How to think like a compliance surveyor
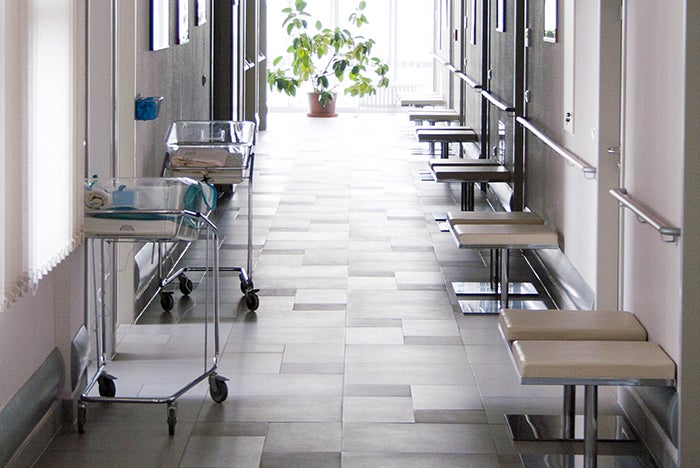
Means of egress during an emergency can be affected adversely by corridor clutter.
What do compliance surveyors see during a building tour? Pretty much everything.
Surveyors who review physical environments are sophisticated in spotting existing problem areas within health care facilities both because they know where to look and because their “fresh eyes” have never seen those areas before.
While many health care facility professionals maintain eagle-eyed surveillance of their physical environment at all times, some other health care facility staff members have reported that they did not see what a surveyor observed until the surveyor brought it to their attention during a building tour.
Commonly cited findings
There are few differences whether the surveyor is performing an accrediting organization’s compliance survey, a state agency is performing a Centers for Medicare & Medicaid Services (CMS) validation survey or its periodic licensing survey, or a local authority having jurisdiction (AHJ) is conducting the survey. The volume of findings may differ based on the number of surveyor-days or on individual surveyor expertise, but many of the types of observations are consistent.
Some of the most commonly cited adverse findings seem to appear in the path of a surveyor’s building tour and can be noted immediately, including National Fire Protection Association’s NFPA 101, Life Safety Code, deficiencies such as blocked fire extinguishers, blocked fire alarm system manual (pull) stations, blocked fire doors or smoke barrier doors, and blocked exit signs.
Further examples are common survey citations such as blocked medical gas (e.g., oxygen) zone valves; daisy-chained or unmounted power strips, which are sometimes called relocatable power taps by many AHJs in deference to the Underwriters Laboratory standard terminology; blocked electrical panelboards; or blocked ventilation system fire dampers or smoke dampers.
And, finally, there may be issues related to hazardous materials and waste risk mitigation such as eyewash stations that are blocked or otherwise unsafe for use, or unlabeled secondary containers containing hazardous materials or hazardous waste.
Means of egress can be affected adversely by corridor clutter, locked doors that are noncompliant with Life Safety Code restrictions, combustibles or other items that can cause safety violations. As an example, the basis for most corridor clutter-related findings is the Life Safety Code, as succinctly stated in CMS K-Tag K211 (“Aisles, passageways, corridors, exit discharges, exit locations, and accesses are in accordance with Chapter 7, and the means of egress is continuously maintained free of all obstructions to full use in case of emergency, unless modified by 18/19.2.2 through 18/19.2.11.”)
Adverse findings in almost any finished space also can include the results of both ceiling-level and above-ceiling observations.
Ceiling-level observations often include such items as damaged ceiling tiles, gaps in ceiling tiles that exceed the NFPA limitations, missing or dislodged sprinkler escutcheons, items hanging from sprinkler heads, damaged or dirty sprinkler heads, and water-stain marks indicating the potential for an infection-control problem. There also may be an increased likelihood of follow-up probing related to such ceiling-tile water stains due to their potential infection-control impact on patient care. Another common citation is caused by stored material observed within the 18-inch clear area beneath the bottoms of the sprinkler heads.
Common above-ceiling observations include inadequately sealed penetrations of smoke barriers and fire-rated barriers, and a sprinkler pipe that supports anything else. AHJs have been citing anything supported by sprinkler piping (even as small as one wire) for several years, and subject matter experts do not expect changes in this situation.
Specialty areas like mechanical or electrical rooms have their own typical findings. Among the common findings in mechanical and electrical spaces are improper sealing of rated barrier penetrations. Leaks under or near equipment could result in follow-up questions pertaining to inspection, testing and maintenance (ITM) processes.
Those follow-up surveyor questions also can result in additional adverse findings. Such areas often have rated barriers surrounding them, triggering a surveyor’s interest in penetrations and penetration sealing systems. Open junction boxes or other uncovered electrical boxes with electrical wiring are often cited as fire risks. Open junction boxes or uncovered electrical boxes without wiring in them are often cited as smoke propagation risks.
Mechanical or electrical equipment that appears to the surveyor to be in an unmaintained condition also can result in follow-up questions about the ITM processes and whether the manufacturer’s ITM recommendations are being followed. This area of questioning then can expand into related questioning that includes the utility equipment inventory, the existence of a CMS-compliant, risk-based alternate equipment maintenance (AEM) program and so on. High-impact patient care equipment (such as emergency generators, automatic transfer switches, fire pumps and other life safety equipment, critical care area HVAC equipment or electrical equipment, etc.) also may trigger increased surveyor scrutiny.
Unlabeled utility system switching equipment, whether it consists of electrical circuit breakers, mechanical valving, medical gas/air/vacuum source valves or other switching equipment, can raise questions about utility system-failure risk mitigation. The CMS Emergency Preparedness Final Rule invokes the requirement for all-hazards preparedness. It is clear from the CMS Survey and Certification Letter 17-29 Emergency Preparedness Interpretive Guidelines and related CMS web instruction that all-hazards preparedness does include preparedness for both internal and external utility system or equipment failures. With that new factor, it is possible that improper or missing utility control-device labeling could become an even more pervasive and impactful finding than previously experienced.
Both CMS surveyors and other AHJ surveyors have been assessing compliance with the NFPA 99, Health Care Facilities Code’s Essential Electrical System branch separation requirements. It has been somewhat common for surveyors to investigate selected life-safety panels, critical branch panels, and the equipment branch to determine whether those equipment directories indicate compliance with the branch separation requirements. Discrepancies with these requirements sometimes result in surprises, including the need for expensive corrective action.
Doors that are meant to be closed or able to be closed but are found blocked open during the survey can result in adverse findings. Examples are fire-resistive, rated door assemblies or smoke-barrier doors that have impediments within their paths. Other fire-resistive, rated opening protectives, such as trash chute discharge doors or linen chute discharge doors, pose fire and/or smoke propagation risks, particularly during periods of heavy chute usage.
Improper pressure relationships can result in high-impact adverse findings, and surveyors have been assessing all such requirements during surveys. Sometimes pressure relationships have been determined to be deficient because of an open door somewhere else in the space when the surveyor was assessing the pressure relationship at a different door.
It is also important to pay close attention to the detailed requirements within NFPA 99-2012. Although some surveyors had addressed selected NFPA 99 requirements (based on previous 2000 Life Safety Code references to NFPA 99-1999) prior to the adoption of the 2012 codes, there is now a much more critical review relative to the detailed NFPA 99-2012 requirements.
Now that CMS has published 33 separate K-Tags related specifically to the adoption of NFPA 99-2012, the detailed requirements, NFPA references and expectations of those K-Tags should be included in all compliance activities. Some of the building tour observations are related to the NFPA 99-related K-Tags.
An example of a detailed NFPA 99 requirement that may have escaped earlier attention includes the NFPA 99 requirement that stipulates the required wording of a sign at the bulk oxygen storage facility as “OXYGEN – NO SMOKING – NO OPEN FLAMES.”
AHJs have been giving adverse findings if the sign does not match that language verbatim because NFPA 99 requires it. Another example of detailed signage requirements is found within the K-Tag K905, Gas and Vacuum Piped Systems — Central Supply System Identification and Labeling details based on the listed NFPA 99 Chapter 5 paragraphs.
There are many opportunities for observation when surveyors see empty or unused patient rooms. Among these opportunities are the potential infection-control issues related to damage to materials, furniture, outlets, walls or ceilings. Patient rooms currently being used for storage historically have had a heavy level of surveyor interest because of the degree of combustible storage within such areas.
Kitchens have their own unique requirements from several NFPA codes and standards. Remember that the 2012 NFPA 101 and the 2012 NFPA 99 both reference many other NFPA codes and standards that are anywhere from 10 to 15 years newer than the editions referenced by the 2000 Life Safety Code.
As with all physical-environment compliance, the detailed requirements are where organizations often find difficulties. From the sprinkler heads in large walk-in freezers and refrigerators, to the Class K fire extinguisher and its new signage within 30 feet walking distance of the hazard, to the hood extinguishing systems, the details are all survey subjects.
Construction, renovation and demolition areas are also important fodder for surveyors. Surveyors likely will be assessing full compliance with the construction risk assessments, infection-control risk assessments and the life-safety risk mitigation processes.
Whether the life-safety risk-mitigation activities are driven by the Joint Commission’s Interim Life Safety Measures or by the NFPA 101 Alternative Life Safety Measures invoked by the other accrediting organizations, surveyors will be looking for life-safety risk mitigation.
The American Society for Healthcare Engineering’s Healthcare Construction Certificate workshop includes an excellent foundation of these requirements for construction and other personnel.
Regular assessments
Because compliance surveyors already know where most health care organizations have challenges with compliance before arriving on-site and they usually have substantial experience in observing challenging situations, health care organizations should proactively and aggressively assess their own facilities on a regular basis.
While many of the observed survey challenges are related to operational processes or human behavior rather than installed infrastructure, the observed infrastructure deficiencies are also rising in volume due in part to the impact of the changes in codes and standards as well as tightened CMS requirements.
With this increased attention, health care facility professionals cannot afford to let their guards down.
David L. Stymiest, PE, CHFM, CHSP, FASHE, is a senior consultant at Smith Seckman Reid, Nashville, Tenn., specializing in facilities engineering and regulatory compliance. He can be reached at DStymiest@SSR-inc.com.