Fostering greater staff engagement
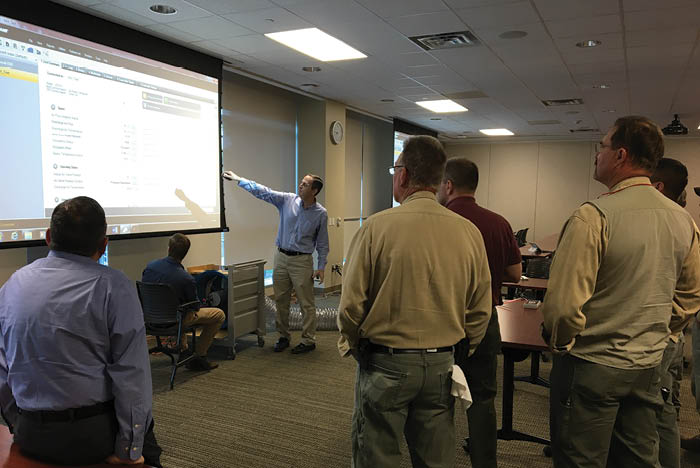
Energy Connect classroom training includes live demos of VAV box and static pressure resets.
Image courtesy of Atrium Health
Keeping patients and staff safe and comfortable is the primary focus of health care facilities staff, but maintaining these conditions can require significant energy. Conditioned air and water transported throughout a campus are the primary drivers for energy consumption in hospitals.
An explosion of new technologies, including sensors and building automation systems (BASs), have been introduced to ensure systems function as efficiently as possible. Retrocommissioning and advanced fault detection software also offer efficiency upgrades, such as optimized sequences of operations and the detection of overrides and malfunctioning resets.
At the end of the day, however, responsibility for safety and comfort rests in the hands of on-site mechanics and technicians. They understand the nuances of their buildings and systems better than anyone and will drive their operation based on what they know will work.
If mechanics are trained on the concepts of energy-efficient operations, as well as the technologies installed to automate optimization, they are able to operate their buildings and resolve issues in the most energy-efficient way.
Atrium’s training program
As Atrium Health, Charlotte, N.C., embarked on its journey to reduce energy consumption, retrocommissioning and advanced fault detection were key elements for reaching the goal. The health care system realized, however, that if the building mechanics were trained to understand the sequences and technologies being put into place, they could leverage their building knowledge to find further savings opportunities and maximize the program’s success. On-the-job training on operating HVAC systems in an energy-efficient manner was needed, but no formal training program or template existed.
Beginning in 2016, Atrium Health partnered with the University of North Carolina at Charlotte (UNCC) to develop an innovative training program for its mechanics. Faculty and researchers from the Energy Production and Infrastructure Center at UNCC worked with Atrium Health to develop a program called Energy Connect focused on teaching mechanics a new concept: energy troubleshooting.
Mechanics are intimately familiar with how to troubleshoot problems in a faulty piece of equipment, typically by following a set of steps to diagnose the root cause of a problem. The team from UNCC decided to adopt this familiar format to teach operators how to spot energy inefficiencies in system operations.
An example of energy troubleshooting is identifying and reducing reheating on a warm day.
Traditionally, air-handling units (AHUs) cool the air to approximately 55 degrees F. If a space needs warmer air to maintain occupant comfort, the variable-air volume (VAV) box for that space will use hot water to reheat the supply air before it enters the room. Even though occupants are comfortable, energy is being wasted. A mechanic doing energy troubleshooting will be on the lookout for reheating and will notice in the BAS that cool air is being reheated in many rooms. This opportunity can lead to significant savings.
Identifying energy experts
The team from UNCC worked closely with staff at Atrium Health to identify a process for teaching mechanics about energy troubleshooting.
To begin, the team provided energy basics training to all mechanics across the enterprise. Next, facility managers and directors identified HVAC mechanics at each acute care hospital who showed an eagerness to learn during energy basics training. These individuals became the site’s “Energy Performance Experts” and were provided more advanced training.
The first step was to ensure the Energy Performance Experts understood the core concepts governing how energy is used for HVAC inside a hospital. The team focused specifically on AHUs, providing training on the concepts needed to understand efficient operation.
The team from UNCC started with a set of classroom-learning experiences and developed a set of materials focused on four key questions:
- Question 1: Are primary sensors or actuators faulty?
- Question 2: Is air being moved efficiently?
- Question 3: Is air being cooled efficiently?
- Question 4: Is outside air being used appropriately?
To help the Energy Performance Experts understand the answers to these questions, the classroom materials elaborated on important physical concepts.
For example, Question 2 requires an understanding of how fans operate inside an air handler to maintain static pressure. If static pressure is set to a value higher than needed, each room receiving air from the AHU will close the damper that admits air into the space. Maintaining such a high static pressure requires greater fan energy. Lowering this value reduces fan energy and allows the dampers to open further. As long as each room receives the necessary airflow, occupants should remain comfortable, but the system will be more energy efficient.
Even though such concepts are familiar to engineers performing retrocommissioning, they are not top of mind for most mechanics. The team from UNCC educated the Energy Performance Experts on these concepts in a practical manner that did not require a detailed understanding of physics.
BAS training
All the Energy Performance Experts participating in Energy Connect have a basic understanding of how to use their BASs. They have all received training on how to navigate the different screens and menus, how to click on different components and how to make certain updates.
Some mechanics only use their BASs to make changes when alarms are triggered or work orders are submitted, but the BAS is one of the most important tools used in energy troubleshooting and management, so the Energy Performance Experts needed to be trained on “what to do” with their BASs.
Building mechanics are adult learners and hands-on by nature, so the team did not want to focus too much on classroom learning. Still, some fundamental principles needed to be taught. To keep the Energy Performance Experts engaged, the team chose to rely heavily on real-world examples to which the experts could relate. The team from UNCC reviewed the BAS at each facility prior to each session and identified several AHUs to examine as case studies during each individual lesson.
A typical lesson would begin with slides teaching key physics concepts, then transition to the Energy Performance Experts applying their new knowledge in a real-world scenario. The instructor and experts would review a chosen unit in the BAS and begin an energy troubleshooting exercise using their new knowledge.
For example, in the lesson focused on efficient cooling, the instructors would choose an air handler in which many of the units were reheating. Such units display the simultaneous heating and cooling effect in which air is actively cooled at the air handler only to be heated again before being delivered into a room. The goal is for the Energy Performance Experts to identify the opportunity to modify supply air temperature. They would begin by looking at the summary page showing the real-time behaviors of all the VAV boxes served by an AHU. The instructor and experts would determine opportunities to adjust supply air temperatures or static-pressure settings.
Applying the knowledge
After the initial classroom training, Atrium Health and UNCC developed a checklist for the Energy Performance Experts. This checklist, called an “AHU performance review,” is designed to emulate the basic form of any preventive maintenance procedure. Each month, the experts use the sheet to examine the performance of a given air handler.
The AHU performance review provides the Energy Performance Experts with a clear process for applying their knowledge. It is designed to walk them through the steps needed to ask the four questions provided during the classroom training. For example, it prompts the experts to evaluate the status of all terminal units served by a given air handler. The experts should review summary pages to identify faulty dampers, stuck valves and opportunities to improve control settings.
During the initial rollout, the instructors from UNCC met with the Energy Performance Experts to help them complete the performance reviews. Initially, the instructors would lead the experts through the process but, eventually, it transitioned to a process driven by the experts. This master-apprentice model allowed the experts to ask questions and better develop their skills. It also allowed them to gain confidence during the early stages.
Anytime opportunities or faults are identified during the performance review, the Energy Performance Experts generate an energy fault work order that is tracked just like any standard work order. During the initial performance review sessions, the instructor from UNCC provided the experts with a template for these work orders, which greatly improved the quality of the information collected.
Bigger opportunities
Given the trend toward advanced fault analytics, it is natural to ask, “Why train operators? Can’t automated software tools detect most of the energy waste that occurs in the field?”
To some extent, Energy Connect has focused on teaching mechanics the same rules that are applied in many software packages so they understand what the tools are doing. For example, many analytics packages provide mechanics with automated work orders generated by a fault that has been detected somewhere in the building.
If a work order is generated from a patient room in which the occupant is comfortable, a mechanic might easily think that the work order was the result of a false positive and fail to complete a thorough review. By providing mechanics with an understanding of why such work orders are generated, there is much greater buy-in and opportunity for success.
The greatest benefit of having informed mechanics is the unique opportunity to leverage their detailed knowledge of building operations. As was previously stated, engineers performing retrocommissioning have generic knowledge about how to adjust controls to maximize energy efficiency, but the mechanics’ site-specific knowledge may improve the performance of these controls even more than initially expected.
In one example, an Energy Performance Expert observed that condensation was developing on supply registers served by a certain air handler. During the performance review, the experts at the facility determined this condensation only formed when the static pressure was lowered to a particular point. Low static pressure, combined with reduced outdoor airflow from retrocommissioning, was causing negative building pressure, allowing infiltration of humid summer air. The experts were able to identify this problem and work with their control vendor to develop a solution.
In this example and numerous others, the Energy Performance Experts combined their specific knowledge of the building and its operations with their newfound knowledge about building science and energy troubleshooting to develop optimizations that would not have otherwise been obvious. The experts often notice that control logic can be improved to yield greater savings when certain rooms are not considered as part of a reset operation or when certain changes are made to economizer operation.
As technologies continue to evolve, artificial intelligence (AI) will likely perform the “what if” analysis needed to determine the optimal sequence of operations in any building. Given the unique nature of each building, however, it will take time for AI to mature. Currently, no existing market technologies can perform such detailed analysis. In the meantime, human intelligence can be leveraged to identify key opportunities and continually optimize operations.
Sustaining the gains
A primary focus of Atrium’s large-scale retrocommissioning effort was to introduce new energy-saving sequences of operations throughout their acute-care facilities. These sequences included features intended to reduce airflows, eliminate simultaneous heating and cooling, and maximize the use of economizing.
Their implementation unlocked significant energy savings potential, but Atrium was aware these savings could easily erode over time if mechanics were not trained and the savings were not monitored. For example, a mechanic not educated on the changes might log in to the BAS in response to a temperature complaint and observe the discharge air temperature leaving the AHU was no longer at 55 degrees. He then might override the new sequence assuming the BAS system was in error and thus accidentally reduce the energy savings.
A new mantra quickly emerged within Atrium Health: “Sustain the Gains.” Teams at both the site and corporate levels engaged in education, such as Energy Connect, and the rollout of fault-detection software to support the goal. Although fault-detection software can find operator changes, it can be counterproductive to use such software in that manner. Energy Connect, on the other hand, has efficiently educated building mechanics on these major changes so they are empowered to make energy-conscious decisions and play a central role in sustaining the gains.
Tremendous potential
Atrium Health has invested heavily in retrocommissioning, analytics and regular performance monitoring. The Energy Performance Experts provide Atrium Health with the opportunity to develop a robust ongoing commissioning program that leverages and enhances its previous investments.
UNCC and Atrium Health are piloting a framework that empowers mechanics to use the tools Atrium has purchased to find ever greater levels of health facility energy savings.
Building support for operator training
Energy Connect has become a key component of the energy-management strategy at Atrium Health. A primary benefit is lower energy expense, but there are several other positive outcomes that help sell the program to upper management:
- Increased employee engagement. In an environment with limited ability to improve employee compensation, the program has allowed Atrium Health, Charlotte, N.C., to find an alternative means of investing in its employees. Since the program started, mechanics have expressed greater engagement and satisfaction. The program has allowed them to feel more confident in their abilities, and many of the top “Energy Performance Experts” now feel empowered to go well beyond the requirements of their monthly air-handling unit performance reviews. The hospitals with the most engaged mechanics have made significant strides in energy performance.
- Greater operational efficiency. At Atrium Health and many other health care providers, it is assumed mechanics are doing what they can to ensure maximal equipment efficiency. Without formal training, however, mechanics may not know the level of efficiency that is possible or how to achieve and maintain it. Energy Connect has introduced a means for mechanics to increase their knowledge, evaluate the efficiency of systems and identify opportunities for savings.
- A low-cost means to save. There is always a desire to find energy savings without investing in capital-intensive projects. As mechanics become Energy Performance Experts through Energy Connect, they begin to find savings during their day-to-day duties. Most opportunities are related to equipment operations and control and can be addressed through low-cost repairs or by simple programming changes during regular control vendor visits.
- Sustaining the gains. Retrocommissioning and other major projects introduce significant energy savings potential to facilities but also change building operations. Energy Connect has educated Atrium’s mechanics on the intent and specifics of these projects so they are informed of the changes and empowered to maximize long-term savings.