Managing flammable and toxic refrigerants
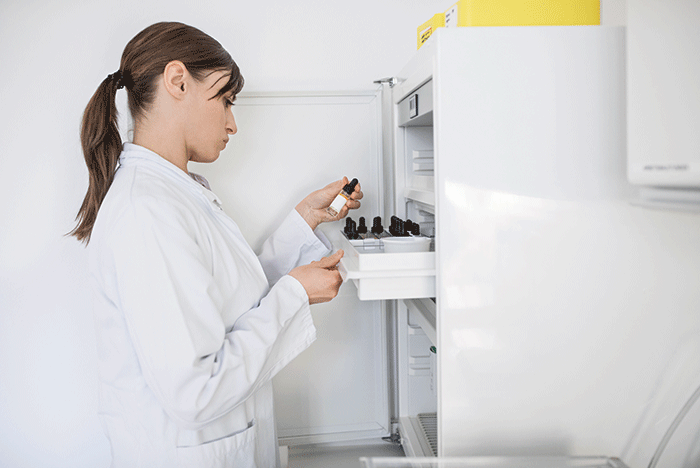
Facilities managers must recognize the often-hidden dangers of toxic or flammable refrigerants used for medication storage.
Image by Getty Images
Facilities managers must maintain an abundant knowledge base to ensure a safe environment for their building occupants, including their most vulnerable occupants: patients. This includes recognizing the often-hidden dangers of toxic or flammable refrigerants.
Exploring the guidelines assembled by ASHRAE is an invaluable resource for facilities managers seeking clarity.
The ASHRAE standards that are pertinent to this refrigerant discussion are ASHRAE 15, Safety Standard for Refrigeration Systems, and ASHRAE 34, Designation and Classification of Refrigerants. These standards are available for free viewing through the ASHRAE website.
Understanding history
Understanding the history of refrigerants will make clear why the refrigeration manufacturers selected flammable refrigerants. In the 1830s, the first generation of refrigerants were picked based upon whatever chemicals worked with the knowledge base of the time to move heat and make ice.
In the 19th century, these refrigerants included diethylether, dimethalether, ammonia, sulfur dioxide and methalchloride. According to a 1989 book by ASHRAE titled CFCs: Time of Transition, “Propane (R290) was touted as a replacement for ammonia refrigerant in the 1920s. Isobutane (R600) was first used as a refrigerant for small systems in the 1920s but, as with other flammable refrigerants (except ammonia), it quickly fell out of use when chlorofluorocarbon (CFC) refrigerants were introduced for commercial use in 1931.”
They worked well moving heat but, during those years, the refrigeration equipment was not well regulated, and failures were quite dangerous for workers who were present when refrigerant was leaked into the plant. These first-generation refrigerants were dangerous to humans and, for obvious reasons, were generally discontinued.
The second generation of refrigerants spanned through the 1990s. These refrigerants were primarily nonflammable and low toxicity. Refrigerants were used in stationary and mobile machinery and included R-11, R-12, R-22, R-502 and similar refrigerants. Besides having high British thermal unit per pound characteristics, these refrigerants had boiling points and pressure ranges that were complementary to the heat transfer temperature ranges needed.
These second-generation refrigerants are classified as CFCs and hydrochlorofluorocarbons (HCFCs). They are significantly safer for humans but harsh on the environment. These refrigerants were determined to be damaging to the ozone layer and contributing to greenhouse warming. In 1987, the Montreal Protocol was initially signed, and today nearly every country has signed and complies with the treaty. The Montreal Protocol has phased out halon and CFCs. HCFC production is scheduled to cease in 2030.
Removing these second-generation refrigerants created a need for replacement refrigerants that were not only safe for the environment but also moved heat efficiently and were not significantly dangerous to humans. A quick reference to identify a refrigerant’s safety can be found in ASHRAE 34.
The figure appearing in the sidebar on page 42 of this article helps users identify the safety and flammability of refrigerants using a simple-to-understand scale. These new requirements drove significant innovation in the industry and ushered in the third generation of refrigerants. Many of these refrigerants are less efficient at moving heat and thus have driven a change in the size of components. Additionally, energy efficiency requirements are contributing to the increasing size of components, hence the larger condensers and evaporators.
Third-generation refrigerants are Montreal Protocol compliant. The Montreal Protocol does not prohibit hydrocarbon refrigerants. Nearly a century after their first debut, hydrocarbon refrigerants such as R290-Propane and R600-Butane have returned to the market, promising to fill the void established by the Montreal Protocol. Both of these refrigerants have attractive boiling points and generous heat transfer capacity, which supports their selection for refrigeration. These refrigerants are found in many health care refrigerators.
What is permitted?
Which refrigerants are allowed in health care facilities? Facilities managers should understand what is permitted and in what quantities.
ASHRAE 15 and 34 specifically identify and define institutional occupancy in the standard. Hospitals and nursing homes clearly fall within this classification.
ASHRAE 15, 7.2, defines the refrigerant concentration limits and references ASHRAE 34, Table 4-1, for the quantities. Exception 7.2 states, “1. Listed equipment containing not more than 6.6 lb. (3 kg) of refrigerant, regardless of its refrigerant safety classification, is exempt from Section 7.2, provided the equipment is installed in accordance with the listing and the manufacturer’s installation instructions.”
ASHRAE 15 Exception 7.2.2 states, “Listed equipment for use in laboratories with more than 100 ft2 of space per person, regardless of refrigerant safety classification, is exempt from Section 7.2, provided that the equipment is installed in accordance with the listing and the manufacturer’s installation instructions.”
These two references appear to permit any refrigerant. However, there are even more stringent guidelines in ASHRAE.
ASHRAE 15, 7.5.3, addresses higher flammability refrigerants and states, “group A3 and B3 refrigerants shall not be used except where approved by the [authority having jurisdiction (AHJ)].”
It goes on to state, “Exceptions to 7.5.3 #3. This restriction does not apply to listed self-contained systems containing no more than 0.331 lb. (150 g) of A3 refrigerant, provided that the equipment is installed in accordance with the listing manufacturer’s installation instructions.”
ASHRAE 15, 7.5.3, is more stringent than Section 7.2.2. In the AHJ world facilities operate within, the most stringent code requirement prevails. Now, 6.6 pounds of refrigerant is no longer applicable, and the smaller quantity of 150 grams maximum takes precedence.
After researching the currently available health care refrigerators and ice machines, the typical under-counter health care grade refrigerator contains 74 grams of R600, and a double-door health care refrigerator typically contains 100 grams of R600.
This exception appears to permit an unlimited number of devices given none of the individual devices contain more than 150 grams of flammable refrigerant. Some facilities managers report the location and quantity of flammable refrigerant containing devices to their AHJ as an added safety measure, although the standard does not require reporting.
The 150-gram maximum charge does carry some limitations. Quick temperature recovery places significant demands on mechanical systems and often requires larger refrigerant charges to manage these heat transfer requirements. Consideration should be given to the selection process, taking into account the capability of the unit to meet the specifications for cooling medications or food.
One may question why manufacturers would choose to use flammable refrigerants when there are other alternative refrigerants available. The answer is complicated at best; however, ASHRAE has determined what levels of flammable refrigerant is required to propagate a fire.
The 150-gram maximum limit is based upon the science of the compounds necessary to support a fire. The lower flammability limit (LFL) is the measure ASHRAE has utilized to quantify this requirement. If the LFL is not reached, there can be no fire as a result of a flammable refrigerant leak since there would not be an adequate amount of flammable gas relative to the amount of air in the room to support combustion.
In simpler terms, if the amount of flammable gas is limited, relative to the air in the room, it will not ignite. This would support ASHRAE 15, Exception 7.5.3.3, concerning the 150-gram limit.
To further support the use of flammable refrigerants, consider the fact that most hospitals are fully sprinkled and those that are not will be by 2026. Additionally, hospitals are surveyed regularly by AHJs to ensure the facilities do not have excessive flammable loads, thereby further reducing the hazard presented.
ASHRAE 15, Chapter 9, Design and Construction of Equipment and Systems, specifically addresses how these refrigeration systems should be manufactured to safeguard against unintended failures. This standard provides manufacturers with the necessary guidelines to design and manufacture refrigeration systems that are both reliable and safe. An internet search for catastrophic failures from flammable refrigerant leaks provided few results. There is an occasional household refrigerator that has experienced a failure that caused damage, but none have been reported as catastrophic.
The most notable fire involving a refrigerator with flammable refrigerant was in London at the Grenfell Tower, which killed 72 occupants. This fire apparently originated with a refrigerator; however, subsequent reporting on Nov. 27, 2018, by BBC News quotes Dr. J Duncan Glover, “The overheating connector in my opinion was the first event that started burning the insulation on the wires that led to the short circuit.”
This professional opinion suggests the fire actually started in the plastic electrical box within the refrigerator’s mechanical section, not related to the flammable refrigerant contained inside the sealed system. The fire spread from the apartment to the exterior building cladding, which provided an unobstructed path for the fire to envelop the building.
The Grenfell Tower did not have a sprinkler system installed. This example contrasts the differences in occupancies — no sprinklers, inappropriate cladding and no central fire alarm system. Hospitals utilize all of the missing components of the Grenfell Tower to alert and protect the occupants.
Taking into account all of the standards and information discussed here, health facilities managers should consider the following when using flammable refrigerants:
Fire and smoke alarm. Hospitals are required to have fire and smoke alarm systems. Is an approved alarm system in place? Is the approved system working as designed?
Location. Is the refrigerator in a nourishment room? If so, what other flammables are in the space? Is the refrigerator open to the corridor? Is it in a patient room? Given flammable refrigerants are heavier than air, is there a concern about refrigerant settling into a low spot?
Maintenance and repairs. Planning how to manage repairs will make a difference with flammable refrigerants. There are reports of minimal training from manufacturers that is causing delays for repairs and driving up costs. Have the facility’s technicians been trained in safe handling of hydrocarbon (flammable) refrigerants? Best practice for all refrigerant repair is to remove the unit to a shop area away from patients and staff, keeping in mind the refrigerant quantity exception in ASHRAE 15 is for listed equipment, not refrigerant in a jug. Is the evacuation equipment safe to use with flammable refrigerants? Is the shop safe for handling and storing flammable refrigerants?
Disposal. At end of life, how will equipment be safely disposed? Will reclamation of refrigerant be required?
In addition to flammable refrigerants, there is another classification for toxic refrigerants in ASHRAE 34. There are only three toxic refrigerants currently available: R21, R40 and R630.
During the research for this article, no health care refrigerators, freezers or ice machines were found that utilize these refrigerants. Knowing the refrigerant type and classification will support the decision to permit or refuse usage of toxic refrigerants within a facility.
The available information for toxic refrigerants in occupied buildings is sparse. Any toxic substance should be carefully scrutinized before it is introduced into a facility. Refrigerants containing the “B” classification (see sidebar on page 42) should not be considered without understanding how the refrigerant will impact those around it if a leak occurs.
ASHRAE is not the only standards body in the refrigerant world. This article did not interpret any differences nor conflicts that the Environmental Protection Agency; National Fire Protection Association; Air Conditioning, Heating, and Refrigeration Institute (AHRI); Underwriters Laboratories (UL); the International Building Code (IBC); or International Organization for Standardization (ISO) have with either ASHRAE 15 and 34.
Knowing the ASHRAE standards and how to apply them to a facility will provide the facility manager with the foundation necessary to understand the dangers often hidden within a mechanical system. Refrigerant phaseouts, and new refrigerant compounds and blends, will continue to drive change in this industry. Keeping abreast of the ASHRAE standards will ensure a defensible and safer environment for building occupants.
Facilities managers may use the following bullet points as reminders to manage flammable refrigerants in their organizations:
- Read and understand standards related to flammable refrigerants.
- Ensure quantity of flammable refrigerant per device is no more than 0.331 pounds or 150 grams.
- Validate the unit is listed for use in health care.
- Carefully scrutinize use of flammable or toxic refrigerants in patient rooms.
- Establish policies for repair locations and mechanic certification requirements.
- Evaluate the need for fire detection and suppression.
A place in health care
Flammable refrigerants have a place in health care. They perform well and pose a minimal risk when used within the standards established.
Health care facilities managers should take the time to evaluate the quantity and type of refrigerant used. They also should recognize that HCFC refrigerant production is scheduled to cease within 10 years and make informed decisions regarding continued purchasing.
Finally, they should use the resources available to educate colleagues and administrators.
Bobby Baird, SASHE, CHFM, CHSP, CHC, is director of facility operations at University of Florida Health. He can be reached at bairdr@shands.ufl.edu.