Maintaining hospital floor surfaces
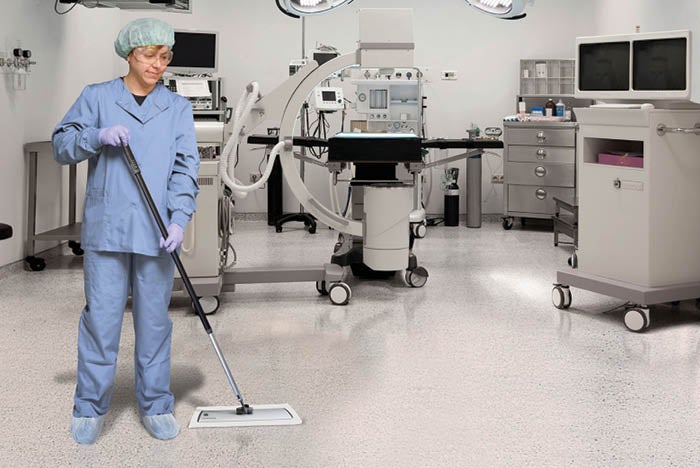
An integrated floor program with the right products, procedures and tools helps create a safer and more satisfying environment of care.
Image courtesy of Diversey NA
From the moment a patient or visitor walks into a health care facility, their first impression of cleanliness often is how the floors appear. However, building a floor care program to give patients and visitors the right impression can present unique challenges.
An integrated program with the right products, procedures, tools, training and measurement processes is key. When the right components are all in place, these solutions will drive improved results and satisfaction, enhancing the image of the facility with patients, staff and visitors.
Factors to consider
There are a number of factors to consider in building such a program. Floor care in hospitals includes key steps that can help deliver a maintenance process that is efficient, reduces wear and extends the life of the floor. Skipping these steps will incur more long-term labor and expense for the facility. The steps include the following:
Step 1. Assess the needs and objectives of the facility. There are many key stakeholders involved, and they may have different needs. Part of this process is an overview of the facility, condition and assessment of the floors and substrates, current practices, identification of best practices and gaps to improve.
Environmental services (EVS) professionals also should be sure to evaluate workflows and optimal times to address certain areas of the facility. Multiple substrates and traffic patterns can create complex needs for total floor maintenance, and getting an overall view of current practices can help start the process to standardize and optimize with a best-practice approach. This also feeds into the planning cycle of how to replace floors in the future.
During the assessment, it is important to understand what challenges may be faced and address them for corrective protocol implementation.
Challenges may include having enough properly trained staff to get the work done; getting access to the floors in patient care areas to allow for daily maintenance as well as more restorative processes to meet appearance requirements and protect from wear and damage; and creating a streamlined and simple program to address the various flooring substrates and traffic levels found throughout the facility.
Step 2. Select a robust floor maintenance program. A floor maintenance program should include regular, periodic, interim and restorative maintenance. This includes using the right products, procedures and frequencies because the wrong product could void the floor manufacturer’s warranty and mean significant expense to replace any damaged flooring. In addition, deploying industry best practices with a standardized approach that is streamlined can help achieve optimal performance.
Considering the different flooring surfaces throughout a facility, it’s often difficult to know where to begin when developing a maintenance program.
The first step is to refer to the manufacturer’s recommendations. This will not only help ensure the warranty of the floor, but may also save time and money by eliminating unnecessary maintenance.
Consistent cleaning and maintenance regimens are designed to keep floors clean and slip resistant while helping to deliver a consistent appearance. The frequency of these processes may vary based on traffic levels and patterns. Additionally, floor finishes and coatings can help protect the flooring substrate from soil and wear. Determining frequency is a critical step to a better floor care process.
Interim and restorative maintenance procedures, such as scrubbing and recoating or stripping, restore floors to an acceptable level when they no longer appear as desired. If consistent cleaning and maintenance regimens are in place, it reduces the requirement and frequency for these more labor-intensive processes.
Streamlining floor care maintenance through the consolidation of products and adding the right tools and machines can help when trying to do more with less. A chemical and equipment supplier can provide guidance to tailor the best solution.
A closer look at types of maintenance programs includes:
- Regular maintenance. This is a routine process of removing dry soil such as dust and dirt through vacuuming, dust mopping and damp mopping. By following these simple processes frequently, EVS professionals can extend the time between more aggressive and costly processes.
Regular cleaning should be performed more frequently at all entrances and less frequently in lower traffic areas throughout the facility.
All floors should be dust mopped prior to wet mopping or a floor-scrubbing process. This prevents excess dirt from accumulating on the scrubbing pads and equipment, or being sucked into the vacuum motor system or scrubbed into the floor finish.
After placing safety or caution signs in the area, the floor is ready to be cleaned. The floor scrubber uses a process of placing water or cleaner on the floor, scrubbing and then removing the water with a vacuum. This is performed in one continuous process as the machine passes over the floor.
A great option for mopping most hard floors is a neutral floor cleaner. A neutral floor cleaner can also be used in an automatic floor scrubber, which is a great labor-saving device. Often, the scrubber will do a good job of removing soils and pathogens versus just moving them around.
When cleaning the floor, the operator should make overlapping passes with the mop or machine in the center of hallways and corridors where most traffic occurs, and only one pass near the walls where there is less traffic. If this is performed in the evenings, nursing can be consulted to see if patient room doors can be closed to limit disturbances.
If a protocol requires that disinfectants be used on the floor, it is important to follow label instructions for the disinfectant and ensure the process allows EVS professionals to meet required contact times.
Some disinfectants may cause hazing of the floors or build up over time. This often can be addressed with a periodic scrub with a neutral or general-purpose cleaner to help remove the residue.
Finally, entrance matting can help capture dirt, snow and debris at the door. This eliminates much of the grit that can soil, scratch and damage flooring. It is also an important tool to help prevent slips and falls.
- Periodic maintenance. This consists of more aggressive methods, which incorporate scrubbing, buffing and burnishing. Depending on the traffic volume or location of the particular floor, this may be performed more often.
Higher-frequency scrubbing is performed in locations closer to facility entrances and in high-traffic areas versus locations toward the center. When creating floor-cleaning schedules, consider the traffic and workflow to be utilized to ensure that time can be spent where needed.
Both buffing and burnishing are ways of repairing fine scratches in floor finish. Buffing is considered a lower-speed method whereby a traditional “swing” machine is used often with a red pad. It is labor intensive and time consuming as the operator moves the machine from side to side across the floor. Burnishing, on the other hand, is considered a higher-speed method. It is faster and may produce higher gloss levels. Unlike the swing machine, the operator pushes the burnisher similar to a lawn mower.
Some concerns with buffing and burnishing include the level of noise, dust creation and accessibility to the area. If dust is a concern, a better option might be wet burnishing. This combines the best of spray buffing and burnishing for instantaneous and satisfying results. This method refreshes floor appearance with immediate results and minimal impact on air quality.
Other benefits of this method include adding protection to the floor, instead of sanding off the finish, and providing some cleaning capabilities. It will extend the floor care life cycle and save labor by repairing damage and reducing floor stripping frequency.
Diamond pads are used for polished stone floor maintenance and can also be used on floors coated with a floor finish. These pads are a good option because a single pad can be used for both cleaning and burnishing, reducing complexity, labor and training.
When deciding where to use a pad or brush, it is important to understand the smoothness of the surface. Pads should be used on smoother floors, while floors that have texture or grooves may be more easily cleaned with a brush to allow the operator to get into the grooves.
Finally, floors can become sticky or hazy if cleaned with an oversaturated mop, an overly concentrated cleaning chemical, or from the extended use of quat disinfectants, which can leave a residue over time. Another cause is skipping the dry dust step before damp mopping.
If floors are sticky or hazy, an interim scrub is recommended using a general-purpose cleaner to remove the dirt or residue.
- Interim maintenance. The scrub-and-recoat process uses a more aggressive cleaner and pad or brush to soften the finish while applying more friction to the floor to remove soils that may have become embedded in the finish or coating over time. This process requires the operator to scrub the floor, rinse, allow it to dry, and apply a coat or two of finish after the process to replace what was removed from daily traffic and the more intensive scrubbing process.
The scrub-and-recoat process leaves the floor looking fresh and clean. It also reduces the frequency of more labor-intensive processes, such as stripping and reapplying finish to the floor. Reapplication of finish is required when doing a deep scrub. Using the more aggressive pad and cleaner will leave the floors looking very dull and poor.
- Restorative maintenance. Stripping is the most aggressive aspect of floor care and is performed when the finish has become degraded and cannot be maintained with scrubbing and burnishing to provide the desired shine and protection.
The restorative process consists of removing all the remaining old finish from the floor surface and applying new layers of finish.
Applying new floor finish is the most critical aspect of the entire process. EVS professionals can use these questions to help select and ensure they are using the right products:
- What flooring surfaces will the finish be used on? With multiple flooring substrates, it might be possible to reduce complexity by getting the right finish that is versatile enough for all.
- How much labor can the EVS department put into floor maintenance? Select a finish that best matches the department’s maintenance schedule.
- What equipment does the department have available? Make sure the finish matches the speed of the department’s equipment.
- Is accessibility to the floors a major concern? Gaining access to certain areas to complete floor maintenance projects can be a big challenge. EVS professionals should take this into consideration when selecting a finish. For example, under the right conditions, applying a higher solids floor finish may reduce the number of coats needed.
- Is the odor of the floor finish a potential problem? Floor finish odor varies greatly by product, and EVS professionals should understand what is acceptable.
- Is hand sanitizer marking an issue? Floor finishes are available that have been formulated to resist damage from hand sanitizers.
Step 3. Implement a training program and materials. EVS professionals should work with their manufacturers to develop a program and outline the steps with customized tools that help with training and best practice adoption. They should ensure the staff is trained with the products and procedures to do the job well. Some manufacturers have excellent training and application tools available to ensure consistency and thorough practices.
Step 4. Round and inspect. EVS professionals should establish a rounding routine to assess the various areas of the facility for the impressions they make. They should identify areas for intervention and provide both feedback and tools to staff members to help drive continuous improvement.
First impression
A first impression is paramount. A lasting impression can improve satisfaction as well as safety in a health care facility. An integrated floor maintenance program with the right products, procedures and tools is key to creating a safer and more satisfying environment of care.
Van Walter is a floor care expert and director of training and applications for Diversey NA, Fort Mill, S.C. His email is van.walter@diversey.com.