National pride
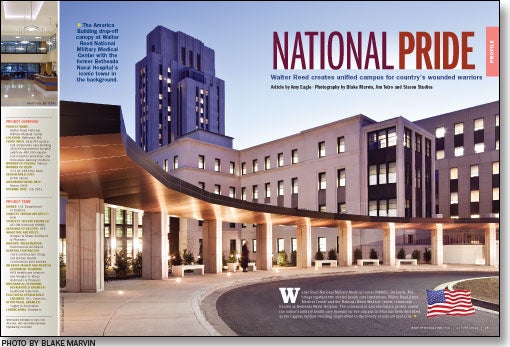
Project Overview
- Project Name: Walter Reed National Military Medical Center
- Location: Bethesda, Md.
- Floor area: 515,000-square-foot ambulatory care building; 162,000-square-foot hospital addition; 450,000-square-foot hospital renovation; and 943-space parking structure
- Number of floors: Various
- Number of beds: 174 (of 345 total beds)
- Design-build cost: $755 million
- Groundbreaking date: March 2008
- Opening date: July 2011
Project Team
- Owner: U.S. Department of Defense
- Concept design architect: HOK
- Concept design engineer: AECOM (formerly HSMM)
- Designer of record: HKS
- Associate architect: Wingler & Sharp Architects & Planners
- Historic preservation: Hartman-Cox Architects
- General contractor: Clark Construction Group and Balfour Beatty Construction joint venture
- Interior design and medical equipment planning: HKS Healthcare Interiors and Wingler & Sharp Architects & Planners
- Mechanical/plumbing design-build engineer: Southland Industries
- Electrical design-build engineer: M.C. Dean Inc.
- Structural engineer: Cagley & Associates
- Landscaping: Dewberry
Information provided by Clark Construction, HKS and Naval Facilities Engineering Command
Walter Reed National Military Medical Center (NMMC), Bethesda, Md., brings together two storied health care institutions, Walter Reed Army Medical Center and the National Naval Medical Center, commonly known as Bethesda Naval Hospital. The construction and renovation project united the nation's military health care systems on one campus in what has been described as the biggest, farthest-reaching single event in the history of military medicine.
"The simple fact that the services that we're providing are all in a singular location is a huge benefit to our wounded warriors and their families," says Captain David A. Bitonti, D.M.D., U.S. Navy, who served as chief of staff for integration and transition, Walter Reed NMMC.
The project was delivered through a design-build contract by a joint venture of HKS, Dallas; Clark Construction Group, Bethesda; and Balfour Beatty Construction, Dallas; in association with Wingler & Sharp Architects & Planners, Wichita Falls, Texas; Hartman-Cox Architects, Washington, D.C.; mechanical contractor Southland Industries, Garden Grove, Calif.; and electrical and systems integration firm M.C. Dean, Dulles, Va. All new construction received a Leadership in Energy and Environmental Design (LEED) Gold rating.
The medical planning, architectural and engineering conceptual design was developed by a joint venture between the New York and Washington, D.C., offices of HOK and engineering partner AECOM (formerly HSMM), Los Angeles; the joint venture continued to support the Department of Defense throughout construction with a post-construction award services contract.
Bitonti says it was a challenge to be "building a hospital while operating a hospital during an active war," but two priorities kept the project focused: patient and staff safety and Joint Commission readiness. "We maintained both of those throughout the entire process," he says.
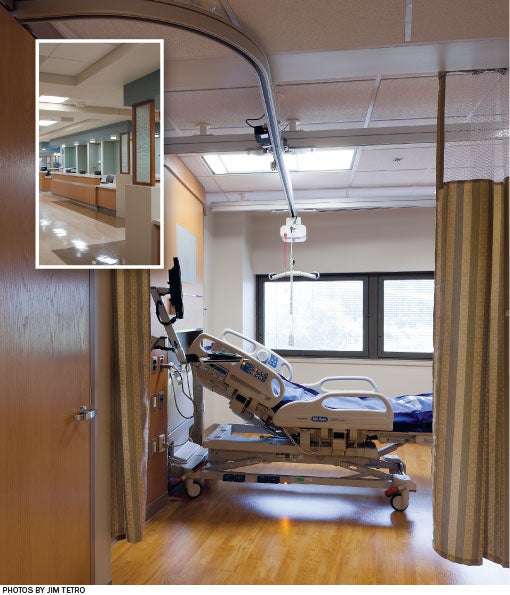
For Patients and Caregivers. Right: The hospital has 110 new single-patient rooms that include built-in headwalls, private bathrooms and patient lifts. Inset: The evidence-based approach led to nursing and charting stations that reduce walking distances.
Towering presence
The campus features an iconic tower from the original Naval Medical Center, designed by consulting architect Paul Philippe Cret from a rough sketch by President Franklin D. Roosevelt. The tower, which is listed on the National Register of Historic Places, is "Washington's only skyscraper," says Bill Hellmuth, AIA, LEED AP BD+C, president, HOK. "It's part of our national psyche, and it's a pretty important building in terms of the history of health care. It's incredibly important to respect that."
Over the years, some large buildings have been added to the medical center that are robust health facilities but not very compatible with the original design, Hellmuth says. One major goal of the Walter Reed NMMC project was to create a campus that worked well from a programming standpoint and appeared as a unified whole.
Two new structures, an ambulatory care facility called the America Building and an inpatient facility known as the Arrowhead Building, were built on either side of the hospital tower, adjoining existing medical center structures. The symmetrical design sets off the tower as the central element of the campus and places medical services in locations that relate well to existing departments.
The exterior of the original building is precast concrete mixed with ground glass for a luminous effect. Precast concrete with a similar luminosity was used on the exterior of the America and Arrowhead buildings. Vertical design elements of the new buildings also complement the original structure. A new parking structure built as part of the project is designed to harmonize with the original building as well.
To preserve the appearance of the historic facility, the height of the America and Arrowhead buildings could not exceed that of the original hospital wings. The two new buildings have the same front elevation, but they are quite different structurally; the six-story America ambulatory care facility is made of concrete and the four-story Arrowhead inpatient facility has a structural steel frame.
The use of structural steel allowed the inpatient building to have a floor-to-floor height of 14 feet, 10 inches, compared with the 12-foot, 6-inch floor-to-floor height of the ambulatory care building, explains Joe Hogan, vice president, Clark Construction, project director of the Clark/Balfour Beatty joint venture. Steel also was determined to be the best support for a section of the inpatient building that cantilevers over an existing structure.
As the builders were procuring steel for the inpatient building, they were able to proceed with the concrete operation for the much larger ambulatory care facility. "We wanted to be in the ground within four-and-a-half months of award, so as soon as we had design under way, we broke it up into packages," Hogan says.
Advanced technology
The America Building outpatient facility has a spacious, multistory lobby and a central light well featuring a hardscape sculpture and a mosaic tile mural. Clinic waiting areas surround the light well, which provides natural light throughout the building. The light well also serves as a point of reference for wayfinding. "[It's] a very good experience for the patient. Very simple for them and very elegant," says Brent Willson, AIA, FHFI, associate principal/senior vice president, HKS.
The America Building has a number of sophisticated rehabilitation environments, including a gait lab that can create three-dimensional images of patients' movements using motion-analysis equipment; a computer-assisted rehabilitative environment lab that allows patients to practice using prosthetics in virtual reality settings; and a computer-based firearms training simulator lab.
Advanced radiation oncology equipment, including three linear accelerators, also is installed in the building.
Willson says the clinical staff, designers and builders worked together to incorporate technologies that were evolving as the project was under way.
'Everyone has a piece'
"We had a great sense of pride building this facility," says Hogan. Bitonti believes the entire country should share in this pride. Walter Reed NMMC bills itself as the nation's medical center. "We mean that truly," he says. "Everyone in the nation has a piece of what we accomplished here."
Amy Eagle is a freelance writer based in Homewood, Ill., and a regular contributor.
Sidebar - Project planning minimizes disruptions to patient care
Sidebar - Design-build strategy helps maintain project budget and quality
Sidebar - SPEC SHEET