Managing life safety deficiencies
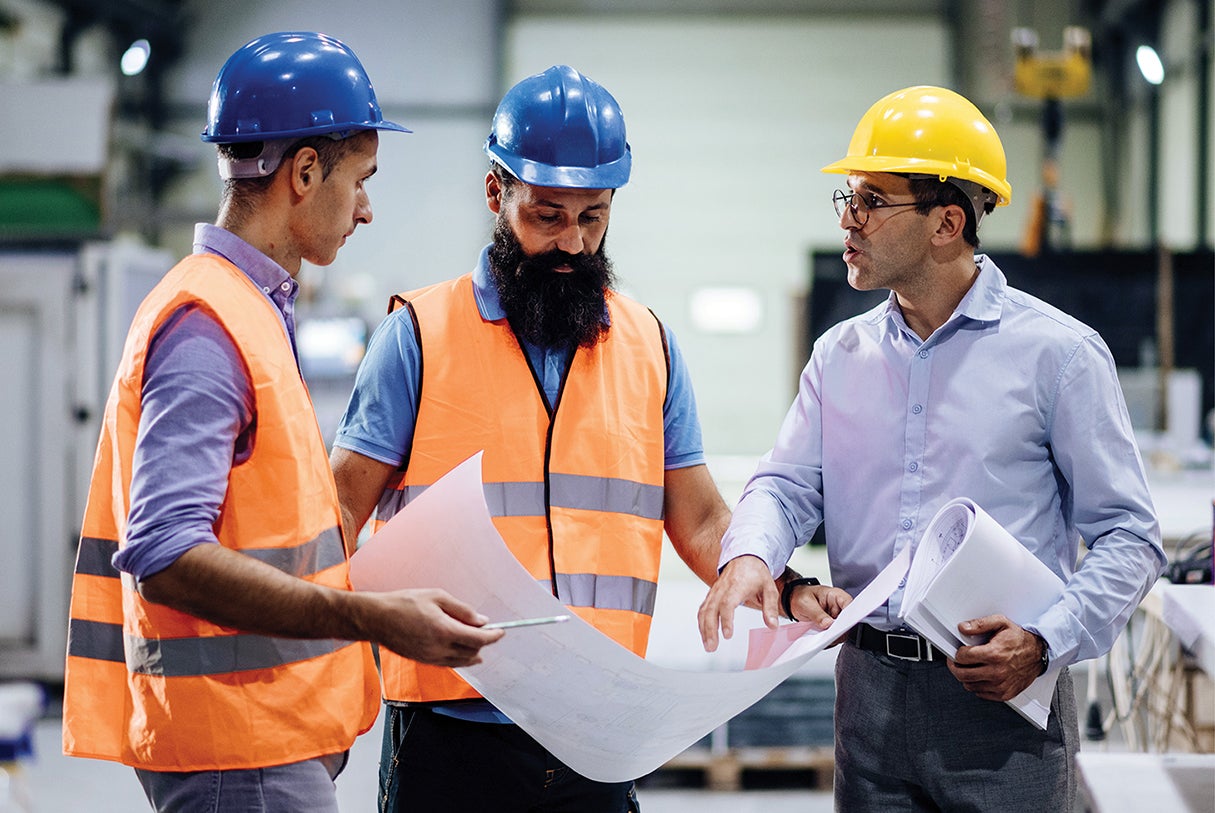
ILSMs, ALSMs and TLSMs are used when Life Safety Code deficiencies cannot be immediately corrected.
Image by Getty Images
Interim life safety measures (ILSMs), alternate life safety measures (ALSMs) or temporary life safety measures (TLSMs) are terms used by various accrediting organizations. They are actions or measures put into place during construction, renovation and maintenance activities or anytime National Fire Protection Association (NFPA) 101®, Life Safety Code®, deficiencies cannot be immediately corrected.
In many cases, an ILSM, ALSM or TLSM is performed in conjunction with a pre-construction risk assessment (PCRA) and an infection control risk assessment (ICRA). PCRAs and ICRAs are more often used for construction, renovation or heavier maintenance activities within or possibly outside a facility.
Examples of conditions affecting life safety are closing an exit; the use or storage of flammable materials on-site; installation of a dust barrier; blocked streets, driveways or access roads; impairment of the fire alarm system or suppression system; narrowing of corridors or removal of doors; and changes to smoke compartments, among others.
The ILSM, ALSM, and TLSM are developed by the health care organization, and the accrediting organization requires an assessment to determine if any are required. The Centers for Medicare & Medicaid Services (CMS) and other authorities having jurisdiction (AHJs) that utilize the Life Safety Code require compliance for these compensation measures for all new and existing occupancies.
Life safety measures
An ILSM, ALSM or TLSM is just what it states: an interim, alternate or temporary life safety measure put in place to make up for the lack of code compliance of a system or condition inside or outside the facility.
Facilities managers should remember that some temporary arrangements, such as adding a fire extinguisher or a temporary sprinkler system, converting smoke detectors to heat detectors or just adding heat detectors, require continued testing and inspection by qualified individuals.
Along with that testing and inspection, facilities managers should ensure the contractor provides the appropriate documentation before work starts, being sure all life safety measures selected are in place. Daily monitoring of the process is important to ensure the ILSM, ALSM or TLSM is being followed as outlined in the organization’s policy and the measures implemented (e.g., increased inspection frequencies) are effective.
One method to keep track of compliance with interim life safety is The Joint Commission’s (TJC’s) Life Safety & Environment of Care Document List and Review Tool. This tool is a guide for each standard and can be graded as either compliant or noncompliant with an explanation of the standard.
It is just one example of tools provided by accrediting organizations. TJC, Healthcare Facilities Accreditation Program (HFAP), and DNV Healthcare USA Inc. are accrediting organizations that many facilities use. They may have different names, but the standards are very similar in their intent to protect building occupants when the Life Safety Code cannot be met.
Health care facilities licensed exclusively by CMS should follow the guidelines listed in the CMS K-tag requirements. For deficiencies, health care facilities may use K-tag K791 “Construction, Repair, and Improvement Operations,” which references NFPA 101-2012 4.6.10 (as noted below) for guidance. The Life Safety Code provides the minimum design requirements for which a building is to be constructed and considered safe for occupant use, including:
- Subsection 4.6.6, Time Allowed for Compliance. Limited but reasonable time, commensurate with the magnitude of expenditure, disruption of services and degree of hazard, shall be allowed for compliance with any part of this code for existing buildings.
- Subsection 4.6.9.1, Conditions for Occupancy. No new construction or existing building shall be occupied in whole or part in violation of the provisions of this code unless the following conditions exist: 1) A plan of correction has been approved; 2) the occupancy classification remains the same; and 3) no serious life safety hazard exists as judged by the AHJ.
- Subsection 4.6.10, Construction, Repair, and Improvement Operations. This states that buildings are permitted to be occupied when under construction, repair or alteration only when the required means of egress and the required fire protection features are in place and continuously maintained in the area occupied or where ALSMs accepted by the AHJ are in place.
Facilities managers should remember to reference the applicable version of NFPA 101 codes and standards, including current state and local building and fire codes for the area, as well as other AHJs. Should standards and codes conflict, the most stringent standard or code should prevail.
According to an article on TJC’s website, facilities should have an effective interim life safety policy in place that includes ILSMs, a matrix and evidence to support standard compliance. This evidence of standard compliance should document all actions taken, planning and completion dates for the deficiency or deficiencies.
According to TJC, the policy should contain the following items: a document that the process is applicable to construction-related situations and situations of noncompliance with the Life Safety Code and documentation of the circumstances requiring an ILSM assessment, including wording that all statement of conditions are to be assessed for ILSMs.
Facilities managers should also explain how the organization will respond to situations described in the standards referenced in the Life Safety portion of 01.02.01; how occupants are to be protected by using the list of ILSMs described in the standards listed in the Life Safety portion of 01.02.01, as applicable to the situation; and the ILSM assessment process in the policy and an assessment tool to demonstrate which measure(s) will be implemented, or if no ILSM is required as a result of the assessment.
Facilities managers also should describe the ILSM implementation process in the health care organization’s policy. It should be effective throughout the duration of the deficiency(s) and include a way to document each implemented ILSM for the duration of its utilization.
TJC’s “Take 5” podcast has an episode titled “Interim Life Safety Measures Revisited,” in which Jim Kendig, TJC’s Life Safety Code field director, discusses ILSMs and the survey process. Topics include requirements for improvement (RFI), and what is required to implement processes to protect patients, staff and visitors until corrective actions are completed.
Changes in the TJC survey process that went into effect in 2016 included a survey-related plan for improvement (SPFI). Life safety deficiencies identified during a survey could be cited as RFI with a required 60-day completion date. These deficiencies will need to be entered on a SPFI, which will also feature a dropdown menu to identify which ILSM could be implemented for each deficiency. This process will be monitored electronically by TJC. Failure to complete the SPFI within the given time frame could generate a decision of accreditation with a follow-up survey.
HFAP was originally created in 1945 to conduct objective reviews of services provided by osteopathic hospitals and, over the years, has become a recognized accreditor for hospitals with either D.O. or M.D. programs. HFAP has maintained its deeming authority continuously since the inception of CMS in 1965 and meets or exceeds the standards required by CMS. Like all accrediting organizations, HFAP uses ALSMs for anytime that a life safety deficiency exists, not just during construction.
Facilities should maintain a complete ALSM policy. The policy is required to identify which measures, if any, impairment or deficiency to a portion of life safety is to receive. Anytime that a life safety requirement is not in compliance for fire alarm, sprinkler system, building component or egress standard, an ALSM must be implemented per the facility ALSM assessment and policy. An ALSM assessment must also be completed for all construction or modification work, even if the ALSM determination is that no compensating measures are required.
The accrediting organization DNV obtained CMS approval in 2008 for its hospital accreditation program. The following are a few of the DNV NIAHO® accreditation requirements, interpretive guidelines and the surveyor guidance, from Revision 18, published on Feb. 5, 2018:
- SR.7. The life safety management system shall address applicable ALSMs that shall be implemented whenever life safety features, systems or processes are impaired, or deficiencies are created or occur. Thorough documentation is required.
SR.7a. All alternative life safe measures must be approved by the local AHJ. Life safety measures for redundant and/or common minor renovations/repairs/testing may be preapproved for the specific task by the AHJ.
- SR.13. Construction, repair and improvement operations shall involve the following activities:
SR.13a. During construction, repairs, or improvement operations, or otherwise affecting the space, the Facility Guidelines Institute’s Guidelines for Design and Construction of Hospitals and Health Care Facilities, 2014 edition, shall be consulted for designing purposes.
SR.13b. The organization shall assess, document and minimize the impact of construction, repairs or improvement operations upon occupied area(s). The assessment shall include, but not be limited to, provisions for infection control, utility requirements, noise, vibration and ALSMs.
SR.13c. In occupied areas where construction, repairs or improvement operations occur, all required means of egress and required fire protection features shall be in place and continuously maintained or where alternative life safety measures acceptable to the local AHJ are in place. NFPA 241-1996, Standard for Safeguarding Construction, Alteration, and Demolition Operations, shall be referenced in identifying and implementing ALSMs.
SR.13d. All construction, repairs or improvement operations shall be in accordance with applicable NFPA 101-2012 standards, and state and local building and fire codes. Should standards and codes conflict, the most stringent standard or code shall prevail.
An ILSM, ALSM or TLSM assessment is a constantly changing document and one that needs to be regularly updated as the project or situation progresses. As the plan is updated and situations change, revisions should be posted as necessary and communicated to all affected parties and documented, including documentation of training for staff.
One common thing that comes up during surveys are missing ILSM, ALSM or TLSM measures for testing deficiencies. Anytime there is deficiency in the life safety testing and inspection reports, there should be documentation of repairs or replacement, including retesting and an assessment to see if an ILSM, ALSM or TLSM is required.
It is suggested that evaluations, plans and monitoring documentation should be kept for at least three years and presented to the Environment of Care Committee or Safety Committee as part of the quarterly and annual fire safety management report to the committee.
Ensuring safety
Regardless of which regulatory agency has jurisdiction, a good ILSM, ALSM or TLSM policy will help ensure the safety of patients, visitors and staff in all buildings.
One common method used for compliance is to include a matrix for determining the actions needed, a method to show the evidence of compliance and documentation of updates as situations change. Keeping the policy current and reviewing it at least annually with the safety committee will provide a dependable safety tool.
Working closely with the local AHJ during construction, renovation, major maintenance activities or anytime deficiencies in the Life Safety Code cannot be immediately corrected helps ensure any requirements are met or exceeded.
Conducting PCRA and ICRA on projects will bring other departments into the conversation and help ensure nothing is missed.
About this article
This is one of a series of monthly articles submitted by members of the American Society for Health Care Engineering’s Member Tools Task Force.
Mark Sears, SASHE, CHFM, CHSP, is the manager of safety services for Faith Regional Health Services, Norfolk, Neb.; and Jeffrey Henne, FASHE, CHC, CHSP, CHEP, CHFSM, is the safety and emergency manager for the Hospital of the University of Pennsylvania. They can be reached at msears@frhs.org and jeffrey.henne@pennmedicine.upenn.edu.