How thermal imaging and RCM combine to increase reliability
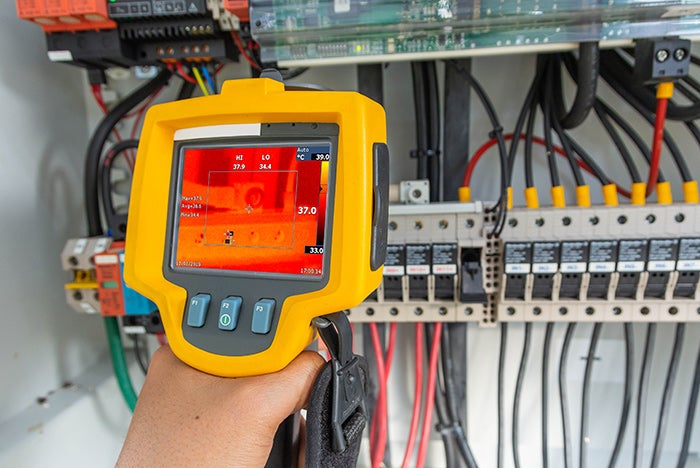
The use of alternate equipment maintenance programs has opened the door for technologies such as infrared scanners to be used more extensively in health care facilities management.
Image from Getty Images
Editor's note: Although the term "reliability-centered maintenance" (RCM) may be unfamiliar to some, chances are that many facilities managers are already using several asset-management tools integral to this concept and well on their way to a complete RCM strategy without yet realizing it. In this monthly three-part series, members of the American Society for Health Care Engineering will explore common tools used in health care facilities today and how they play a role in RCM.
There are competing demands on health care facility maintenance departments. One is a continuous need to do more with less (efficiency), and the other is to do so while maintaining safety and reducing the risk to people, places or things. Facilities managers are constantly trying to work smarter not harder, but still safe or safer. When the regulatory landscape openly endorsed alternative equipment maintenance (AEM) programs, it opened the doors for health facilities departments to look at what they are doing and how they are doing it. This also allows health facilities departments to look at new technologies that can be uses to help ensure safe equipment and environments for patients, visitors and staff.
Any AEM is the result of a comprehensive analysis of specific assets within an organization. Using a reliability-centered maintenance (RCM) method for this analysis will lead one through looking at failure rates, causes and effects, regulatory requirements, manufacturer-specified maintenance activities, environmental variables, age of equipment and many other variables in maintenance. Logically, this analysis may lead to modifying the assets schedule, procedures, repairs or all three.
Let’s use electrical panels as an example asset for this scenario. During an RCM analysis, it has been determined that a common failure are loose or corroded connections. These can cause complete failures (i.e., the circuit is completely interrupted, cutting all power to the downstream connections) or they can degrade the level of electrical energy being passed down the circuit, causing assets connected to it to produce excessive wear due to reduced voltage or amperage.
After identifying a failure, the next step is to define the tasks (or procedures) necessary to prevent or mitigate the failure, or to detect the onset of a failure or a hidden failure. Part of this process is to identify and implement actions, tools and technologies that could ensure the condition is detected early enough to prevent a failure. All this while also balancing the organization’s safety, environmental and economic needs.
Often this process reveals new tools and technologies available for performing those checks and services, and one such technology is infrared scanning.
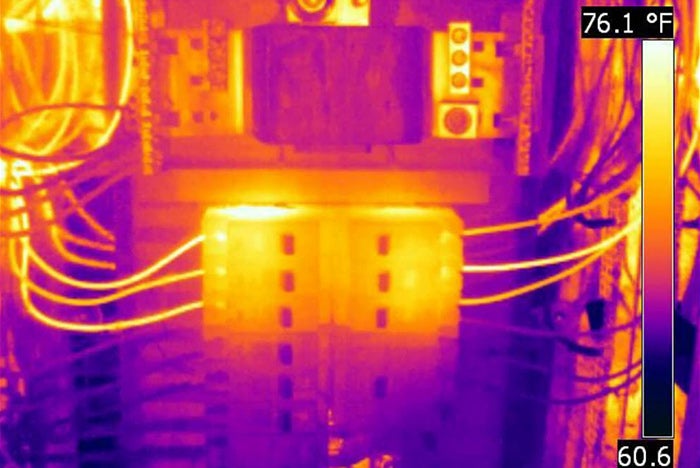
Scanning assets such as breaker panels can reveal hidden issues.
Image by author
There are many assets in health care where infrared scanners can reduce costs and risk by using technology to complete traditionally manual processes. On assets such as breaker panels, sub panels, switchgear, etc., heat usually indicates a problem. An infrared scanner will reduce risk by indicating, via color-coded images, where heat has increased due to loose or corroded connections, and these conditions could pose a threat to the technician or system. Since the scanner replaces the need for the technician to open the panel housing to identify an issue, risks associated with both heat (burns) and shorts (electrocution) are reduced. And if no issues are detected the technician has saved time (and hence, cost) by eliminating the time it takes to follow proper lock-out\tag-out procedures and opening the panel housings.
With tanks, such as fuel, propane, water, etc., potential failures can come from condensation, low volume, blockages and bad seals. Infrared scanners can identify these issues in color-coded scans, where cooler colors (blues) could indicate condensate or emptiness and hotter colors (reds) can indicate evaporation or constrictions.
Scanners can eliminate the risks (and time\cost) of climbing access ladders to open the hatch (or view the site glass) to “see” how full the tank is. And with opening a hatch comes the risk of spillage (although small amounts, it’s still a hazard) and losing objects in the tank (like a flashlight, glasses, etc.). Instead, the technician can remain at ground-level, several feet away from the tank, scan the tank and get a clear indication of the content level and condition of the structure. This ability to walk up to a tank, scan it, read, and record the level and the scan, then move on can reduce the time of these inspection by 50% or more.
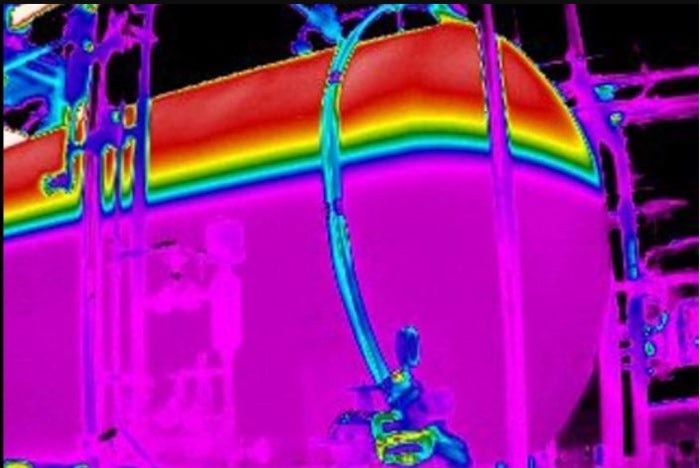
Steam systems and hot water systems can also benefit from infrared scannig.
Image by author
Other assets where infrared scanning can be used are pumps, steam systems, hot water systems, medical gas manifolds, vehicles, windows, doors and other such systems where a temperature is a normal indicator. The ability to scan an object and get a visual indicator of condition, and to record that as a graphic, dramatically improves AEM strategies by reducing costs, effort and risk. Emergency generator testing often uses stack temperature as a load indicator when no load balance is available, and an infrared scanner can be used to determine the temperature of the stack, reducing the risk of injury to the technician.
Finally, a major asset group that could benefit from infrared thermography in health care are refrigeration systems. Food, medications, supplies, transportation, etc., all depend on maintaining critical items at specific temperatures, with some items being so sensitive that even a few degrees off can cause the total loss of the items. Infrared scanners can be used to quickly identify temperature fluctuations, leaking seals, external and internal heat sources, and other defects that may be leading to a failure.
As our industry continues to become more sophisticated in design, application and equipment, it is crucial to leverage available technologies that help to drive down risk while also improving efficiencies. Looking at technologies used in other industries to perform similar functions allows us to jump-start those benefits into health care.
Rick Joslin has been in maintenance and services management since 1984, having performed as a technician, team lead, manager, director, and compliance & enforcement surveyor. Since 1999 he has helped almost 600 health care organizations implement industry best-practice and regulatory compliance functions within computerized maintenance management systems while also championing the need for organizational and industry-wide data standards that enable analytics of and support to total asset management, along with adoption of technologies and processes that increase efficiency and reduce risk.