Establishing a data strategy for RCM
Editor's note: This is the final article of a 14-week series titled "Reliability Asset Management: Getting Started." The series explores the use of reliability-centered maintenance in health care facilities.
I started my career in health care operations just over four years ago, and like some of my fellow task force members, I have little experience with reliability-centered maintenance (RCM).
However, one of the things I’ve learned about this process is the importance of establishing a data strategy as a first step to implementing RCM.
Before jumping too deep into RCM, facilities managers should first answer vital questions regarding equipment inventory. The first question according to the SAE International’s JA 1011, Evaluation Criteria for Reliability-Centered Maintenance Processes is this: What are the functions for the asset?
How does the health care organization define what is an asset and how is it identified in its computerized maintenance management system? An audit of existing/legacy data will help to determine what data the facility has, what data is missing and what effort is needed to obtain reliable data in order to adequately answer that first question.
My journey into RCM implementation has shown the importance of a data management strategy.
The French culinary phrase, "mise en place” translates to “everything in its place” and refers to the setup required before cooking as the chef organizes, measures and arranges the ingredients to simplify and streamline the cooking process.
The data strategy used for an RCM program should follow this same concept. It is important that an organization predefine the nomenclature, data fields and the schema for those data points, before implementing RCM.1 Without good data and data structure, the old adage “garbage in, garbage out” will continue to plague successful implementation.
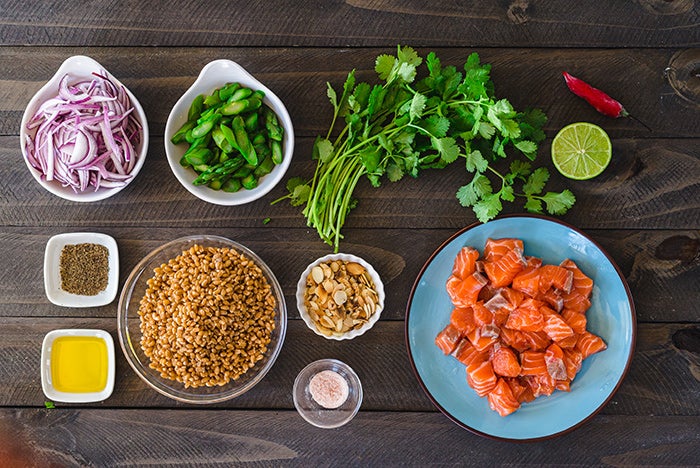
The French concept 'mise en place' is an apt metaphor for beginning a reliability-centered maintenance program.
Image from Getty Images
The goal for health care operators is to use facility data as a tool to make informed decisions. Data with context and analysis leads to information, and information with meaning leads to knowledge. To turn data into a useful tool, adherence to a common nomenclature based on industry standards is key. Developing a common nomenclature is important to simplify the maintenance of reliable master records for buildings, streamline health care facility risk management, increase compliance with regulatory requirements, support benchmarking and increase visibility of total cost of ownership.2
The ASHRAE Vision 2030 listed data and integration as one of the pillars to drive the built environment to increasingly higher performance. Common data storage methods and nomenclature are key to improve interoperability between all the systems and programs that are using the same standard.
The Health Care Facilities Data Standardization working group identified that often inconsistencies exist around naming assets and therefore created a categorization schema that contains 650 classes of facilities assets. This tool is available to all ASHE members to use and serves as an established framework for facility data.
Having assets named and categorized will help to set a steady foundation for building a robust RCM program, and, if built correctly, can lead to greater resiliency, optimization of facility operations and potential cost savings.
FOOTNOTES:
- Keady, Robert. Equipment Inventories for Owners and Facility Managers: Standards, Strategies and Best Practices. Wiley, 2013.
- ASHE ITM - developing code compliant integrated fire protection and life safety inspection, testing and maintenance program