What facilities managers need from a digital twin handover
About this series: “Digital Twins” is a three-part series that introduces health care facilities managers to the world of digital twins. It offers a clear and practical overview of what digital twins are; the specific value they bring to health care; the role of planning, design and construction (PDC) in their implementation; and how to get started.
This second article builds on the “square peg, round hole” concept introduced in the first article, “The value of digital twins.” It revisits that analogy and explores how data is generated and how technology is used across different phases of the building life cycle. The article highlights where misalignments occur, why they persist and how the industry must evolve its building delivery processes to address them effectively.
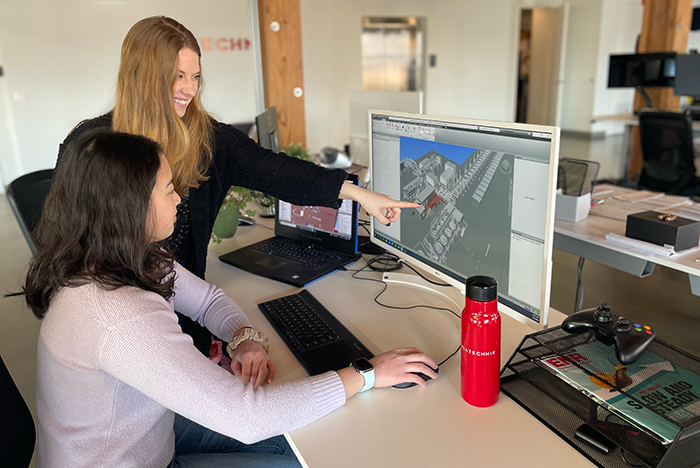
Moving digital twins from construction to operations requires close collaboration.
Image courtesy of VIATechnik
The architecture, engineering and construction industry often assumes that technologies used during design and construction — such as building information modeling (BIM) — will seamlessly carry over into operations and deliver the same value. While these tools have proven transformative for design and construction teams, their benefits rarely translate directly to facilities operations. This disconnect typically stems from a misalignment between the operational team’s needs and the value delivered during earlier project phases — a mismatch often referred to as the “square peg, round hole” dilemma.
At its core, this is not a technological problem; It’s a human one. Tools developed for one phase of the building life cycle often are not designed to meet the unique requirements of another. Addressing this challenge requires deeper engagement with facilities teams, a clearer understanding of their operational pain points and a willingness to adapt technologies to meet those needs.
The evolution of technology
As technology has advanced, it has both revealed and intensified the “square peg, round hole” issue across the building life cycle. Project teams and stakeholders often operate in silos, with limited understanding of the challenges faced outside their own phase. This lack of cross-phase visibility leads to misaligned expectations and incomplete solutions as a project transitions from one stage to the next.
Ironically, the same technological advancements that were intended to bridge these silos by enabling greater collaboration and data sharing also have made the disconnect more apparent. Data, tools, workflows and processes may now flow more freely between phases, but they are frequently misapplied. What works well during design or construction may not translate effectively into operations, where different objectives, timelines and performance metrics come into play.
This misalignment underscores the need to tailor technology and processes to the unique demands of each phase, rather than assuming a one-size-fits-all solution will work across the board.
Creation and utilization of data throughout the building life cycle
This article continues to explore the misalignment between project phases, now through the lens of data and technology. From the perspective of the health care facilities manager, the problem is not just the handoff of tools but the creation, delivery and eventual use of data throughout the building’s life cycle.
Design and construction. Over the past two decades, technology has dramatically reshaped how buildings are designed and constructed. Tools such as BIM have moved the industry beyond 2D drawings into highly coordinated 3D models. These models allow designers to better visualize space and help contractors resolve conflicts virtually, reducing costly errors in the field.
Beyond coordination and visualization, BIM also enables the structured creation of building data. Each model element, from architectural components to critical systems, can carry embedded metadata that supports asset tracking, maintenance planning and informed decision-making. For health care facilities managers, this structured asset-level data is more than a technical bonus — it’s a foundational operational resource.
Project handover. Despite advancements in technology, project handover remains one of the most difficult and underserved phases of the building life cycle. It typically takes place when tensions are high, timelines are tight, and teams are eager to move on. This phase often arrives when construction crews are racing to close out punch lists, owners are preparing for occupancy, and design professionals have already shifted their focus to the next project.
In the health care sector, where the volume and complexity of systems are substantial, handover becomes even more difficult. Facilities teams may receive scattered or incomplete documentation (if they receive it at all), forcing them to manage critical assets without institutional knowledge or formal records.
This is a missed opportunity. The same BIM model used throughout design and construction also can serve as a framework for organizing and delivering essential handover data. When leveraged effectively, this data becomes a bridge, carrying forward crucial information like asset locations, specifications and maintenance histories into the operational phase.
Building operations. Once a health care facility becomes operational, the environment is fast-paced, complex and high-stakes. Facilities managers rely on a suite of digital platforms to support daily operations — computerized maintenance management systems (CMMS) for maintenance, building management systems (BMS) for system controls, and integrated workplace management systems (IWMS) for space and asset management. Each of these tools depends on accurate, structured data to function properly.
If the data needed to populate these systems was never delivered or arrives incomplete, facilities teams are left to reconstruct it manually. This leads to duplicated efforts, inefficiencies and a higher risk of failure. On the other hand, when data is captured during design and construction and transferred properly, it serves as a powerful foundation for operational success.
The digital data deliverable
As digital twins gain traction as centralized access points for integrated building data, they are redefining how data is collected, shared and applied across the building life cycle. These platforms offer clear, measurable returns on investment, but only if they are built on a foundation of accurate and validated data.
This introduces a new and essential expectation: Structured digital data must be delivered at project handover. Transferring the data created throughout design and construction into operations is no longer optional. Rather it is a prerequisite for unlocking the full value of digital twins.
Yet this requirement also reinforces the ongoing challenge. When upstream teams fail to understand what facilities operations need, the wrong information, tools or formats often are delivered, exacerbating existing misalignments.
Solving this problem requires early and ongoing collaboration between stakeholders from planning, design, construction and operations. A shared understanding of which operational systems — CMMS, BMS, IWMS and others — will be populated is a critical starting point. Once those needs are identified, teams can use technology throughout the project to capture, structure and deliver the right data in the right format and at the right time.
The role of the digital delivery manager
As building projects increase in complexity, particularly in health care, the list of specialized consultants on a project team continues to grow. Commissioning agents, medical equipment planners and infection control experts have become common additions to project delivery teams due to their specialized knowledge and the criticality of their scope. Today, as structured data becomes equally critical to facility performance, another specialist is emerging: the digital delivery manager.
The importance of structured, validated data has reached a point where owners must consider a fundamental question: “Can we afford to open a new building without the data our facilities teams need to operate it effectively?”
In many cases, the answer is “no.” When facilities managers lack the right tools, data and technology at turnover, they are forced to operate at a disadvantage — chasing down documents, rebuilding asset inventories and manually populating operational systems. The cost of inefficiencies, downtime and rework quickly outweighs the investment in a consultant whose sole purpose is to ensure that the right digital information is delivered at the right time.
Enter the digital delivery manager — a dedicated consultant commissioned by the contractor, planning, design and construction (PDC) team or even the owner’s facilities department. Their responsibility is simple but critical: Deliver the required project handover data to the facilities team on time, validated and aligned with the owner’s operational processes.
This role is not just about compiling files at the end of construction. It requires engaging early, listening carefully to the facilities team and understanding how their platforms, such as CMMS, BMS and IWMS, need to be populated. The digital delivery manager works across project stakeholders to ensure that the data being collected during design and construction aligns with these operational requirements.
In this way, they directly address the “square peg, round hole” problem. Rather than retrofitting construction data for operational use after the fact, they shape the data strategy from the outset to meet facilities needs from Day One.
Facilities teams also can benefit from engaging with these consultants outside of active projects. By collaborating early before a shovel hits the ground, owners can define clear digital handover standards, naming conventions and platform requirements. This proactive planning helps future-proof building operations and ensures that technology continues to support long-term goals, not just short-term construction milestones.
For facilities managers, the value proposition is clear: Imagine a single consultant responsible for managing closeout documentation; enforcing naming standards; organizing operations and maintenance, shop drawings and warranties; and working directly with the operational platform teams to ensure that the data from design and construction flows seamlessly into the building’s CMMS, BMS and IWMS.
Embracing the shift
As the health care industry continues to embrace digital transformation, the need for intentional, cross-phase collaboration has never been greater. Solving the “square peg, round hole” problem starts with listening to facilities teams, defining operational needs early and ensuring that technology — and the data it generates — serves those needs throughout the building life cycle. Whether through dedicated roles like a digital delivery manager or through standardized data expectations at handover, the future of facilities operations depends on how we align people, processes and technology from Day One.
We want to hear from you
To continue this important conversation, American Society for Health Care Engineering (ASHE) President-elect Dennis Ford and I will be speaking at the Health Care Facilities Innovation Conference™ in Columbus, Ohio, sharing insights on digital delivery and the evolution of data in health care construction. Join us for the breakout session titled “The Rise of Digital Owner Representation in Healthcare Construction,” which will take place July 28 at 4 p.m. local time.
In addition, we’re proud to be partnering with other ASHE leadership on a digital twin focus group that will help to shape the definition and future direction of digital twin adoption across the industry.
If you're a health care facilities professional navigating this shift or helping others prepare for it, now is the time to engage. The conversation is happening. Make sure your voice is part of it.
Jacob D’Albora, FMP, is a subject matter expert in building data and its application during building operations, with a focus on health care facilities management and driving innovation in the architecture, engineering and construction industry. He is the director of digital building operations at VIATechnik, a consulting and services firm dedicated to advancing the digital transformation in the built environment. He can be reached at Jacob.dalbora@viatechnik.com.