How to ensure central utility plant reliability
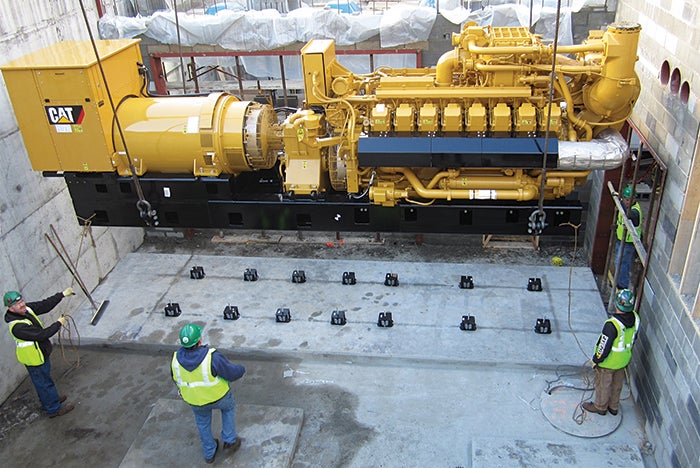
A generator set being lifted into a mechanical pit at Upper Chesapeake Medical Center in Bel Air, Md.
A hospital’s critical power supply and all associated components must function properly at all times. With myriad life-saving equipment, operating rooms and computerized systems in hospitals, central utility plants (CUPs) ensure that patients can depend on reliable, uninterrupted power and other utilities.
You may also like |
Modular central plant offers flexibility |
Alternative utility equipment maintenance requirements |
Phoenix Children’s central plant goes green |
|
Keeping it flowing means being prepared for the worst, such as the destruction left by hurricanes, earthquakes, tornados and floods — when hospitals become an even more vital community resource. At these times, facilities must be prepared to protect themselves and respond to the influx of patients.
U.S. hospitals spend nearly $5 billion annually on energy and related costs. Energy comprises a little more than half a typical hospital operating and maintenance budget. Mechanical and related systems make up more than 70 percent of that energy use in hospitals, with mechanical reheating and cooling consuming more than half.
Clearly, systems supplying facilities and life-saving technologies influence the organization’s bottom line.
Balancing the challenges
Virtually every hospital modernization project must balance the challenges of building systems that meet the current electrical loads and code requirements, are flexible enough to meet growing and changing hospital needs while at the same time meet budget constraints and are constructible.
Because most new health care construction is often an addition to an existing site, the first step is to investigate and analyze. This is the phase in which a team of engineers and designers investigates, and confirms and documents the hospital's electrical infrastructure.
All too often in many hospital expansion and modernization projects, the natural tendency of electrical design engineers is to avoid older or non-code-compliant electrical infrastructure and equipment. Often it is easier to install new equipment to serve the new project area, but sometimes the best solution for the hospital is to clean up existing distribution equipment or systems that are not in compliance with National Electrical Code requirements.
Every phase, from concept to commissioning and operations and maintenance, is executed with a construction-driven mindset. For example, engineering and procurement activities are based on creating a holistic better-build approach. Through intensive planning, starting in the front-end stage, the project determines the path of construction, developing engineering and construction work packages in accordance with the construction sequence and significantly improving efficiency.
Additionally, most main hospital buildings in the U.S. are more than 20 years old, which means a significant portion of that spending could be curbed through improvements in energy use.
According to the J.P. Morgan white paper, “Energy Performance Contract Financing as a Strategy: Transforming Healthcare Facilities Maintenance,” both public and private hospitals have worked hard to control their operating costs in the face of thinning margins, an uncertain economy and a challenging regulatory environment. As a result, many organizations face difficult decisions between maintenance and infrastructure improvements, while assuring quality patient care.
The CUP is high on the list of the complex components in any hospital’s infrastructure. Combining the immediate benefits of energy-efficiency upgrades to existing systems with an investment in new and reliable on-site energy infrastructure provides compelling financial, operational and environmental benefits.
Planning and logistics
Communications, coordination and planning are important throughout any renovation. However, the challenges facing building owners and facility executives [planning a renovation] are magnified on a health care campus. Specifically, infection control, utility loads, switchovers, service to physicians and patients, and the impact of design on existing facilities and activities all are critical issues that must be addressed in the health care environment.
The analysis of loads and capacities extends from the major power and HVAC utilities to medical gases and pneumatic systems. At the planning stage, the design and construction team not only must address load and capacity, but also the strategy to be followed when the utility shutdown and cutover occur during construction.
Building a state-of-the-art hospital with complex mechanical, electrical and plumbing (MEP) systems requires the utilization of the latest advancements in design and construction technology as well as an experienced and collaborative team. Constant communication is the key factor in initializing various phases of construction to safeguard patients, doctors, administration, faculty and emergency traffic flow against any disruption.
Building information modeling (BIM) is now essential to mitigating logistical challenges and improving communication and coordination in any project. BIM methodology helps to avoid conflicts among the trades through systems clash-detection. BIM also will help with the scheduling of the MEP trades and can aid the team in structural design and tie-in to the existing facility. Additionally, a BIM execution plan establishes goals and processes to integrate BIM at every level. Within the plan, individual roles and responsibilities are clearly defined, including meetings and protocols.
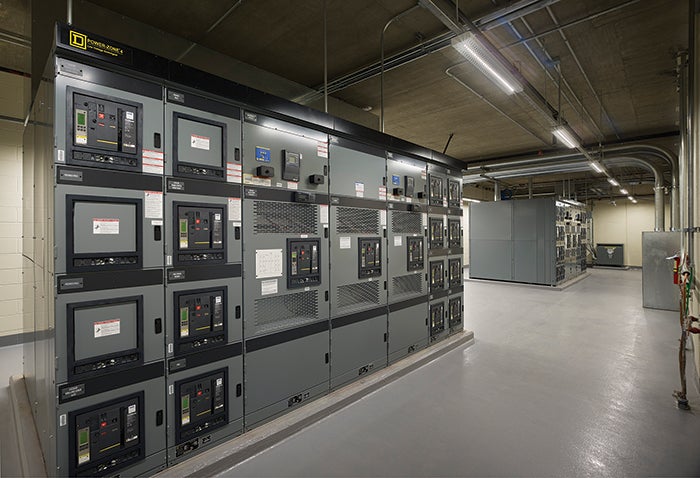
Distribution switchgear is a key component for proper operation of emergency power systems.
Maintaining a CUP during construction is no small feat. The project team has to be as unobtrusive as possible while conducting complex construction activity near and throughout the existing facilities and infrastructure. The renovation and expansion of a CUP also should be done in phases to maintain uninterrupted operation and service of essential utilities.
Logistics planning in a health care renovation project can be more difficult than the work itself. For that reason, regular coordination with the facilities staff before, during and after a renovation project is essential and will help to avoid any unnecessary rework expenses.
An important component to help with the logistical challenges is to build a sequential timeline for disruptions related to the new project. It is key to schedule shutdowns with minimal impact to existing operations and maximum efficiency during construction.
One way to control this process is to set a regularly occurring "disruption meeting" with the integrated team and key hospital operational personnel to review the construction schedule of activities and any touchpoints with the existing infrastructure. It is important to include all stakeholders in these meetings to minimize problems.
New vs. existing
There are different considerations for CUPs installed in new facilities and those installed in existing facilities.
CUPs for new facilities. There are exciting opportunities when designing a CUP for use at a new medical campus, particularly to incorporate lessons learned during natural disasters that severely damaged health care campuses. Not only does the CUP need to last for the projected life span of the hospital campus itself, but it also needs to be expandable, adaptable and easy to replace as dictated by changes in available technology and the needs of the campus.
The new CUP’s design has the chance to make a significant energy-reduction impact. Sustainability is a major consideration in health care and the CUP often incorporates many green features. For example, heat that normally would be discharged and wasted may be harnessed to reheat surgical suites; and water for the cooling towers may be supplied, in part, from rain water collected and stored on-site, protecting natural resources and helping to reduce utility costs.
Future expansion may not require additional space for more equipment because the existing equipment may be upgraded. However, it is very important to design adequate access for the removal and replacement of the type of machinery involved with the CUP, such as chillers, generators and tanks. The facility’s design also should include a way for this equipment to be moved; for instance, with steel beams in the ceiling and the rooms’ removable access walls.
Building technologies play an important role in delivering better health care at lower costs and a CUP is key in that objective. Resiliency, sustainability and long-term operational flexibility are the driving forces that shape the design. New construction is a chance to install advanced, energy-efficient technologies because a sustainable building that is operating at a lower energy benchmark can stretch its emergency capacity over a longer period.
Careful consideration should be given to the overall design of the CUP, not just its form, but how it will interact with the campus and the environment. In many instances, the CUP is placed in the same building as deliveries or other back-of-the-house functions. Placing a CUP near a loading dock can cause humidity and associated bacteria control issues because nearby doors are frequently open.
These issues are compounded by the geographical location and season, causing unwanted humidity and condensation problems in the loading bays. To rectify this, engineers should design the building to maintain positive pressure in open areas, such as loading docks or other HVAC rooms where humidity can enter.
In some instances, health care mechanical systems are not properly designed for their geographic locations. For example, an engineer experienced only in designing for the Northwest might include elevator relief vents that are not conditioned for a facility in the Southeast. This design will pull hot, humid air continually into the shafts, allowing mold growth. This is obviously undesirable, which an engineer from that region would know. Viewing systems online and what can occur in different environments can minimize or eliminate these design mistakes.
The earlier the engineering group becomes involved with the contractors and the facility’s maintenance staff, the better the chance of avoiding issues such as these. Additionally, it’s imperative that the engineering group conduct site visits to ensure that the design performs as expected once the system is brought online.
Utilizing a holistic integration process when approaching a medical campus’ CUP helps to create a modern campus that is both capable of meeting today's health care needs as well as one that allows for greater ease of adoption to future changes in health care technology.
A CUP need not be relegated to a far-off corner on campus. To make sustainability and the importance of conservation front-and-center, a forward-thinking design and construction that makes the facility very visible and very prominent not only will speak to what it does, but also promote these important objectives.
CUPs for existing facilities. With an increased emphasis on expanding and renovating existing medical facilities and campuses, it is critical to understand how CUPs are maintained during construction and renovation, and how to overcome the challenges of seamlessly tying an existing and new system together.
Working with an integrated design team of architects, engineers, construction managers, subcontractors and commissioning agents helps to guarantee that no adverse impact occurs to hospital operations. It’s imperative to work closely with the hospital’s engineers and facility maintenance team to devise a plan that enables the completion of this sensitive infrastructure project while mitigating disruption.
The planning, design and construction of a new CUP into an existing facility requires an intensive preconstruction and construction coordination effort that includes a thorough plan for continuing day-to-day uninterrupted operation. An unplanned outage or equipment failure can result in the inability to treat patients, which can have significant safety and cost ramifications. Sound central plant design and planning is the first step in creating a reliable, economical and maintainable system.
Implementing a design-assist delivery and gathering the subcontractors’ input allows the team to proactively engage in cost-saving suggestions to bring the mechanical and electrical trades into the process early. Upholding tenets of an integrated design and construction approach, the construction team, architects, engineers and contractors must work cohesively — from concept through substantial completion — to deliver a successful CUP facility.
From an aesthetic standpoint, CUPs are being designed to fit in with the existing campus architecture. In some cases, screens, walls, louvers and openings are being used to allow the equipment to breathe, while concealing mechanical equipment and piping from public view.
Coordination of new and existing MEP as well as tie-in with the existing facility structure is critical due to the multitude of systems that have to be rerouted for new construction. Rerouted systems include normal power, emergency power, steam, pumped condensate return, chilled water supply and return, domestic water, storm, sewer, fire sprinkler, nurse call, data, telephone, paging, and distributed antenna and cable TV.
It is important to schedule shutdowns with minimal impact to existing operations and still allow for maximum efficiency during construction.
When existing equipment gets integrated into a new system, it is imperative that the existing equipment is fully restarted, tested and commissioned to ensure that the entire system is synchronized.
Like other industries, health care has embraced sustainable practices in the construction, renovation and operation of medical campuses. Given that these campuses are large consumers of water and power, there is substantial chance to improve efficiency as systems are renovated or replaced. There are also opportunities for the adoption of cutting-edge technologies, such as cogeneration and the use of recycled water.
Many health care organizations are setting sustainable goals for the CUP to be a new standard for energy efficiency, water conservation, utilization of recycled materials, and protection of air quality; and to utilize all possible efforts to conserve and preserve natural resources.
Essential investments
The investment in infrastructure systems to ensure continuous operations is essential for health care facilities.
The health care organizations that embrace and implement advanced technologies, redundancies and sustainable upgrades are well-prepared for future physical growth.
Jim Salvino is a mechanical-electrical-plumbing executive with Clark Construction Group, based in Bethesda, Md. He has been part of several complex health care projects for clients including Inova Health System and Johns Hopkins University. He can be contacted at james.salvino@clarkconstruction.com.