Strategies to maximize HVAC system output
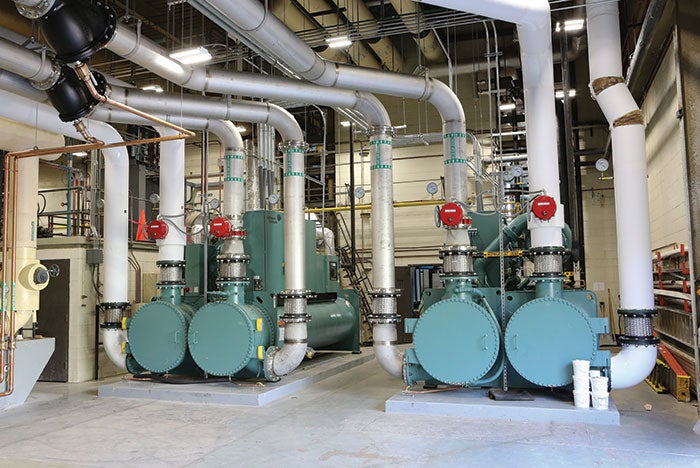
Centralized chiller plants and large air handlers cost more to operate, generally have more sophisticated controls and are more likely to have dedicated staff to operate and maintain them, thus presenting an opportunity for greater savings.
A health care facility’s HVAC system — the chilled water plant, steam and hot water plant, and air distribution system — typically accounts for 33 percent of its electricity and 57 percent of its natural gas use. Chilled water plants also consume substantial water.
That makes these systems ripe for optimization, which means getting away from the philosophy of applying more energy to hide the symptoms of system deficiencies and, instead, finding a way to deliver the most system output with the least system input.
HVAC optimization involves automatically controlling HVAC systems to deliver needed heating and cooling at energy-efficient levels. This goes beyond recommissioning or traditional static setpoints and proportional-integral-derivative-based controls. Optimization solutions should measure the system input (i.e., electric, gas, water) and the system output (i.e., heating, cooling, airflow, water flow), and use that data to operate the system in real time.
Typical optimization projects provide payback in three to five years, with savings starting immediately. In addition to automatic control, HVAC optimization provides energy monitoring and fault detection, which can enable facilities personnel to improve operations without increasing head count.
Compelling cases
Health care facilities can be subject to many conditions that would make a compelling case for HVAC optimization. Some of the leading motivations include:
Energy costs. Rising energy costs — due to rising electricity rates or increased usage — are a sign that a facility would benefit from optimization.
The more a facility pays for power, the more it will benefit. (As a general guideline, 5 cents per kilowatt-hour (kwh) is inexpensive, 10 cents is average, 15 cents is high.)
Optimization can help a facility to take advantage of variable rates by shifting power use where feasible to the lowest rate periods. Additionally, it can ensure that equipment is running at full capacity, which can help a facility to use less energy.
Sustainability mandates. Many organizations have a mandate to save energy and meet sustainability or carbon-footprint goals.
Efficiency efforts will yield easy payoffs — energy savings with paybacks of one to three years — or more difficult ones with paybacks of three to 10 years. It’s common to see facilities start energy-saving measures by retrofitting lighting, but what do they do once all the lights are retrofitted?
HVAC optimization is a logical next step and is essential to meeting aggressive sustainability goals, but it falls into the more difficult category, with higher complexity and higher cost.
A mix of old and new equipment. HVAC systems that have been built up over time may have a mix of equipment — some old, some new and of different brands. With mismatched equipment, it is not always clear which is the best combination to run or what is the best setpoint for a subsystem. HVAC optimization provides the information needed to control complex HVAC systems for the highest possible efficiency and control sequences that will use that information to the fullest.
Optimization requirements
Projects to minimize HVAC energy and water use often follow some basic principles that serve as guideposts as more complicated issues are tackled. To deliver consistent and reliable savings, HVAC optimization requires:
Measurement. Measuring both the energy input and the system output is essential for data-based optimization. Varying the energy input of any piece of equipment will vary the total system output. So, without an accurate measure of energy use by each piece of equipment in the system, it is impossible to predict and report the impact of varying conditions on the system. In short, if you can’t measure it, you can’t optimize it.
System-level approach. A system-level approach is key to effective HVAC optimization because it prevents unintended side effects that can occur if you optimize components one by one. Reducing the output of one component without analyzing its effect on the entire system may cause other components to increase their energy use, leading to lackluster results.
Automatic control. A truly optimized system requires a continuous, automatic controller. A fault-detection diagnostics platform or an alarming/advisory system that requires human intervention to implement optimization recommendations may provide some energy savings, but real-time, dynamic control is the only way to provide maximum savings without compromising operations. This often is the most challenging part of an optimization project, requiring integration, programming and testing, typically in collaboration with a controls contractor.
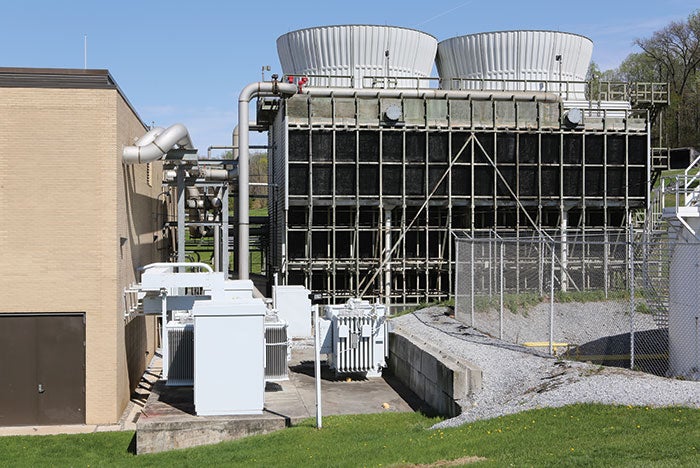
Most existing facilities have dialed-in operational setpoints and procedures meant to fulfill worst-case conditioning and ventilation requirements.
Making it work
In general, the larger, more highly utilized and more centralized the facility, the better suited it is for HVAC optimization. Centralized chiller plants and large air handlers present a concentrated target, which usually produces greater savings. These systems cost more to operate, generally have more sophisticated controls and are more likely to have dedicated staff to operate and maintain them. Owners of multiple facilities that are looking to optimize should prioritize buildings based on size, electricity rate and total utility cost.
In particular, facilities with the following characteristics would be prime for optimization:
- High energy use — the more energy consumed, the greater the benefit.
- 24/7 operations — hospitals are great candidates. As part of the optimization process, it is critical to identify the facility’s specific HVAC requirements and ensure that the optimized system could operate within those requirements.
- New HVAC systems that have not been optimized.
- Middle-aged HVAC systems (10 to 15 years old) are often good candidates. They offer room for improvement and are worth upgrading.
Any optimization project, as part of the initial feasibility study, should quantify operational restrictions that would constrain optimization and ensure that the optimization product can operate within those restrictions. One common issue in health care facilities is that operating rooms have temperature requirements that the cooling system must fulfill; this typically manifests as a static chilled water temperature setpoint.
Health care spaces also have air change per hour (ACH) requirements for air-quality control, odor control or comfort. Facilities may have equipment that uses chilled water for cooling and that can sometimes drive the operation of the system.
In some cases, health care facilities are using far more energy than necessary to meet such requirements, and optimization will address that waste. Most existing facilities have dialed-in operational setpoints and procedures meant to fulfill worst-case conditioning and ventilation requirements. Often, systems operate at these setpoints at all times, even when not needed.
ACH requirements, for example, do not need to be fulfilled 24 hours per day in facilities that are not occupied 24 hours per day. A particular piece of equipment that requires cooling may cause a whole chiller plant to run, even when it is the only load in the facility that requires cooling at a given time.
Facilities professionals should identify system requirements and develop a plan for addressing all needs with the lowest possible energy input. The solution could be as simple as adding an occupancy schedule and night setback setpoints to an air handler, or installing a dedicated air-conditioning unit to provide cooling to a specific piece of equipment, allowing the chiller plant to shut down when it’s not needed.
In the case of a chiller plant with strict chilled water-temperature requirements, it may not be possible to optimize the chilled water temperature; however, optimizing the cooling towers, condenser pumps, chiller staging and chilled water-pump operation still could produce significant energy and cost reductions.
Determining ROI
In an environment where energy project dollars must meet a payback threshold, certain facilities are more likely to meet return on investment (ROI) requirements than others. If an HVAC optimization package reduces building energy use by 5 percent and the payback threshold for energy projects is three years, then the project budget for optimization is 15 percent of the building’s annual energy expenditure. Between a clinic that spends $50,000 a year in electricity or a hospital that spends $5 million a year, the hospital is clearly the highest priority. Facilities professionals should specifically look at:
Cost factors. The condition and age of the HVAC system will affect both the cost and the savings potential of an optimization project. The older and less controlled the HVAC system, the larger the potential savings, but also the larger the potential cost to bring the system to optimization readiness. The newer and more modern the HVAC system, the lower the cost and the potential savings.
The size of the facility and its HVAC system also affect costs. Larger and more centralized systems concentrate energy use in one place, where it’s easier to measure and optimize. A distributed system, such as one with numerous split systems or rooftop DX units, will require optimization and monitoring of each independent system and will cost more to optimize.
An HVAC system at the end of life provides another opportunity for optimization. If a system is ready for retirement, optimization along with equipment replacement provides a quantifiable financial payback that otherwise would not exist for the capital project. Replacing and optimizing a new chiller may have a 10-to-15-year payback, but replacing the chiller with no optimization may have a longer payback or none at all. This difference in payback could provide the impetus needed to secure funds to replace old equipment.
Timing for cost effectiveness. Depending on the size of the system, HVAC optimization can be a significant expenditure, requiring up-the-ladder budget approvals. It’s a good idea to time optimization feasibility studies to be completed in line with the budget planning cycle, to avoid yearlong delays in procuring optimization.
If a large capital improvement is already planned, it may make sense to include HVAC optimization, especially if the HVAC system is part of the renovation. This may allow facilities professionals to consolidate construction costs. A design review from a qualified optimization provider may reduce project costs if they find unnecessary or redundant equipment.
In another example, the HVAC optimization system may be able to achieve greater efficiency with a primary-only, chilled-water pumping arrangement, and converting the system to primary-only during the design phase eliminates the need to purchase and install a whole set of pumps. In still another example, a facility can install new flow meters and other sensors without hot taps during construction, which is much cheaper than retrofitting them onto a running system.
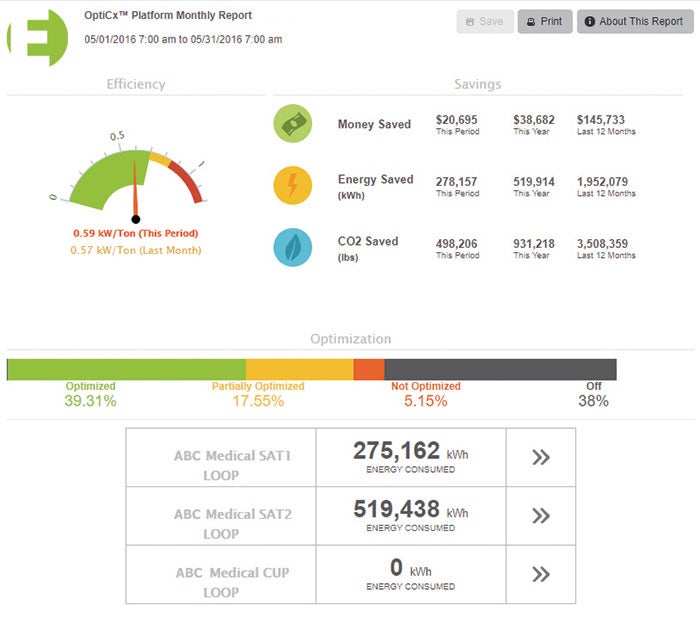
An HVAC optimization package should produce measurement and verification reports capable of documenting the effectiveness of efficiency efforts.
Project elements
A significant number of energy conservation projects do not provide the projected energy or cost savings. To reduce that risk, such projects should follow a robust process from concept to design, bidding, construction and after-project support. It’s also important to educate stakeholders and gain their buy-in on the process and goals. The following steps are key to a successful project:
Goal setting. Is the goal to reduce energy costs as an absolute value, or energy cost per square foot or energy input per unit output? When reducing energy costs by a particular amount, what is the baseline against which energy use will be compared? Answering these questions will ensure that the project has the right targets.
Measurement and verification (M&V). M&V is a critical and often neglected part of optimization. The optimization product should include an M&V method and should be capable of reporting the effectiveness of optimization versus the organization’s goals. If the organization has a carbon footprint-reduction goal, for example, the product should report mass of carbon dioxide reduced in an easy-to-retrieve format.
Road map. The project scoping phase should include development of a robust road map that provides a calculation of the projected energy savings, clear documentation of the method to achieve those savings, and a detailed plan of the project retrofits and tasks required to implement optimization. The energy-savings projections and detailed retrofit plan should be developed in partnership with the contractors who will do the work. Many project managers instead go the traditional route of plan and specification, then request multiple bids. But optimization is not yet a commoditized product that can be successfully purchased this way; typically, the bid winner is the one who provides the least optimization at the lowest price, which results in missed savings.
Quality control. A key part of a successful optimization project is an engaged project sponsor or owner’s representative. In retrofit jobs, optimization may involve multiple vendors and groups on the facility side; someone must coordinate the many activities and ensure that the project is built with success in mind. Each part of the optimization project must be installed correctly for the system to work. Instruments that are used as control points for optimization or for calculating the energy input or output of the system must be installed in the correct location with correct orientation and be properly calibrated.
Training. Near the end of the project, a clear handoff and training for facility personnel is essential to ensure that the optimization system is used to its fullest. As with HVAC controls, HVAC optimization easily can be overridden or bypassed by operators and thus fail to meet savings goals. Proper training will give operators an understanding of how the system is meant to work, what to expect the system to do and what to do in the event of a problem.
Once the project is completed, facility personnel must monitor and report on the optimization. Periodic reviews of optimization will prevent performance drift and ensure that the project achieves the projected savings.
Excellent performance
For health care facilities, HVAC optimization can deliver significant energy savings and contribute to achieving sustainability mandates. With these elements in place, an optimization project will result in excellent system performance and energy savings year after year.
Fred Woo, P.E., is manager of engineering at Optimum Energy LLC, Seattle. He can be reached at fred.woo@optimumenergyco.com.