Unlocking the potential of an existing CMMS
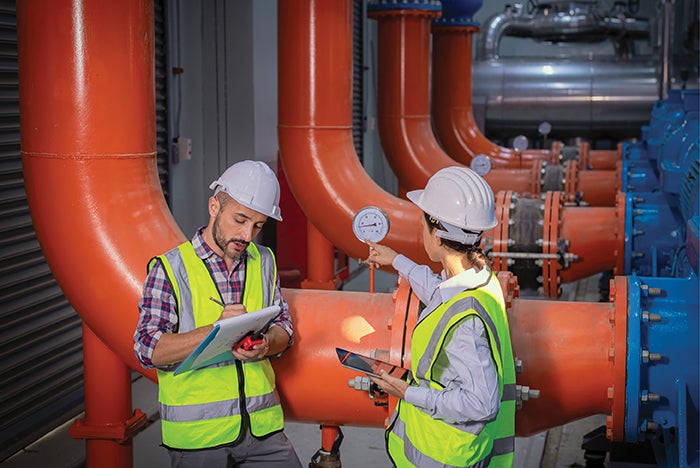
An effective CMMS is a dynamic system that supports day-to-day operations, empowers front-line content experts and equips leaders with the insights to make sound decisions.
Image by Getty Images
Health care facilities teams face more than labor challenges and aging infrastructure. They’re also navigating misaligned processes, outdated maintenance strategies and computerized maintenance management systems (CMMSs) that too often become a burden rather than serving as the organization’s operational backbone.
The goal isn’t just better software; it’s unlocking the full potential of the CMMS already in place.
Critical data often disappears into a digital black hole. Front-line content experts (FCEs) waste valuable time navigating cluttered screens, irrelevant fields and endless clicking.
Despite costly investments in CMMSs, many teams continue to rely on redundant software, rogue spreadsheets and paper logs, undermining the system that was implemented to streamline operations, reduce waste and support informed, data-backed decision-making.
A new approach
CMMSs are frequently misaligned because they are deployed or managed without a full understanding of the hospital’s operational processes and the realities of front-line workflows. Over time, these systems become patched together with extra fields, redundant steps and unnecessary data collection, all in the name of better data. The result? A bloated CMMS that generates more noise than insight. Instead of enabling clear decision-making, it creates confusion, frustrates FCEs and buries leadership under layers of irrelevant data.
This is where many facilities leaders become stuck. There is a common belief that more data equals more insight. However, poor data leads to poor decisions, wasted time and a disengaged front-line workforce. On the other hand, a well-optimized CMMS captures only what is necessary, eliminates waste and transforms operational activities into actionable intelligence. With this mindset, the CMMS can be reimagined not as a burden but as a vital, decision-enabling tool.
When organizations discuss CMMS optimization, what does it truly mean? An optimized CMMS is not simply cleaner but smarter. It aligns with workflows, prioritizes what matters most and removes the noise that impedes performance. It effortlessly and automatically converts raw data into information. It avoids unnecessary fields, simplifies front-line workflows, enhances reporting clarity and rebuilds trust in the system.
The good news? CMMS optimization does not require starting from scratch. Implementing a replacement CMMS should be the absolute last option, not the first. What is needed is a new approach that starts with desired outputs, aligns data structures with priority and supports risk-based decision-making. This roadmap is designed to help facilities leaders, supervisors and FCEs unlock the full potential of their existing CMMSs. The objective is to cut through the clutter, streamline processes and transform a CMMS into a high-value operational tool.
Three pillars of success
An effective CMMS is not just a digital filing cabinet; it is a dynamic system that supports day-to-day operations, empowers FCEs and equips leaders with insights to make sound decisions. To achieve this, every organization must build its system on the following three foundational pillars:
Pillar 1: Workflow-driven design. This ensures that the CMMS reflects how the facilities team functions, not how a software vendor prescribes it. Too often, systems are developed in isolation without consideration for how FCEs interact with them. A successful CMMS begins with a detailed understanding of real-world processes: how service requests are submitted; how inspection, testing and maintenance activities are performed; and what information FCEs require at the point of performance versus what may hinder them.
When the CMMS mirrors workflows, it becomes a natural extension of daily operations rather than a burdensome task. Poorly designed systems force users to go out of their way to enter or retrieve information, resulting in non-value-added work and diminished data quality. Because FCE labor represents the second-highest facilities department expense after utilities, inefficient workflows are not only operationally disruptive but also financially irresponsible. Every minute spent on redundant entries, unclear steps or unnecessary system interactions diverts time away from patient safety, asset preservation and regulatory compliance. Organizations that invest in intuitive workflows improve efficiency, protect capacity and enhance outcomes. When they fix the flow, the data will follow.
Pillar 2: Structured, aligned and standardized data. Even the most well-designed workflows fail when burdened with inconsistent or disorganized data. Without proper structure, a CMMS quickly devolves into a digital junk drawer, overflowing with data yet nearly impossible to query, interpret or trust. Clean, consistent data provides the foundation for accurate reporting, compliance tracking and informed, risk-based decision-making. It enables a shift from reactive firefighting to proactive planning.
This pillar depends on standardized field values, elimination of duplicate or improperly merged entries, limited use of free-text fields and intuitive naming conventions that are easily understood by FCEs and leadership. When data is reliably entered into the correct fields, it becomes actionable, scalable and trustworthy. Organizations also should be cautious about excessive customization. While custom features may seem helpful, they often increase complexity and reduce long-term system manageability. A better approach is to map actual workflows and align them with the out-of-the-box features already available in the CMMS. Every field should serve a clear and necessary function.
Pillar 3: Purposeful reporting and decision support. Data alone is not enough; it must drive timely, informed decisions. The value of a CMMS lies in its ability to provide actionable insights through reporting tools, dashboards and real-time tracking of key performance indicators. These outputs must directly support the organization’s strategic goals, such as compliance readiness, labor utilization, asset life-cycle forecasting and capital planning.
When reporting is designed with intent, it enables confident decision-making and aligns stakeholders with a shared understanding of performance and risk. Data collected without purpose is just noise; data structured to support decisions becomes a powerful organizational asset.
CMMS optimization
When all three pillars are in place, the CMMS evolves from a basic ticketing tool into a strategic operations platform. It accelerates decision-making, enhances patient safety, improves financial stewardship and becomes the operational backbone of the organization.
But turning principles into progress requires more than good intentions. It requires a structured and deliberate approach. The following six steps to CMMS optimization serve as a practical roadmap to begin guiding teams through clear, day-to-day improvements that simplify workflows, improve data quality and elevate decision-making:
Step 1: Structuring permissions for clarity and growth. Optimization involves refining permission structures, so users only see what’s relevant to their roles. Granting every user full access only leads to confusion, misalignment and data inconsistency. A well-structured permissions strategy aligns access with responsibilities by ensuring that new team members are not overwhelmed, seasoned team members are empowered and data entry remains aligned across the system. It’s not about restricting access as a form of control; it’s about enabling clarity and growth. By simplifying the interface for each user type, organizations improve adoption, reduce errors and create natural pathways for professional development as responsibilities evolve.
Step 2: Reverse engineer the system to turn data into decisions. Many CMMS platforms are flooded with data that has no defined purpose. These systems often fail because they start with data collection without identifying the operational questions the data must answer. Optimization instead begins by identifying essential outputs, such as compliance reports, risk assessments, asset life-
cycle forecasts and labor performance metrics. From there, the necessary inputs can be defined and built into the system intentionally.
An optimized CMMS is not merely a data repository. It is a decision-support tool that translates raw data into useful information. For example, a generator run-time log is only raw data until it is paired with maintenance thresholds and becomes part of a service forecast. Every field within the system should have a specific function. Fields that do not contribute to meaningful outputs should be eliminated. When FCEs spend excessive time entering data with no return in value, or when leadership cannot access usable insights, the system is no longer serving its intended purpose. This step ensures the CMMS supports real operational outcomes rather than becoming a source of digital clutter.
Step 3: Apply risk-based asset management. More than 80% of a facility’s total life-cycle costs are directly tied to owning and operating its structure, systems and assets. With this financial impact, asset risk management must be central to CMMS configuration. Rather than stopping at basic asset identifiers like manufacturer, make and model, equipment should be classified based on its function and potential impact on safety, infection control, operations and regulatory compliance. For example, an exhaust fan serving an airborne infection isolation room carries significantly greater risk than one serving a public restroom and should be managed accordingly.
Risk-based scoring facilitates intentional maintenance program planning, informed resource allocation and improved compliance alignment. Most importantly, it ensures that teams focus their time and energy where it matters most.
Step 4: Eliminate CMMS noise with field, form and language standards. Over time, many CMMS platforms accumulate unnecessary fields and inconsistent terminology. While these additions may begin with good intentions, they often result in confusion, slow performance and diminished user trust. Effective optimization requires discipline in the field and form design. Only the data that directly supports workflows, decision-making and compliance should be captured. Anything more introduces unnecessary complexity.
In addition to reducing field count, organizations must focus on clear and consistent language. Vague and outdated or vendor-specific terminology create avoidable errors. For example, labeling an equipment identifier field as “barcode” may be inaccurate if the organization uses QR codes or dot-matrix labels. The more inclusive term “asset ID” avoids confusion and accommodates multiple technologies. Standardizing terminology across the CMMS enables faster data entry, more accurate reporting and a better user experience.
Step 5: Prioritize mobile usability and offline access. FCEs do not live behind a desk; they work on rooftops, in central plants and mechanical rooms, and in dark, remote spaces. If the CMMS can’t function in these environments, it becomes a liability. A mobile-first CMMS must support offline functionality as well as auto-synchronization when Wi-Fi becomes available. The easier it is to complete work in the field, the better the data, the faster the closeout and the sooner data is converted into actionable information.
Step 6: Load equipment during construction and commissioning. Too often, CMMS data entry happens after handover, when critical information is incomplete or missing. Instead, equipment should be loaded during construction and commissioning. This ensures that assets enter the system with accurate metadata from the start — location, maintenance requirements, warranty dates, compliance needs and more. This head-start approach improves accuracy, saves time and builds long-term confidence in the CMMS.
From burden to backbone
In today’s health care environment, where facilities operations directly impact safety, compliance readiness and financial performance, a misaligned CMMS is more than just an inconvenience; it’s a risk.
However, a well-optimized CMMS is not about chasing the newest platform or adding more complexity; it’s about building a system that mirrors real-world workflows, captures only what matters most and turns raw data into actionable insight. By focusing on the three pillars of CMMS success and applying the six steps to CMMS optimization, health care facilities teams can begin moving from firefighting to fire prevention, from reactive to predictive.
It starts with one decision — to stop accepting the CMMS as it is and start shaping it into what it can be. An untrusted CMMS doesn’t need to be replaced so much as it needs to be reimagined. Teams that succeed in 2025 and beyond won’t be those with the most data but those with the right data at the right time driving the right decisions.
Related article // Ensuring a facility’s CMMS is empowering the team
The role of the so-called “firefighter” is often celebrated and even rewarded within health care facilities management. Firefighters are team members who respond at a moment’s notice, improvising and bringing failed equipment back to life, MacGyver-style. While admirable in a crisis, firefighting was never meant to be a long-term or sustainable maintenance strategy. Unfortunately, this outdated mindset often spills over into how organizations manage their computerized maintenance management systems (CMMSs).
A well-optimized CMMS should prevent fires versus acting like a fire alarm to track crisis response. When misunderstood, underutilized or misaligned with workflows, teams become frustrated, data quality declines and reporting becomes unreliable. Over time, the system shifts from a trusted solution to something merely tolerated.
Overcoming these challenges doesn’t require starting over. While replacing the system may seem tempting, true optimization starts with a mindset shift and a commitment to continuous improvement through small, purposeful adjustments that deliver lasting results. Done right, a CMMS not only streamlines maintenance but also empowers leadership with the actionable data needed for informed, strategic decisions.
Optimization includes innovating and pushing the boundaries of what was previously thought possible. It involves simplifying fields, correcting data inconsistencies and aligning workflows with real-world processes. It also ensures front-line staff are equipped with context instead of just instructions, empowering them to expand their knowledge and deepen their understanding of why the system matters and how every input informs decisions. This fosters a culture of ownership, accountability and continuous improvement among users.
Every journey begins with a single step. Some actions that organizations can take to start transforming their CMMS from a burden into an operational backbone include:
- Facilities leaders should ask themselves, “When was the last time planned maintenance was performed on the CMMS?” If the answer is “never,” it’s time to start.
- Facilities leaders can open a work order to audit data entry fields, then highlight any fields that are never used or don’t contribute to reporting and mark them for removal or revision.
- Facilities teams should identify one report that leadership relies on and work backwards, asking “What data fields feed this report?” Then, they should delete or flag unnecessary fields not tied to decision-making.
- Facilities leaders should schedule a 30-minute CMMS walk-through with a front-line content expert. They should closely watch the process steps required to complete a work order and take note of pinch points and cluttered workflows.
- Facilities teams should create a CMMS cleanup board, which is a living list of obvious problems, bloated dropdowns, duplicate records, irrelevant fields and other issues.
- Facilities teams should test mobile usability by going to remote locations and completing work orders from the field.
- Facilities leaders should pick one asset and assess its risk level, asking, “If this fails, what’s the impact?” They should then use that to start developing a basic risk-based prioritization model.
Small adjustments over time restore trust, reduce friction and empower team members to focus on what matters most — delivering an unparalleled patient care experience at the highest value possible. As stewards of the physical environment, facilities teams must treat the CMMS like any other mission-critical asset. They must maintain the CMMS intentionally, operate it efficiently and align it with the organization’s purpose.
Ryan Schramm, CHFM, CHC, MECH, FASHE, provides consulting services in CMMS optimization, asset risk management and patient-centered maintenance strategies. He also serves as the senior systems manager for facilities operations at Banner Health and as a subject matter expert with Legacy FM, both of which are headquartered in Phoenix. He can be reached at rschramm@legacy-fm.com.