Inspecting hospital building envelopes
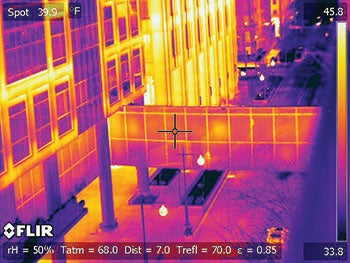
Infrared thermography can be used to identify thermal anomalies associated with heat transfer, air leakage or moisture.
Maintaining and preserving the building envelope is an important part of a successful operations program, especially for facilities with critical interior spaces.
The building envelope represents an essential boundary between the exterior environment and interior conditioned space. It must effectively control and respond to the environmental loads to maintain environmental separation and prevent problems related to durability, water intrusion and indoor air quality.
You may also like |
Conducting a building assessment |
Resilient health care facility design |
Building materials for hospital construction |
|
Through a fundamental understanding of architectural concepts and implementation of an effective maintenance program that’s aligned with product manufacturers’ warranties, a facility will sustain performance, identify problems early, and extend the service life of the envelope materials and components.
Envelope fundamentals
Health facilities professionals must have a fundamental understanding of how the building envelope is designed and constructed to provide environmental separation, especially when attempting to resolve a problem or failure. For example, one common mistake of a facility maintenance staff is to install sealants or caulking where they do not belong.
If a weep hole, which is designed to allow water to drain from an assembly, is observed opposite an interior leak, it seems intuitive to simply seal that hole. However, sealing weep holes may exacerbate the problem. With a proper understanding of how the wall system works and is designed to function, mistakes like this can be avoided.
Building envelope wall systems often are designed as barrier, drainable cavity or mass assemblies. Barrier systems rely solely on the outer surface of the wall to control and shed exterior precipitation. These systems must maintain a fully sealed, watertight exterior surface to effectively control water. Common barrier systems include precast spandrel panels and fully sealed metal panel systems. Cavity assemblies employ an exterior cladding or layer that sheds most exterior precipitation and rely on an interior drainage plane that functions as the primary control layer. An example of a cavity or drainage assembly is a drained masonry or other clad wall.
Although mass assemblies rarely are designed on new projects, they have been used successfully throughout much of history. In general, they rely on the capacity of the envelope material to store moisture. Most mass walls are constructed with masonry. Roof systems can have similar design concepts. Some systems rely on an exposed outer membrane that is responsible for controlling air and water intrusion, while ballasted or protected membrane roof systems maintain a protection material on the exterior side of the primary control layer.
Generally, envelope systems designed as barrier assemblies require and facilitate more maintenance than concealed layers of cavity assemblies. Concealed materials must be durable because they are not accessible. However, if a concealed control layer was not properly manufactured or installed, the resolution of the problem can be costly because exterior or interior finishes must be removed to access the material.
Inspection and maintenance
With demanding occupant requirements and frequently overworked operations staff, a proactive inspection of a building’s envelope without an obvious problem may seem like a waste of time, but it’s not.
Sometimes, envelope failures already have occurred and are only unnoticed. For instance, a leaking roof could be quietly draining water into the building where mold and rot are degrading building materials, but hidden from view with a fresh coat of paint.
With an inspection program, that failure could have been identified prior to its becoming a serious issue. This early detection could result in the availability of a patient room that otherwise would have been closed. Preserving the envelope, catching problems and minimizing large capital expenditures are a few of the benefits of a successful maintenance program. It is generally accepted that an effective building envelope maintenance program is part of every high-performance building, especially health care facilities.
A building owner can design a building envelope maintenance program in a number of ways. However, development of a comprehensive maintenance log is often the first step in implementation. Most logs include original or as-built design documents, warranty documentation and maintenance checklists. The checklists typically include a list of systems to be inspected such as the roof and sealants, along with a list of things to look for.
Many manufacturers provide maintenance inspection checklists for building owners, so this may be a good place to start. The checklists must summarize typical failure or distress mechanisms, but also leave space for a description of an issue that isn’t captured within the checklist. The documentation can be valuable when analyzing repair strategies and for anticipating replacements.
A large portion of building envelope maintenance issues and failures often occurs at the interfaces between systems. Inspection checklists should include items associated with individual systems, but also focus on the system interfaces. Hospital complexes often consist of multiple buildings, constructed at various times throughout the life of the property, with each building consisting of a different building envelope system that was popular during the time of the facility expansion. This ongoing construction results in transitions between many different envelope systems.
Transitions between different building envelope systems commonly require maintenance or repair. The transition between a 1930s-era mass masonry wall and a 1980s-era drainable brick cavity wall may be more prone to failures than the transition between two similarly constructed systems. Interconnected properties also have a high number of expansion joints where the envelope will move while remaining air- and water-tight.
Evaluations should not exclude parking structures common to many hospitals. Parking structures are unique in that the structural components are exposed to the elements and therefore require similar considerations as building envelope components on occupied buildings.
Identification of the inspection regimen and schedule is next. Most roofing manufacturers recommend that their roof systems be inspected twice per year at minimum, commonly in late fall and early spring. Degradation of building envelope components often can be attributed to the level of exposure and movement, such as thermal or structural. Therefore, the frequency of inspections may be based partially on the anticipated rate of degradation and associated risk. Vertical sealant joints do not have the exposure of the roof and, therefore, may not require an inspection cycle as frequent. Conducting the envelope inspection a minimum of twice a year is likely a best practice. Severe weather events also may initiate an inspection.
Many building envelope visual observations are performed from the exterior, and are not intrusive on the operations of a facility. However, care must still be taken to notify all appropriate staff of the work being performed, however minor. Security personnel should be fully aware that one or more people will be photographing the property. Privacy of hospital tenants and staff during the execution of these tasks should be reviewed with appropriate personnel. Communication prior to performing investigative tasks can help to prevent unnecessary distress. Certainly, the safety requirements also should be fully understood by maintenance staff prior to conducting an inspection.
Subsequent to adequate training and preparation, an inspection can begin. Based on access and building geometry, binoculars may be helpful to provide the magnification required to identify a deficiency. If closer examination is required, lifts or swing stages may be needed. Some envelope systems can be complex. If it appears that something is wrong, document the condition, and research it later. Sometimes, conducting the inspection immediately after a rain can be helpful to indicate how systems are draining. For example, ponding water adjacent to roof drains may indicate a clogged drain or improper slope. Photographs during the inspection not only document a condition, but can help identify changes during future inspections.
Some failures or issues are not easily observable. Missing or displaced insulation or air leakage can contribute significantly to energy losses, but easily can go undetected. In these cases, the building automation system frequently is overridden to sustain comfortable interior conditions in areas of the building that have difficulty maintaining set points. Tests can be conducted to identify air leakage or missing insulation. Some methods include infrared thermography or air leakage testing. Most qualitative tests like thermography rely heavily on the experience of the person conducting the test.
Finally, consider printing 11-by-17-inch sheets with elevations and plans of the building. Each observation can be noted on the sheet so the location is clearly identified. Programs also are available on handheld electronic devices that facilitate electronic notations.
Addressing failures
After a failure is identified, the next step is to consider repair options to correct the building envelope deficiencies found during the evaluation. Most involved parties will be anxious to implement repairs, which should be performed in a timely manner.
Immediate safety measures can be addressed quickly and small maintenance items addressed in the short term. Larger long-term repairs however, may require time for thorough evaluation and design. This tends to be especially true for water leaks. Finally, it is important for all staff to recognize that repairs or modifications should never be conducted on a material or system that is still under warranty without consulting the manufacturer.
It’s not surprising that building failures related to the envelope represent a large portion of overall building failures. Commonly cited statistics often claim that envelope failures are responsible for 50–75 percent of construction defect claims. These types of envelope failures are commonly related to moisture or durability with severity ranging from barely noticeable to tremendously dangerous. A failure can be initiated through numerous mechanisms, including any or a combination of design or construction defects, weather exposure, material reaching the end of its service life and inadequate maintenance.
Some failures clearly may be related to a specific material while other failures may not be as easily discernible. Identifying the source of water leakage into a building can be challenging and often requires extensive investigation. While the water may enter the building at one location, the actual cause may be completely unrelated to where the leakage was observed.
Once a failure is observed, the first step is to identify potential safety risks. The difference between a building enclosure failure that is a safety hazard and a component that merely requires routine maintenance may be difficult to diagnose. If there is any question about the severity of a condition, an expert or specialist can provide the information that a facility manager needs to make the best decision regarding safety.
For example, cracks in a wall surface in a highly visible area near a hospital entrance may result in a high number of concerned calls to property management, but may not necessarily be a cause for concern. Shrinkage cracks in a concrete spandrel panel, while unsightly, might not require immediate attention. Meanwhile, smaller, less visible cracks in the same concrete spandrel panel near a structural connection could be a safety hazard or lead to water intrusion.
While structural issues can pose immediate safety hazards, water leakage also can result in health hazards because wet materials are significantly more prone to biological growth.
If mold or other biological growth is discovered, an industrial hygienist or similar professional can help to diagnose the type and extent of growth. An extensive abatement, investigation and repair program could be required immediately for these situations.
If the failure is not an immediate safety concern, documentation of the conditions when the failure occurs can be important to beginning an investigation. For water leakage, interior and exterior air temperatures and relative humidity levels, wind speed/direction, building pressures, location of water leakage, and quantitative descriptions of the leakage are all important factors to document.
An integral part
Building envelopes often are considered static and durable systems that require little or no maintenance. This is becoming less true as many new facilities are designed and built with lower budgets, tighter schedules and more complex materials.
Building owners are becoming more sensitive to existing building preservation, costs associated with failures and energy consumption. Likewise, occupants are becoming more sensitive to healthy buildings and indoor air quality.
It has never been clearer that an effective building envelope maintenance program is an integral part of operating a high-performance health care facility.
Rick Ziegler, PE, RRO, is a principal and Greg Isaacs, PE, is an engineer with Smith Seckman Reid Inc., Nashville, Tenn.; both specialize in building enclosure consulting and commissioning. They can be reached at rziegler@ssr-inc.com and gisaacs@ssr-inc.com, respectively.
Knowing where to look for envelope failures
Knowing where to look makes a big difference in identifying potential maintenance issues and causes of envelope failures. This list summarizes examples of important systems to check and key things to look for:
Wall systems. It would be impossible to identify specific items to look for related to every wall type. However, the following should be checked:
• Cracks or voids within sealant surfaces, which may indicate that the sealant is at or near the end of its service life.
• Sealants, which must maintain a continuous bond with the adjacent substrates.
• Cracks within the wall systems, which can be completely normal and within acceptable tolerances or could indicate a problem.
• Discoloration within wall assemblies due to efflorescence, rust or other factors, which can provide clues as to how the wall is functioning.
• Flashings and associated weeps, which must be maintained free and clear so that water effectively drains to the exterior.
Roofing. Due to the orientation, exposure and foot traffic applied to roof assemblies, roofing evaluations are vital during maintenance reviews. Health facilities professionals should do the following:
• Make sure roof drains are clear of such debris as leaves and dirt to allow clear operation.
• Ensure that flat surfaces are clear of debris, because sharp objects can puncture roof membrane surfaces, especially in areas with heavy foot traffic like those adjacent to HVAC units.
Windows and doors. While metal and glass components of windows and doors can be durable, sealants and gaskets can wear. Health facilities professionals should check the following:
• Weep holes within window systems, so they remain clean and free of debris.
• Gaskets for placement, location, staining and shrinkage, all of which can indicate that they are approaching the end of their service lives.
• Sealants within windows and doors and at perimeter joints.
Working with an outside expert
Health facilities professionals may want to hire a building envelope specialist in the case of complex failures, comprehensive maintenance reviews or general condition surveys. With the right information, an expert could develop a proposal for the requested scope of work.
Documentation of the envelope conditions or failures throughout the building history can provide an expert with background information on the project. Other considerations:
• Most experts will require safe access as well as sources of electric power or water. For example, water leakage investigations often require water spray testing to attempt to re-create the water leakage.
• Weather may influence when an expert can conduct the work. Thermography is often most beneficial with a specified air temperature differential between interior and exterior conditions, and water testing cannot be conducted at very cold temperatures.
• Removal of building components is almost always beneficial during failure investigations. Most experts will not remove these components, and a contractor must be hired to remove and replace materials as directed.
An expert who can provide comprehensive reports, including prioritization of issues, development of repair options or documented solutions, can be found through industry organizations such as RCI Inc., Raleigh, N.C., or local building enclosure councils.