Planning a consolidated clinical testing facility
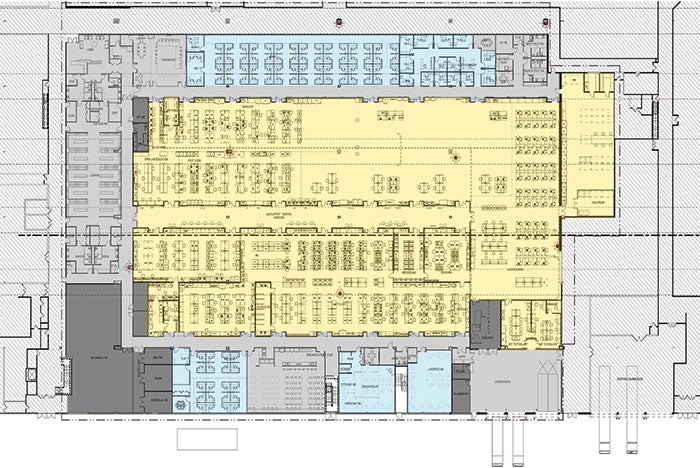
An open-lab concept allows the greatest flexibility of space for future change with functional separations only where required.
A variety of programmatic and design issues impact the planning of a consolidated clinical testing (core) lab. While program theoretically comes before design, the issues are intertwined. The following categories of planning and design considerations — all of which are relevant to creating a successful facility solution — are therefore not sequential, even though the first two are the likely initial steps in the process.
- The operational concept. Programming the space begins with an understanding of the staffing model, which includes everything from hours of operation and the work-shift strategy to safety protocols and cleaning procedures. Then comes the development of a logistical plan for sample management along the entire chain of custody control, including receiving, sample login, distribution, testing, reporting, freezer or cold-room storage, waste removal and management of consumables. Equipment-related optimization issues like capacity modeling, throughput analysis and backup strategy round out this operational strategy.
- Organization of flows. Applying Lean principles, the team then tackles work cell development with sample flows and efficient use of equipment and space and evaluates layout opportunities as well as personnel, equipment, sample and waste flows. Flow analysis is used to confirm contamination control, sample integrity and protocols anticipated. The team looks for opportunities for preventing contamination, process overlaps and bottleneck conditions. It also evaluates furnishings and equipment arrangement (e.g., sample prep and instrument layout) to help optimize work patterns and shared equipment opportunities. The team considers lab, office and support space adjacencies, which are critical for connectivity and supervision as well as interaction space for coordination between testing groups.
- Modular planning for flexibility. An open-lab concept allows the greatest flexibility of space for future change with functional separations only where required. Within this space, utility distribution is planned to allow for open floor plates and flexible connections. The team then establishes a planning grid that allows for adaptability in the technology platform, lab automation, and assay and equipment upgrades. Sample preparation, incubation, amplification/detection and recording stations — which are important to optimize movement between operations — are located within the grid. Additionally, serviceability of equipment and calibration requirements (utilization logs) are confirmed. Finally, structural loading and vibration criteria, essential for sensitive equipment and robotics, are reviewed.
- Development of a safety and containment strategy. The team determines biosafety level or potency of compounds and provides safeguards for personnel (e.g., personal protective equipment) and product (e.g., containment device or room), gowning and de-gowning concepts and isolation requirements. It also conducts safety or hazard and operability reviews and confirms intended standard operating procedures.
- Cross-contamination control. This involves functional separations of special testing needs; space pressure cascade and relationships between adjacent areas; and special procedure/special design requirements, including those for cleanrooms designed to ISO standards, cleanable surfaces, particulate-free finishes, environmental monitoring and, potentially, HEPA filtration. An air-handling zoning and cleanliness strategy will need to be put in place, whether using directional air flows or special spatial monitoring, when required.
- Regulatory impacts. Besides typical building codes and standards, these may include Centers for Disease Control and Prevention and World Health Organization guides; Clinical and Laboratory Standards Institute regulations; ASHRAE standards; and National Fire Protection Association standards for flammables and life safety, among others.
- Special systems and security considerations. This will involve controlled access, equipment monitoring and alarms, data storage and multiple electronic reporting systems (especially those governing uninterruptible power supply, validation, redundancy and protection of personal information) as well as a data backup strategy that is balanced against operational cost impacts.
In all of these areas, space benchmarks can assist the evaluation of proportions of space and needs assessment.
Jim Gazvoda, AIA, is a principal and Jeff Raasch, AIA, LEED AP, is design principal at Flad Architects. They can be reached at jgazvoda@flad.com and jraasch@flad.com.