A new approach to health care facilities maintenance
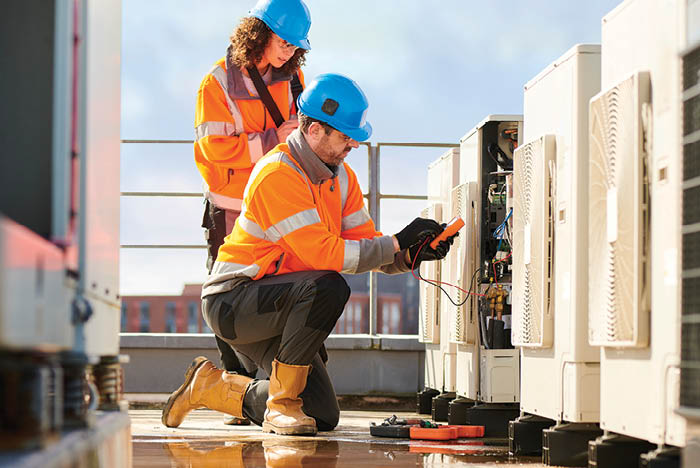
A health care facility’s maintenance program can be enhanced with reliability-centered maintenance.
Image by Getty Images
Most health care organizations have maintained their equipment per manufacturer recommendations or some form of preventive or scheduled maintenance based on regulatory or equipment need. However, these approaches do not address a system’s need to be managed for minimum failure as opposed to the failure of a system’s components.
The solution? Reliability-centered maintenance (RCM), an organizational-level strategy that can enhance the maintenance program in a health care facility by following four key principles: preserve system function; identify failure modes that can impact system function; prioritize the failure modes; and choose suitable and effective tasks to control the failure modes.
With RCM, after determining the organization’s most critical assets and functions, one can optimize cost-effective maintenance approaches to improve functional reliability and availability of equipment while also decreasing system failures. And that can result in saving more time and money otherwise spent on maintenance and repairs that other methodologies incur, including preventive maintenance and reactive maintenance.
RCM value proposition
Devin Hugie, FASHE, CHFM, CHC, president and CEO of DHI Consulting in Spencer, Ind., says health care has fallen behind other fields when it comes to efficiently and resourcefully operating a maintenance and repair program.
“We need to embrace the numerous opportunities provided by RCM, which identifies the most effective preventive maintenance task for facility component equipment,” he says. “RCM establishes a repeatable program with documented processes and procedures. It provides a framework to improve maintenance efficiency and functional reliability of assets.”
W. Thomas Schipper, CCE, FASHE, manager of environmental risk for Children’s Hospital of Orange County, Calif., and a past president of the American Society for Health Care Engineering (ASHE), agrees that hospitals and other medical facilities need to get on the RCM bandwagon.
“In health care, we often look at failures not in terms of comprehensive cost of downtime but as problems to be solved. We’ve often followed the advice of ‘get it done,’” Schipper says. “We are increasingly learning that, instead of focusing on ensuring that equipment components are merely working and managing their failures in a traditional way, we should be thinking outside the box and concentrating on more reliable operation of functional units. RCM can make that happen.”
Many organizations aren’t aware of RCM or don’t take the time to look more closely at how it can benefit them, according to Chad Beebe, AIA, CHFM, CFPS, CBO, FASHE, deputy executive director of ASHE. “I’m reminded of a cartoon about a caveman who tries to convince another caveman to swap out his square wheel with a round one,” Beebe says. “The square-wheel user replies, ‘I don’t have time to deal with that.’”
Resources
David Lockhart, CHFM, CEM, FASHE, an ASHE Region 9 representative, insists that facility managers and engineers can’t afford to adopt that mindset. “Every facility has so many variables, and implementing a one-size-fits-all preventive maintenance methodology usually results in reactive performance — basically waiting until something breaks,” Lockhart says. “Eventually, motors, bearings and actuators are going to fail. But why are they failing? What is the best maintenance strategy for the facility to reduce these failures? Can you apply a type of condition monitoring to that failure mode? These questions and their answers are fundamental to how RCM can help a team better understand its equipment and systems and how they should best operate and be maintained to the highest and most efficient means.”
Lockhart believes the timing is ideal for implementing RCM in health facilities due to three important changes that have impacted health care:
- Increased regulatory oversight requires the need to understand and manage risk.
- Patients have a greater choice today as to where they can receive care and the types of services they desire, which requires organizations to improve quality outcomes.
- There is increased urgency to cut costs and run more affordable operations.
Advantages and caveats
RCM yields several advantages, from identifying potential hidden faults or failures and decreasing maintenance expenses to minimizing downtime and increasing staff satisfaction.
“With RCM, the maintenance staff is challenged to plan the best maintenance program using condition-based monitoring (CBM) equipment such as vibration accelerometers and infrared (IR) scanners to identify problems before they become a problem,” says Roy Hirchak, CHFM, BSEE, chief of the facilities operations branch of the Military Health System’s Defense Health Agency in Falls Church, Va. “If they find a task with no benefit, they remove the task. The good news is that an RCM program can be tailored to a few systems or all systems; it’s up to the maintenance team and their bandwidth.”
Perhaps RCM’s biggest plus is the development of measurable outcomes that reduce risk and drive improved efficiencies in system operation and team performance. “As the program matures, it will not only improve operational performance, it will also lead to improved highly reliable installations,” Lockhart says.
Caveats may apply, however. “The work of a skilled RCM facilitator applied at two separate institutions will produce necessarily different outcomes based on the components of the system design for each institution,” says Schipper. “For example, if a system contains either direct-drive or belt-driven equipment to provide a function, the final maintenance parameters of the systems will be different.”
Additionally, RCM can be viewed negatively by some staff. Lockhart says this change management program “disrupts how things have always been done. It can appear to threaten the existing culture, knowledge and staffing performance, as it is often seen as a staffing reduction program.”
Leadership also may balk if they perceive an RCM program as too expensive to implement. “There are some costs involved with training staff, bringing in an RCM consultant to get it started and purchasing CBM equipment,” Hirchak says. “But these costs are not large in the grand scheme of things.”
Alternatives to RCM
So why adopt RCM when other popular methodologies exist, including reactive maintenance, maintenance task analysis, preventive maintenance optimization, peer-to-peer review, failure modes and effects analysis, and root cause analysis?
“Other maintenance approaches attempt methods for becoming more effective and efficient,” says Schipper. “But without the quality cycle of RCM analysis as a driving force, one can only be assured of equipment component reliability as opposed to the functional unit reliability of critical failure points provided by the analysis.”
RCM proponents believe that maintenance should focus on the critical failure points of system functions instead of equipment system components. This realization reveals that most alternative programs are less than adequate.
“For example, traditional preventive maintenance is an experiential series of prudent guesses related to components and not functional definitions. Reactive maintenance requires no analysis — just a response to problems,” Schipper says. “And predictive maintenance uses the measurement tools of RCM but usually as a measure of equipment component health and not for the management of a system’s functions.”
Too many organizations merely employ programs that simply follow a manufacturer’s recommendations for upkeep and repair. But that can be a recipe for disaster, Hirchak believes.
“Reactive programs that follow the ‘fix-it-when-it-breaks’ philosophy can lead to regret because they often expose a lack of planning for staff, parts and material that can make a simple repair take more time and at a higher cost with a detrimental impact to operations,” Hirchak says.
Cases in point
Recalling his experiences as a Joint Commission surveyor, Schipper relates three examples that show the value of RCM.
“With air handlers, one normally needs to ensure that filter banks are changed out on a set schedule and monitored by differential pressure devices,” he offers as the first example. “However, with an RCM approach, the filters would not be touched until it was seen that the quality of the air was being affected.”
Secondly, generator load testing is traditionally performed annually when monthly testing shows greater than a 30% load. But RCM would result in the elimination of the annual test for otherwise-compliant generators.
“That’s because we are required to avoid redundant work when we have what’s needed in place for a reliable system function,” Schipper says. “When RCM principles of functionality are applied, it becomes clear that redundant activities do not enhance reliability.”
For the third example, consider that defibrillator testing is usually conducted by nursing on a shift or daily basis when the device’s technology includes a self-check function. However, an RCM-based retroactive study can discover that the most common cause of defibrillator failure is enhanced by multiple daily tests.
“Under an RCM program, these three scenarios would be modified or eliminated after being examined through the lens of system functionality,” Schipper says. “Consequently, dollars for time, materials and manpower can be regained for other purposes.”
RCM amenability
Of course, some equipment and systems can benefit from RCM more than others.
“The ventilation and cooling system and generators are usually recommended as a starting place for RCM because they affect the whole facility,” Schipper says. “Beginning with these systems, the facility team can gain knowledge in shifting from a component-based maintenance concept to a functional reliability concept.”
Others recommend also applying RCM to equipment that uses CBM technologies and gets rotated.
“This includes chiller water and hot water pumps, booster pumps, sewage ejectors, circulating and sump pumps; electric motors for the boiler and chillers; and many different fans, like exhaust fans, cooling tower fans and AHU fan shafts,” Hirchak says. “And there are hundreds of pieces of rotating equipment in a facility that each have some type of bearing on their shafts that can fail due to improper alignment, lubrication issues and excessive vibrations. A simple vibration analysis and IR scan can spot problems early on and allow for minimal impact when that equipment needs to go offline for repairs.”
Hugie believes RCM should also be applied to all systems and equipment that are classified as critical, which can be determined by performing risk assessments. “As less-complex equipment and systems are gradually added to an RCM program, less rigorous RCM analyses can be conducted,” Schipper says. “Also, as functional units become more self-reliant, thanks to self-diagnostic functions and more solid-state components, the need for formal RCM analyses is minimized.”
Getting started
A successful RCM program starts with getting buy-in from leadership and preparing staff for a change in maintenance philosophy. RCM represents a culture change as well as a technical change in how maintenance is performed; facilities managers should expect questions, doubts and pushback, and plan for how to address these concerns.
“Assign one or more local champions to the RCM initiative and have this person or group attend programs, courses and meetings on RCM,” Schipper says. “Also, invite someone familiar with RCM to speak at the facility and explain its concepts to all the management and technicians involved in the maintenance program.”
Next, develop an RCM program specifically tailored to the facility’s needs and resources, and plan to roll out the program carefully without overloading maintenance and leadership staff. The following steps should be considered:
- Review maintenance records to determine items to include in the RCM program — especially equipment prone to failures.
- Once the equipment has been identified, the maintenance team must verify it and its subcomponents and functions so that a criticality assessment can be performed. “For example, normally the basic information on a pump is recorded in the computerized maintenance management system; but did they include the bearing type? This information would be necessary for the vibration analyzer since the bearing type defines its characteristics,” says Hirchak.
- Analyze system functions so that items within the system can be ranked or prioritized and asset allocation of resources can be better determined.
- Perform failure mode and effects analyses. “This will help identify possible failures and risks of failure and their impacts on individual components,” Hirchak says.
- Develop an enhanced maintenance plan to improve the efficiency and effectiveness of the RCM program.
- Establish baselines using CBM to determine starting points for equipment and apply key performance indicators. “For example, a pump can have a vibration and IR scan. The pump’s vibration signature will be the baseline; when the next vibration scan is performed, the facility’s team can determine if there are any deviations,” Hirchak says. “The CBM technician can use these deviations to inform the mechanics when the equipment is running properly or if it needs service and to what component.”
Once the RCM program has been approved, facilities managers should provide necessary RCM training for all staff involved, including management and technicians.
Don’t give up
Lastly, organizations should prepare for possible setbacks and learning curves along the way.
“Don’t give up on an RCM program prematurely,” says Hirchak. “Remember that, in the long run, it can be a great methodology that will help an organization lower overall costs and run more efficiently.”
“My favorite thing about RCM is that it reveals what is worth doing. It’s a method to ensure asset function,” says Terrence O’Hanlon, CEO of Reliabilityweb Inc. in Fort Myers, Fla. “But remember that creating and executing the plan isn’t enough; one has to evaluate an RCM program regularly and make changes when necessary.”
Erik J. Martin is a freelance writer based in Oak Lawn, Ill.