Providence Regional Medical Center Everett updates decades-old infrastructure
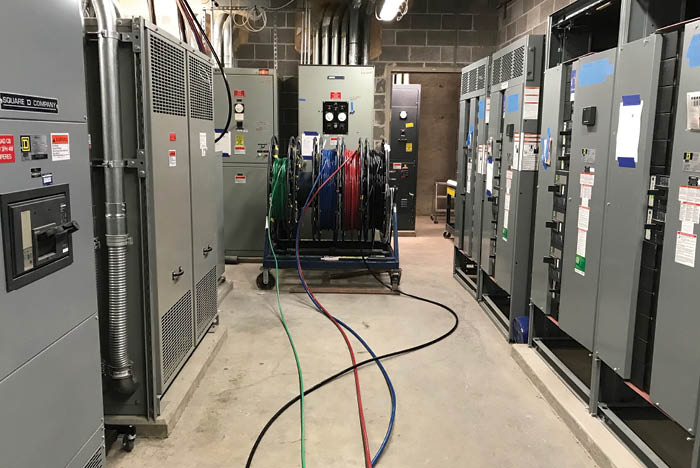
Image courtesy of Stantec
Replacing a main switchboard at a busy hospital that must remain operational is a tall task, especially when that electrical distribution switchboard dates back to the 1960s.
Consequently, when Providence Regional Medical Center Everett (PRMCE) in Everett, Wash., made the commitment to undergo this infrastructure project, it knew it had to carefully choose the experts it needed for this complex switchover.
The old switchboard, which served the A and B wings of PRMCE’s Colby campus, powered portions of the facility that houses patient rooms and 14 different departments, including the main lab and pharmacy. The switchboard was nestled in a small, one-entrance electrical room that didn’t comply with current codes for separation or working clearances.
“The equipment was old and difficult to find replacement parts for. There was concern about the safety of the electricians working on the gear and the fear that, if the breakers were opened, they may not close again or that a failure in the board could take out power to a sizable portion of the campus,” says Maureen D. Jackson, PE, the engineer of record and principal at the Lynnwood, Wash., office of Stantec, an integrated design and consulting firm.
The project called for replacing the outdated switchboard with a code-compliant installation that would ensure reliable power to the affected parts of the hospital for many years to come.
That meant the installation of a new normal service unit substation with distribution and new emergency power distribution switchboards along with replacement of the four automatic transfer switches downstream of the switchboard that served the A and B wings of the medical center.
The highest priority was keeping the power flowing during construction so that critical lifesaving functions could continue to operate in the 24/7 hospital.
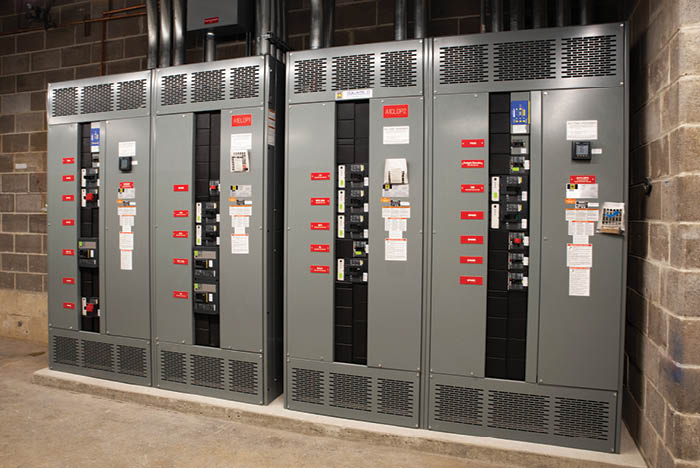
Image courtesy of Stantec
Accomplishing this switchboard substitution in such a tight space while keeping the medical center fully operational was tricky to say the least.
Stantec worked to design a layout that would allow for the systematic replacement of each piece of gear. Team members on staff at the hospital conducted meetings with each department that would be impacted by the shutdowns for cutovers. They researched panel indices and created color-coded drawings for each department indicating areas affected by each shutdown.
“During construction in phase 1, the initial shutdowns went according to plan. But shutdown number seven, which was planned to take 10 hours, turned into 22,” Jackson says. “Fortunately, patient safety was never compromised, but we needed to course-correct and change the strategy for the cutover work to reduce risks and increase safety for the electricians, patients and staff.”
To prevent longer downtime with future shutdowns needed, Stantec worked with Seattle-headquartered VECA Electric & Technologies, the electrical contracting firm enlisted for the project. Their solution? Connect to a temporary feed for as long as needed to get new gear in place and all new feeders pulled, then cut loads back to the new distribution equipment.
“Lessons were learned from every shutdown to make the next one smoother. But the biggest lesson was the importance of adaptability and thinking on our feet to solve problems as they arose,” Jackson says.
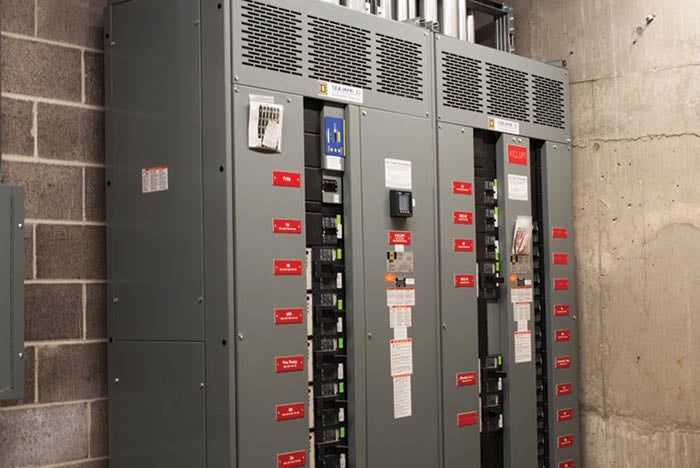
Image courtesy of Stantec
Cody Leckner, project superintendent and VECA’s electrical contractor, says the team was able to make this task seamless, with no surprise outages, by coordinating closely with the hospital’s facilities department.
“Communication was consistent throughout the project, which eliminated missed steps. When we ran into unforeseen issues, we stopped, communicated and adapted the plan to eliminate reactionary mistakes,” he says.
Jim Muldowney, project electrical contractor and general foreman for VECA, credits the PRMCE team and Stantec with carefully planning project construction phases and updating panel schedules.
“This was the most challenging project I had undertaken in my 28 years of being an electrician,” Muldowney says. “Among the biggest hurdles overcome were squeezing a lot of big pipe and equipment into small electrical rooms and corridors and putting timelines to our shutdowns with as little impact to the hospital as possible.”
Michael Newbury, senior principal with Stantec, expressed the team’s pride in receiving the Vista Award for Infrastructure from the American Society for Health Care Engineering (ASHE) of the American Hospital Association.
“Our project approach focused on creativity and innovation to accomplish a very complicated design challenge with a safe and positive outcome,” Newbury says. “None of us got into the health care engineering field to win awards, but being recognized by ASHE is just icing on the cake.”
Project Info:
- Square feet: 274,000
- Number of beds: 170
- Cost: $4,259,649
- Start date: July 2017
- Completion date: September 2020
Team Members:
- David Wachob, project construction manager and owner, Providence Real Estate Strategy and Operations, Everett, Wash.
- Peter M. Smeltz, project facilities manager, Providence Regional Medical Center
- Chris Britton, project facilities engineer and facilities supervisor, Providence Regional Medical Center, Everett
- Maureen D. Jackson, PE, engineer of record, electrical principal, Stantec, Lynnwood, Wash.
- Jack Glover, project manager and electrical principal, Stantec, Lynnwood
- Jim Muldowney, project electrical contractor and general foreman, VECA Electric & Technologies, Seattle
- Cody Leckner, project superintendent and electrical contractor, VECA Electric & Technologies