic stainless steel boiler, ranging from 650 to 1,000 MBTUs, can be used for either comfort heat or hot-water supply. Patterson-Kelley
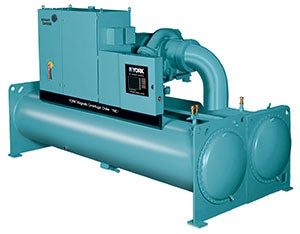
Four-way winner
The YORK YMC² Centrifugal Magnetic Drive Chiller features active magnetic bearing technology to address the most critical concerns of facilities managers: energy, sustainability, sound suppression and uptime. Johnson Controls
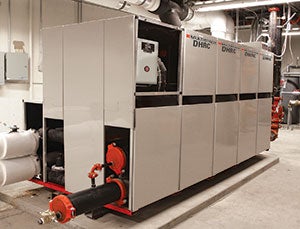
Double duty
Dedicated Heat-Recovery Chillers can produce hot water up to 175 F for heating while simultaneously producing chilled water for cooling. Multistack

Not a trace
New technology in the CBEX Elite firetube boiler enables it to attain near-perfect combustion and the lowest possible NOx emissions. Cleaver-Brooks

Running start
EEX Gas/Oil Series High Pressure Steam Boiler minimizes carryover and produces dry 99-plus percent saturated steam in less than five minutes from a cold start. Miura America Co.
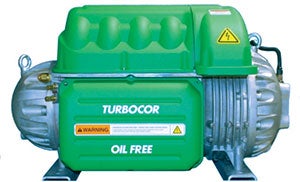
Go green
TG Series Compressors utilize ultralow GWP refrigerants. Danfoss Turbocor Compressors