EVS professionals and hospital design
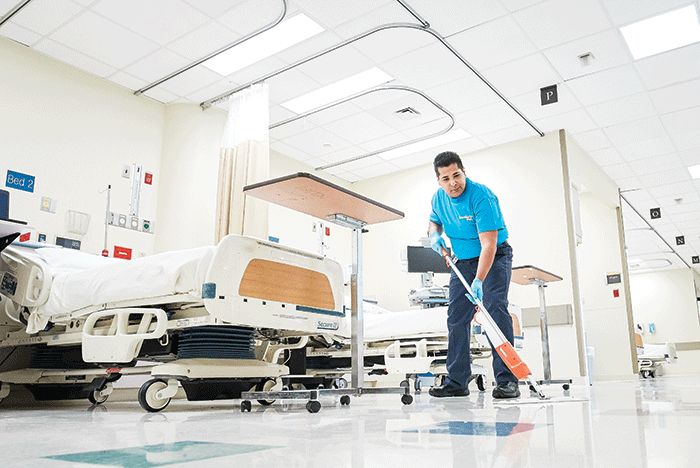
Flooring may be the first surface that environmental services professionals consider when making design recommendations because it is the most visible and most used surface in a hospital.
Image courtesy of Servicemaster clean
Construction and remodeling are almost constant in the health care field. That’s good, because new, modern facilities benefit patients in a variety of ways.
In addition to aesthetics, new construction can promote better outcomes for patients and enhanced efficiencies for staff. Modern medical equipment and technologies can be incorporated into the design, along with attractive and functional new furnishings. Likewise, the newest finishes and surfaces can create an environment that is more durable, easier to disinfect and, therefore, less likely to harbor infectious microorganisms.
When considering new hospital construction, the planning group usually includes administrators, doctors and representatives of the clinical team, along with architects, construction professionals and engineers. Each group brings an important perspective to the design process.
One group that sometimes is omitted is the environmental services (EVS) department. This is a mistake because EVS has a specific interest in the priorities of almost every group, including patients.
Primary objective
Each stakeholder in the health care construction project team brings to the table a different perspective regarding the list of subordinate priorities. Ask a patient or hospital visitor what is important in a new facility and they will likely mention aesthetics and comfort. Doctors and clinical staff will undoubtedly prioritize medical efficiency and infection prevention. Administrators usually put a priority on cost control, both in the construction phase and for long-term maintenance. For engineers and architects, construction budgets must align with expectations and construction realities.
Once the new facility is built, EVS interacts with all groups on a daily basis. EVS directly affects infection control, patient care, clinical efficiency and cost control, so the EVS perspective aligns well with the priorities of the clinical team and administration. EVS also will touch virtually every surface in the facility every day, sometimes many times a day. By extension, EVS touches every patient every day.
“It’s imperative that environmental services is involved in the design process and selection of surface materials because our department sees the whole picture. We are always working to improve EVS efficiencies and prevent infection; those are daily objectives,” explains Tom Mattice, environmental services director for Montefiore Nyack Hospital, a 375-bed facility in Nyack, N.Y. His hospital recently completed two construction projects and is in the midst of a third.
Mattice notes that his team was involved throughout the design phase in all recent projects. “We are fortunate that our hospital has allowed us input into the selection process of many of the surface materials. There are long-term benefits by having environmental services involved in the planning process.”
Infection prevention is a critical part of daily hospital routine, and disinfecting the facility impacts many aspects of health care outcomes. As a practical matter, it makes sense to build a facility with surfaces that can be disinfected easily, hold up under daily wear and cleaning, and be functional and attractive. In doing so, patient safety from infection is enhanced, manpower costs for cleaning and maintenance are reduced, the lifespan of the surfaces is increased, and a comfortable, convenient and safe setting for patients and staff is created.
At the outset of the design phase, EVS directors should make the case to hospital administrators, clinical staff and architects that their input will have a practical impact on both health care and facility care for years to come. Some of the surfaces in any new facility that must be cleaned daily or regularly include floors, countertops and desktops, bathroom fixtures, privacy curtains, beds and furnishings, walls and doors, air vents, lighting fixtures, windows and window coverings, and medical equipment.
Cleaning and disinfecting these surfaces is essential for infection prevention, but there are other factors to consider, such as recurring labor costs, the selection of approved cleaning products, and the tools and machines necessary for daily cleaning. The EVS director is the expert on these matters.
One may think about the cost and efficiency impact on an EVS staff if they spend just 5 percent more time each day cleaning surfaces that harbor pathogens. That’s 24 minutes per EVS staffer per day, based on an eight-hour work day.
If a hospital has 20 EVS staffers working daily eight-hour shifts, that equates to eight hours per day of inefficient time, which means less work gets done or the work is rushed. That results in less time for discharge and terminal cleanings and perhaps longer waits for clean exam rooms. That, in turn, means more wait time for patients and increased frustration, not to mention discomfort and perhaps greater health risks.
Inefficiencies can have a significant impact on infection prevention. Less time for the cleaning of waiting rooms, restrooms and common areas may expose more patients, visitors and staff to pathogens. This is contrary to the highest priority: health and healing.
Building a new facility is an excellent opportunity to choose materials that are easy to clean and disinfect, functional, durable, attractive and serve patient needs best. Having EVS input on the front end helps ensure that cleaning efficiency and infection control are integrated into the hospital’s operating philosophy.
The EVS challenge
Choosing surfaces for a health care facility is a balancing act. Patient care and infection prevention are priorities, but the fixtures and surfaces should be attractive, easy to maintain and durable. Designers also should seek consistency — use the same materials throughout the new facility to enhance cleaning efficiencies. EVS directors must be prepared to make informed recommendations when they are asked for input.
“You will be in discussions with administrators, architects, engineers and medical professionals,” says Scott Thornton, director of operations for PCSI in Austin, Texas, which provides EVS for several hospitals on military bases. “They rely on data to make decisions, so EVS directors must be prepared with data to support their recommendations.”
EVS directors should be familiar with federal, state and local regulations when considering surfaces for health care facilities. It’s also helpful to have a checklist to go by. A good place to find such a checklist is the Guidelines for Design for Construction of Hospitals published by the Facility Guidelines Institute (FGI).
In the 2018 Guidelines, it states, “Surfaces and finishes selected should have clear, written manufacturer-provided cleaning protocols that will ensure the product remains durable and can meet [Centers for Disease Control and Prevention] cleaning standards for health care facilities.”
The Guidelines notes that surfaces should be easy to clean with no surface crevices, rough textures, joints or seams; be non-absorptive, nonporous and smooth; and that manufacturer-recommended cleaning and disinfection methodologies be easy to use and effective for meeting Centers for Disease Control and Prevention and other clinical bacterial elimination requirements.
Other considerations should include slip-resistant floors, acoustic characteristics and non-flammability.
Becoming familiar with manufacturer specs and cleaning protocols will help the EVS director create a list of preferred surfaces for various applications in the hospital. When it is time to present recommendations, the EVS director will be equipped with the information to support the recommendation and factors such as resistance to pathogens, durability, recommended cleaning processes and products, projected lifespan, lifespan maintenance costs, and available colors and textures. EVS directors should have this information for every surface recommended for the new facility.
Three key areas
There are three key areas where EVS has the expertise to make a long-term impact on functional hospital design:
Flooring. Floors may be the first surface EVS considers because they are the most visible and most used surface in every hospital. “There’s a great deal of awareness paid to floors,” Mattice says. “They are the first impression when you enter the facility. It’s important to select a surface that is less labor-intensive and provides the best infection control.”
Polyvinyl chloride (PVC) is a type of vinyl surface that is often used in hospitals, clinics and nursing homes. It’s popular because it can be installed in large sheets with few seams and because it has a low cost. On the downside, it requires lots of regular maintenance that is time-consuming, and PVC surfaces typically wear out faster than others, such as ceramic tile.
Many health care facilities now use luxury vinyl tile. Although more expensive initially, these surfaces don’t require waxing or finishing, are durable over time and can be coated to resist chemical stains and body fluids.
Horizontal surfaces. A large hospital can have thousands of square feet of countertops and horizontal surfaces, most of which will be high-touch areas.
Laminates and solid-surface materials are popular because they are inexpensive and come in many colors and patterns. However, laminates are not as durable as metal or solid-surface acrylic surfaces. Acrylic surfaces are seamless, nonporous and very durable, but more expensive initially than laminate surfaces. Engineered stone (usually a combination of marble or quartz and polymer resin) is another expensive alternative. It’s beautiful but perhaps not practical from a budgetary standpoint.
Stainless steel is a good choice for infection control because it is durable, nonporous and relatively affordable, but it is difficult to maintain as a presented “clean” surface. There also are enhanced metal surfaces that actively kill bacteria.
Vertical surfaces. The selection of materials for vertical surfaces, such as walls and partitions, presents two conflicting challenges: infection prevention and acoustics.
Textured surfaces often help with sound dampening, and they are often more aesthetically pleasing, but they are harder to clean and can harbor pathogens. Infection control is always the top priority, so smooth, durable, nonporous, seamless walls are preferred as it is very difficult to disinfect porous finishes.
The selection of wall surfaces is especially important for surgery suites, intensive care and emergency units, and exam rooms.
Informed and prepared
If a hospital is not currently involved in a renovation or building project, chances are it will be soon. It is practical for EVS be part of the planning and design process and imperative that the EVS professional be well prepared for the discussion.
EVS directors should conduct thorough research before recommending any surface material for a hospital or clinic. They should get technical data and clinical trial information. Talk to manufacturers and facilities that already use the material.
The information EVS directors provide will impact patient care and costs for years to come.
Steve Zimmerman, CHESP, T-CSCT, is director of health care services for ServiceMaster Clean, Memphis, Tenn. He is co-chair of the Association for the Health Care Environment’s advisory council and a member of the planning and industry liaison committee. He can be reached at szimmerman@smclean.com.