Readiness for accreditation surveys
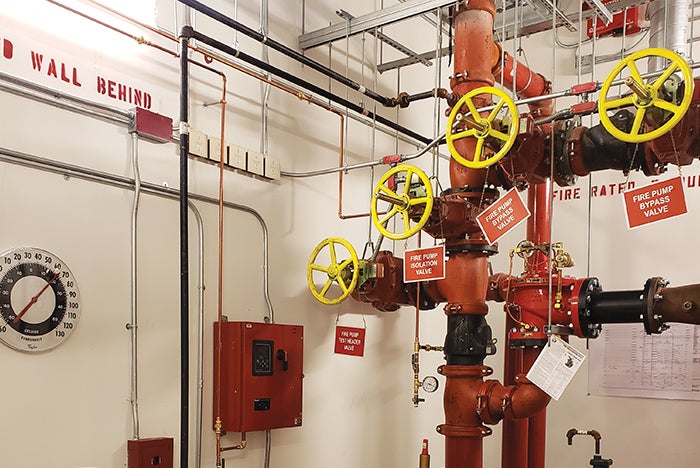
Fire pumps and the rooms where the fire pumps are housed must be inspected on a weekly basis.
Hospitals accredited by The Joint Commission (TJC) can expect an unannounced survey from TJC between 18 and 36 months after their previous accreditation survey.
However, whether or not a health care facility is accredited by TJC, this guide will provide code requirements and recommended best practices that will increase staff awareness for what to look for when conducting life safety (LS) inspections of a health care facility.
Locations the LS surveyor will want to see during the survey include the main fire alarm control panel; fire pump room; generator room; roof; operating room (OR) suite; central sterile supply; endoscopy and cath labs; isolation rooms; main piped medical gas panels; bulk oxygen and medical gas tank farm or main medical gas storage area; pharmacy; kitchen; gift shop; loading dock; hazardous areas; electrical closets; and fire and smoke barriers.
But what does that mean for the facility team, and how can the team be survey ready?
Survey ready
Immediately, the surveyor may go to the facility’s main fire alarm control panel to verify the system is functional. The facility manager will need to be able to explain to the surveyor if the fire alarm panel has any trouble conditions or disabled points and, if so, whether an interim life safety measure (ILSM) assessment is covering each item.
The facility should have a fire alarm logbook into which staff enter daily any conditions identified and have a process for making the appropriate notifications to hospital staff to conduct an ILSM assessment. Having a non-functioning fire alarm system without staff knowledge and proper ILSM assessment would be an immediate threat to life and would stop the survey.
In addition, staff must know the location of the electrical panel with the designated breaker (fused disconnect switch) for the fire alarm system. The location should be labeled at the main fire alarm panel.
Before or after surveying the main fire alarm control panel, the survey team will attend the opening conference welcoming TJC surveyors. The LS surveyor usually will not want to waste any time; they have a lot to look at in their short time in a facility. So, the LS surveyor will dismiss themselves from the opening conference after introductions, and the facility manager will meet them outside the conference room to begin the survey.
The facility orientation is when the LS surveyor will meet with the appropriate facilities staff to become oriented to the layout of the facility. This includes reviewing the facility’s life safety building feature drawings and to hear from staff if there are any areas under construction or if there are any equivalencies granted by TJC.
If a facility manager utilizes an electronic system for showing the life safety building feature drawings, it is recommended they have hard copies as a backup. Immediately following the facility orientation, the surveyor will begin the document review.
Managing documents
Document review will be conducted following TJC’s LS and environment of care (EC) documentation checklist, which should be utilized to prepare for the survey. Facility managers should make sure they are familiar with documents in the binders that the surveyor is going to ask for. The quicker the facility manager can get the document the surveyor is requesting, the better.
It may be difficult, but the facility manager should try to hand over only the exact document the surveyor is asking for. If the facility manager gives them the entire binder, they are now free to look through it all, and it may open the facility staff up to more questions. The facility manager should do several dry runs on the documentation prior to the surveyor being on-site.
A good tip is to tab the documentation binders by TJC standard. Facility managers should make sure they have everything clean and easy to read. If a facility manager has had any troubles, yellow tags or failed devices, they should make sure they have the repair ticket, work order and other documentation behind it showing they have taken action and the device is in proper working order.
Facility managers should make sure to take notes and write down anything the surveyor questions or requests. If facility managers are unable to present something to the surveyor in a timely manner, they should make sure they present it to the surveyor before they leave the facility. Even though the surveyor may still write it down as a finding, at least the facility manager has already “corrected” that finding.
The building tour
After that, the facility manager can expect the LS surveyor to start the building tour. TJC has provided a building tour guidance document available to all facilities that will aid in the preparation for a survey. Each facility should have a planned survey route that is developed during survey planning and audited during internal mock audits. While a surveyor could deviate from the planned route, it is always a recommended practice to have a planned route. The facility manager should designate a planned route and survey to that route, making sure any advanced teams know the route.
It is also recommended that each facility designate an advance team to be ahead of the surveyor doing a walkthrough of the corridors to make sure no extinguishers, medical gas shutoff valves, egress paths, electrical panels or other items are blocked by patient beds, workstations on wheels, chairs or other common items.
Facility managers should have their advance team check pressure relationships in areas such as ORs, central sterile processing departments and soiled/clean utility rooms to make sure the facility is maintaining appropriate pressure differentials. They also should check fire doors to ensure they are self-closing, latching and gaps are within the permitted limits. The team also should check for various unsecured gas cylinders as well as check the “full” and “empty” racks for the E-cylinders.
As soon as a facility is notified that TJC has arrived, the advance teams should be dispatched to their designated locations and begin tracing.
The LS surveyor likely will first want to survey and check the air pressure relationships in the ORs and critical care rooms. This is conducted early in the survey to allow an organization time to correct any deficiencies while the survey team is on-site. During document review, the surveyor also may request to see any balancing reports for the ORs to check the air exchange rates. Facility managers should be sure to make any introductions to the OR leadership when in the OR area and have them walk with the facility team while the surveyor is in their ORs.
Facility managers will need to direct the surveyor in the proper attire, following their organization’s process on gowning to walk into sterile cores and hallways around the OR.
While checking pressure relationships, facility managers can expect a surveyor to ask the clinical team the process if a room under positive pressure suddenly is under negative pressure. The clinical team must know if the room pressure is under constant monitoring by a central system by facilities and if a notification will be made to the facilities team or others in the organization.
Facility managers should discuss the process with the clinical team on a regular basis and make sure everyone is able to speak about the process, including which rooms should be positive or negative and what to do in situations in which two rooms back to back are positive and which takes precedence.
If there are any deficiencies and the facility makes the corrections, a review of corrective action must include documentation that other areas supplied by the same air handler were not negatively impacted by correction work. This means a facility did not take air from another part of the building to correct an issue in the OR suite.
OR staff also will be asked about fire safety in the OR. Staff members have specific roles during a fire or smoke event. The roles of staff and licensed independent practitioners at and away from a fire’s point of origin — including when and how to sound and report fire alarms, how to contain smoke and fire, how to use a fire extinguisher, how to assist and relocate patients, and how to evacuate to areas of refuge — may be questioned by a surveyor.
The LS surveyor will want to open several ceiling tiles to check above the ceiling. Above the ceiling, the surveyor will be looking for items on the sprinkler pipes (including laying on, touching or wrapped around), penetrations not sealed or improperly sealed, and open junction boxes.
Facility managers should make sure they have material on-site to make repairs for any deficiencies cited during the survey. If the surveyor identifies a finding, the manager should take a “before” picture, get it repaired and then take another picture of the repair completed. They should also write down the location and give each finding an identification, keeping track of everything.
As with the documentation, it is best for facility managers not to volunteer information. They should be careful not to mention anything that could contribute to a “leadership” finding. For instance, they should never say, “We could fix that, but it is not in the budget.”
Findings that are not corrected immediately will require a risk assessment and, potentially, ILSMs.
Specific areas
A closer look at some of the specific areas the surveyor will be observing include the following:
Roof. The LS surveyor will be looking for proper identification of hazardous exhaust, including proper biohazard warning labels. Labeling of all equipment is recommended to avoid any questions about what equipment is located on the roof. Fresh air intakes must be located at least 10 feet from exhaust vents. Facility managers should check that there are no clogged bird screens on air intakes and no water is ponding under the intakes. Facility managers also should make sure there is no evidence of smoking.
Fire pump room. The National Fire Protection Association’s NFPA 25-2011, Standard for the Inspection, Testing, and Maintenance of Water-based Fire Protection Systems, requires fire pumps and the rooms where the fire pumps are housed to be inspected on a weekly basis. Items to be inspected each week include adequate heat in the room, proper ventilation, pump valves are open, no leaks, gauge readings are within range and pilot lights on the electrical controller are on, among others.
These are weekly inspection requirements, even though the pump itself is required to be tested on a monthly basis. The LS surveyor will be looking at the overall condition and readiness of the fire pump equipment, including pump status, whether valves are supervised and secure, and any visible leaks. The surveyor also will be checking for proper firestopping of penetrations and top-of-wall gaps, fireproofing of structural beams and for emergency lighting.
Generator room. In the generator room, one of the first things the LS surveyor will look for is the remote manual stop station (i.e., generator shut off). The remote stop should be located outside the generator room. This allows the facility manager to shut off the generators without having to further endanger anyone if there is an event occurring in the generator room, such as a fire or diesel leak.
The LS surveyor then will look at the exit sign within the generator room. These exit signs should be on a separate battery backup because they are meant to provide help if the generators fail and somebody needs to exit the room. Along with those two items, the LS surveyor will be looking at basic maintenance of the generators and the room itself.
Kitchen. Kitchens should be assessed to determine if they are considered a hazardous or non-hazardous area. If determined to be a hazardous area, the facility LS drawings should be updated and the kitchen should be inspected to the requirements for hazardous areas.
The LS surveyor will be checking that proper Class K extinguishers are installed at the proper distance from the source with the appropriate placard.
Staff knowledge will be tested by asking a staff member what they would do if there was a fire at the cooking station. Staff must be able to speak to the activation of the Ansul Inc. system and, if the system does not activate, where to find and how to properly use a Class K fire extinguisher. The range hood of the extinguishing system will be inspected for proper direction of nozzles, cleanliness and proper placement of filters. The surveyor will also look at the general condition of sprinklers in the kitchen and inside the refrigeration/freezers, if provided.
EC and emergency management
At some point during the survey, the facility manager will schedule an EC session and an emergency management session. These will consist of the EC committee and the emergency preparedness committee. The LS surveyor will look through previous meeting minutes, ask questions pertaining to current hot topics (e.g., active shooter and mass casualty) and general questions on how the committee handles different situations.
Management plans must be approved annually and kept in a binder.
The hospital must take action to eliminate or minimize risks to safety in the environment. Facility managers should be prepared to bring up a couple of examples where items on an action list have been resolved and corrected through the EC committee.
Final step
After the building tour has concluded, the final step is the exit conference, which will include a written summary of the survey findings.
Frank D. Rudilosso, PE, CHSP, is field director for facilities operations at NewYork-Presbyterian Hospital David H. Koch Center in New York City; and Jacob Allen McCall is director of engineering services at Memorial Hermann Sugar Land Hospital in Texas. They can be reached at frr9035@nyp.org and jacob.mccall@outlook.com. The opinions expressed in this publication are those of the authors and do not purport to represent the opinions or views of their respective employers.