Reliability-centered maintenance guidance
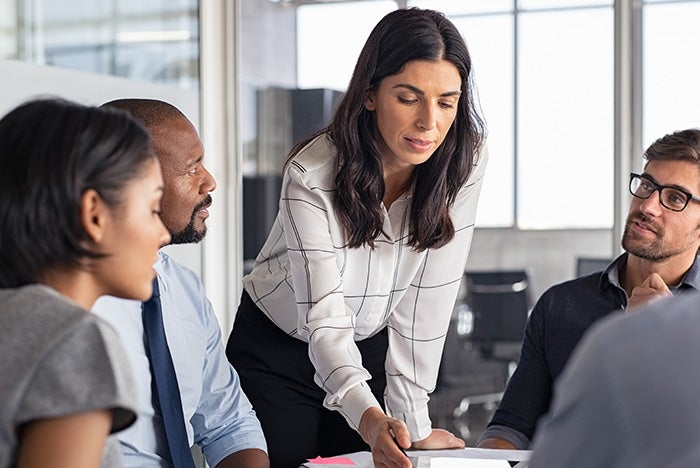
The investments in training, planning and execution of the RCM program will require regular meetings.
Image by Getty Images
Today’s health care engineering teams are tasked with maintaining highly complex, ever-changing systems and environments. Within the context of an evolving regulatory landscape and limited resources, these teams must ensure that structures, systems and assets (SSAs) are operating efficiently, effectively and safely.
Maintaining these SSAs requires adhering to strict service and maintenance guidance from manufacturers or regulatory bodies based on criticality and life support systems and equipment. Regulatory agencies do, however, allow organizations to evaluate all other service, support and maintenance activities and develop alternative activities — known as alternate equipment management (AEM) — that maintain or improve the safety, reliability and operations of these SSAs while using available resources more effectively and efficiently.
RCM guide authors and contributors
Lead authors
- Roy Hirchak, CHFM, is the chief of the facilities operations branch of the Department of Defense’s Defense Health Agency.
- David Lockhart, CHFM, CEM, FASHE, is the support services administrator at Kaiser Permanente.
Authors
- Jim Carrel, CRL-BB, ISO 18436-2 Category III, is the chief operating officer of and a reliability coach with FORUM Reliability.
- Devin J. Hugie, FASHE, CHFM, CHC, CHSP-FSM, CHEP, CLSS-HC, CEPSS-HC, is president and chief executive officer of FORUM Reliability.
- Mark Keller, PE, CHFM, is a section head in the department of facilities and support services at Mayo Clinic in Rochester, Minn.
- W. Thomas Schipper, CCE, FASHE, is the manager of environmental risk at Children’s Hospital of Orange County and Providence Little Company of Mary Medical Centers.
- Michael Wolf, PE, CxA, LEED AP BD+C, is a principal at Farnsworth Group.
Contributors
- Joshua Brackett, PE, SASHE, CHFM.
- Johnathan Johnson.
- Rick Joslin, IRCC RCML1.
- Anthony Moiso, CHFM, CEM.
- Ryan Schramm, SASHE, CHFM, CHC.
- G. Andy Woommavovah, CHFM.
Reviewers
- Marie Getsug, PMP, CAMA, CMRP, CRL, CPIP, CMRT.
- Nicholas Jize, CRL.
- George Mills, FASHE, AAMIF, CEM, CHFM.
- Tim Peglow, PE, SASHE.
- Dean Pufahl, CHFM, CHC.
A major goal of any process-improvement initiative is a shift in resource expenditures without affecting safety, reliability and operations. Reliability-centered maintenance (RCM) is a “process used to determine what must be done to ensure that any physical asset continues to do what its users want it to do in its present operating context,” according to the book Reliability-Centered Maintenance by John Moubray.
It is a methodology designed to guide organizations through evaluating their SSAs to develop more effective ways to service, support and maintain them. While few health care facilities managers have implemented RCM, it has been used in many organizations across many industries, resulting in lowered costs, improved reliability and greater SSA life cycles.
The American Society for Health Care Engineering (ASHE) recently produced a new guidebook titled ASHE Reliability-Centered Maintenance Guide to help managers better understand the concept of RCM and how they can apply it in their organizations.
The guidebook, from which this article was excerpted and adapted, gives health care facilities managers an overview of the RCM process along with the knowledge and tools needed to help their leadership navigate through the process as well.
Decision-making process
RCM is a decision-making process that analyzes an SSA, defines its true design function or what it is supposed to do for the organization, and determines the risk and/or criticality of the SSA to the organization and operation of the facility. A determination is then made about the level of analysis and the RCM application that will be needed.
The next step is to identify how the SSA can fail to perform its function and the effects of the failure so that the optimal maintenance strategy to prevent and/or minimize losses from those failures can be applied. The strategy can cover an entire SSA or components of an SSA, and it can be used on all types of SSAs or a subset of targeted SSAs.
The key is to understand the functions, risks and proper application of a planned maintenance program to increase the reliability of the SSA identified during the RCM process review.
Implementing an RCM program in health care depends on the risk and complexity of the SSA and allows for the identification of different maintenance strategies to prevent SSA failures. A high-risk, complicated SSA will require a full seven-step review, while a high-risk, simple system may require only an abbreviated or simplified RCM to understand the failures and their effects, and the application of proper maintenance to maintain high reliability.
The basic principles of RCM are outlined in the SAE International’s JA1011 standard for RCM and organized around a series of questions that encourage digging deeper into the system or equipment and its operational outcomes:
- What are the functions for the asset? [functions]
- In what ways can it fail? [functional failures]
- What causes each functional failure? [failure modes]
- What happens when each failure happens? [failure effects]
- In what way does each failure matter? [failure consequences]
- What should be done? [proactive tasks and interval]
- What should be done if a suitable proactive task cannot be found? [failure management strategy]
The result is a strategy for managing the risks and failures of a particular SSA while also developing and documenting analytical values for future evaluations. Ultimately, the organization will identify which of the following is the best combination of maintenance strategies for that SSA, because components of more than one strategy are usually employed:
- Preventive maintenance (interval based).
- Predictive maintenance (condition based, sometimes called on-demand maintenance).
- Failure-finding maintenance (time based and/or condition based).
- Planned run-to-failure.
- Reactive maintenance.
The combination of the analysis and assigned maintenance strategies can produce an increase in SSA reliability and lead to a reduction in resources required to maintain the SSA, if the strategies are followed.
Types of programs
The two primary types of RCM programs are original RCM, also known as classical RCM or rigorous RCM; and streamlined RCM. Many variations of RCM have been implemented, with each application of the RCM methodology fitting a particular need.
The JA1011 document was developed in response to these variations, and it ensures that an organization has clear guidance on what constitutes a valuable RCM program. The variations of RCM — including intuitive, streamlined, abbreviated, concise, preventive maintenance optimization, reliability-based and reliability-enhanced — are all still based on the RCM fundamentals, allowing an organization to focus on specific areas for insight and improvement.
Streamlined RCM variations have become popular and are applicable to many SSAs to reduce the risks to operations and resources. Often, RCM variations are grouped based on their approaches to the RCM process and, therefore, provide varying degrees of benefit to an organization. These approach-based groupings include mixed, simplification of analytics, optimization, broad and mathematical/statistical, according to an article titled “An Evaluation of Alternative Approaches to Reliability Centered Maintenance” in a 2015 issue of the International Journal of Applied Engineering Research. Following is a brief description of each:
- Mixed approaches combine several variations of RCM to focus on the consequences of failure analysis as the guiding point. One type of mixed approach, risk-centered analysis, uses probability and consequences to define each failure mode risk and then analyzes the ranked failure modes. Another approach is risk-based RCM, which uses strong statistical analysis to overcome ad hoc failure mode effects and criticality analysis to identify the inspection plans and procedures. In the end, mixed-type approaches use a combination of analytical processes to determine the best maintenance strategy for the SSA.
- Simplification of analytics approaches simply removes one or more of the core steps of classical RCM. Preventive maintenance optimization (PMO or PREMO) uses task/procedure analysis rather than system analysis. In this method, the tasks drive the failure modes (e.g., if the task is “check bearing for noise and vibration,” this will lead to possible failures from both issues). Criticality analysis considers a variety of different analytics but for limited components.
- Optimization approaches seek to “optimize” maintenance implementations. Using mathematical models to combine reliability with economics, these approaches compare the cost-effectiveness of maintenance policies resulting in efficient inspection and maintenance frequencies. While these approaches provide a measurable outcome for cost-benefit analysis, they usually do not consider failure modes or trends and the ultimate benefits are often not visible within maintenance departments.
- Broad approaches combine multiple ways to minimize the total cost of maintenance while maximizing the SSA reliability. These goals are accomplished by optimizing several factors at once to determine the lowest expenditure of resources that achieve the desired reliability level.
- Mathematical/statistical approaches use the numerical values derived from failure mode, consequence, financial, resource and reliability analytics to identify probable failure rates, costs associated with those failures and preventive measures of those failures.
The RCM process
The RCM process presented in the ASHE guidebook provides advice on preparing, performing, implementing and monitoring the RCM methodology to ensure success. RCM applies to all levels of systems or equipment groupings and to all types of and approaches to maintenance, whether equipment is recently acquired, in use, ready for use, or in standby or layup condition.
RCM provides the methodology to develop prescriptive, on-condition, predictive, preventive, corrective, failure finding and no-scheduled maintenance tasks and strategies within a planned maintenance management system. Specific maintenance procedures — including the development of task steps, safety requirements, tools and parts — may be developed during or after the application of the RCM methodology for inclusion in preventive maintenance and corrective maintenance plans.
Planning and preparing. Prior to implementing an RCM program, organizational planning and cultural changes need to be in place, an RCM analysis must be conducted, and a data audit and analysis of the computerized maintenance management system (CMMS) must be completed.
- Within the organization, upper management support is needed as well as plans for establishing the RCM team, staff engagement, key staffing needs, time and financial investments, and alignment with requirements.
- The RCM analysis includes collection of maintenance and design data, operator and maintainer input, work order history and current preventive maintenance tasks as well as information about the impacts of failure.
- A review of CMMS records will help identify available and missing data as well as the work needed to obtain additional data.
- The data audit process involves developing a data strategy, determining current CMMS data collection procedures, mining data in the CMMS, and standardizing and normalizing the data through an asset policy.
- CMMS work types — including preventive/planned maintenance, corrective maintenance and service requests — can help with data normalization.
Implementing the program. Implementation of an RCM program involves a series of training activities; data, system and program analyses; and maintenance plan development.
- The kickoff and training signal the start of the RCM implementation process, which requires that various leadership and organizational components be in place.
- A Pareto chart uses CMMS data to identify “bad actors” and which SSAs will need what level of RCM.
- The system analysis process involves multiple steps to identify and select systems, define systems and their boundaries, describe system functions and functional failure, conduct a failure modes and effect analysis and logic tree analysis, and select tasks.
- In the post-RCM analysis, additional tasks further support the RCM program, including development of manuals and specifications and documenting the effects of changes.
- An equipment maintenance plan developed as part of the RCM program provides a detailed overview of the maintenance work that includes new technologies for improving the program.
Using condition-based monitoring. Condition-based monitoring (CBM) provides early fault detection that allows for advanced maintenance planning and the establishment of baselines for comparison and analysis.
- CBM is a noninvasive way to monitor changes in the condition of machines to assist in determining the best time to perform necessary maintenance tasks or invasive repairs.
- CBM technologies are an extra tool to help mechanics and technicians understand what is happening with equipment by detecting characteristics beyond those detectable by human senses.
- The maximum benefit of CBM comes from using the technologies in conjunction and on a scheduled basis to develop longitudinal data along the equipment’s life cycle.
- Establishing a baseline provides a reference point for the equipment’s life and allows the maintenance team to plan repairs or replacement at times that minimize operational impacts.
- Infrared thermography, ultrasound testing, vibration analysis, tribology/fluid analysis and motor analysis are CBM technologies with applications to health care.
Identifying service needs. Planning, implementing and maintaining an RCM program will require qualified facilitators and CBM technicians.
- The RCM facilitator trains the RCM team to work with equipment or systems and prepares staff members to oversee the RCM program.
- An effective RCM facilitator will have RCM analysis experience and will possess a range of technical, management and regulatory skills.
- For the CBM program, expertise in asset condition monitoring is demonstrated through specific certifications for activities such as vibration analysis, infrared thermography and ultrasonic testing.
- RCM facilitation and CBM services can be in-house or outsourced, and how the program is structured will depend on costs, resources, the scope of the program and longer-term goals.
- Quality control involves establishing a baseline, tracking staff hours and system outcomes, and reporting regularly to the organization’s leadership.
Following the decision tree. The RCM decision tree is a series of questions for an equipment item or system that will help determine the best program by addressing failure modes.
- The “evident functions” analysis looks at the occurrence of a failure, the loss of function or secondary damage, and the direct adverse effect on operational capability.
- The “safety consequences” analysis considers the on-condition task to detect potential failures, the rework task and the discard task.
- The “operational consequences” and “nonoperation consequences” analyses address economics, including maintenance repair costs.
- The “hidden failures consequences” analysis looks at items that require scheduled maintenance to ensure a level of availability necessary to avoid exposure to multiple failures.
- Classical RCM applied to health care settings provides a list of failure modes that are then prioritized using the logic tree analysis to determine equipment criticality.
Measuring progress and success. Case studies of RCM programs at two health care facilities discussed in the ASHE guidebook detail the various cultural, financial, executive and clinical aspects of planning, implementing and maintaining an RCM program.
- For health care facilities, RCM programs reduce costs and labor hours by adding and modifying existing RCM tasks, changing preventive maintenance tasks to RCM tasks and removing preventive maintenance tasks.
- The Mayo Clinic Franklin Heating Station (MCFHS) and Kaiser Permanente Roseville Medical Center (KP Roseville) offer case studies that include different approaches, funding models, tools and lessons learned.
- Both organizations achieved multiple levels of buy-in, facilitated kickoff events, invested in expanding the skill sets of team members and established metrics to track progress.
- The MCFHS RCM program was driven by the results of a culture of safety employee survey and the high cost of reactive maintenance.
- KP Roseville initiated its RCM program to better understand critical and high-risk systems, enhance data quality, address outdated preventive maintenance procedures and improve the condition-based monitoring program.
Addressing code requirements. Risk assessment and accreditation impacts are an important consideration in developing and implementing an RCM program in a health care facility.
- Patient risk categories can be applied to the logic tree format to determine risk-based scores that, together with equipment criticality categories, generate indicators related to the impact of functional failures.
- For hospital accreditation, a full year of maintenance with old and new methods is required before the RCM methodology can become the standard.
- An AEM program allows an organization to deviate from the manufacturers’ requirements for equipment maintenance.
- Implementing an AEM program through a six-step process allows an organization to optimize the use of available resources to better manage the overall safety of the physical environment.
- An organization should be prepared to defend the AEM program and address questions about its effectiveness.
Next steps
The ASHE Reliability-Centered Maintenance Guide offers a pathway to better maintenance, fewer operational failures and better cost control for health care facilities.
RCM is not a one-and-done process but a continuous improvement process that aligns with accreditation bodies. Although RCM may appear daunting at first, once the maintenance team grasps the process and sees the results, the benefits of the RCM process will be clear.
Some key takeaways to remember through the RCM process include:
- Begin to identify the problem areas in the facility that need improvement.
- Data mine the CMMS to gather the data to narrow down the equipment and components causing the most problems.
- Develop a two- to three-year plan to implement RCM, and do not be afraid to obtain some certification in RCM or bring in experts for guidance along the way.
- Once the first RCM implementation is completed on a specific system or component, share the information with the maintenance staff and leadership.
- Remain focused and do not try to apply RCM to everything in the facility.
As an RCM program matures, the frantic emergency calls will subside and the maintenance staff will enjoy the new pace of work. RCM also gives the team time to focus on other matters the health care organization is facing. With discipline, full RCM implementation is very possible.
Health care facilities managers should remember to celebrate the accomplishments, and then help fellow facilities managers find their way to RCM harmony.
Reliability-centered maintenance benefits for health care facilities
As health care facilities teams maintain structures, systems and assets (SSAs), identifying ways to improve the reliability of SSAs while also improving efficiency and effectiveness is important. At first glance, reliability-centered maintenance (RCM) provides a solution to addressing those needs by effective use of resources to identify potential failures, causes of failures and strategies to reduce failures.
The implementation of RCM is somewhat different in its approach to maintenance. Many technicians and facilities managers may perform a task without fully understanding the task and what it accomplishes for the equipment or system. RCM’s focus is on maintenance and the reasons the maintenance task is performed in the first place.
It changes the process from following manufacturers’ guidelines to understanding the failure modes that the equipment is subject to experience and the maintenance tasks aligned with these failure modes.
The goal of this process is to identify developing defects and precision solutions to mitigate them. As the RCM program is developed, the maintainer’s understanding of the individual task and its impact on the equipment will change and give the maintenance team a better understanding of what they are doing.
The RCM analysis and adoption of maintenance practices provide many benefits to the organization, including increasing the reliability of equipment and systems, lowering maintenance costs by eliminating unnecessary labor hours on nonbeneficial preventive maintenance tasks, and scheduling repairs prior to equipment failure. RCM also allows technicians to develop records of failures, identify corrective actions and use strategies that prevent or reduce failures in the future.
An RCM analysis supports decisions to implement alternate equipment management strategies for SSAs by creating logical tasks and procedures tied to realistic schedules and events that ensure all organizational resources are optimized for efficiency.
An RCM analysis also supports a continuous loop to improve on the RCM program and process and to examine the measurable and demonstrated results of the analysis. By comparing RCM outcomes to the pre-analysis maintenance program, tangible outcomes and benefits can be identified and presented to the organization. In addition to the cost variables, an RCM analysis provides the following benefits:
- Insight on failure modes and a better understanding of the SSAs through RCM introductory training on SSAs and the RCM analysis.
- Ownership of the maintenance program by those involved with the RCM analysis.
- Reduction of intrusive maintenance activities and downtime required to perform frequency-based maintenance by applying prescriptive, on-condition and predictive maintenance mitigation strategies.
- Precision-driven maintenance demanded by applying predictive technologies.
This article was excerpted and adapted by Health Facilities Management staff from the ASHE Reliability-Centered Maintenance Guide.