Hospitals contend with construction challenges
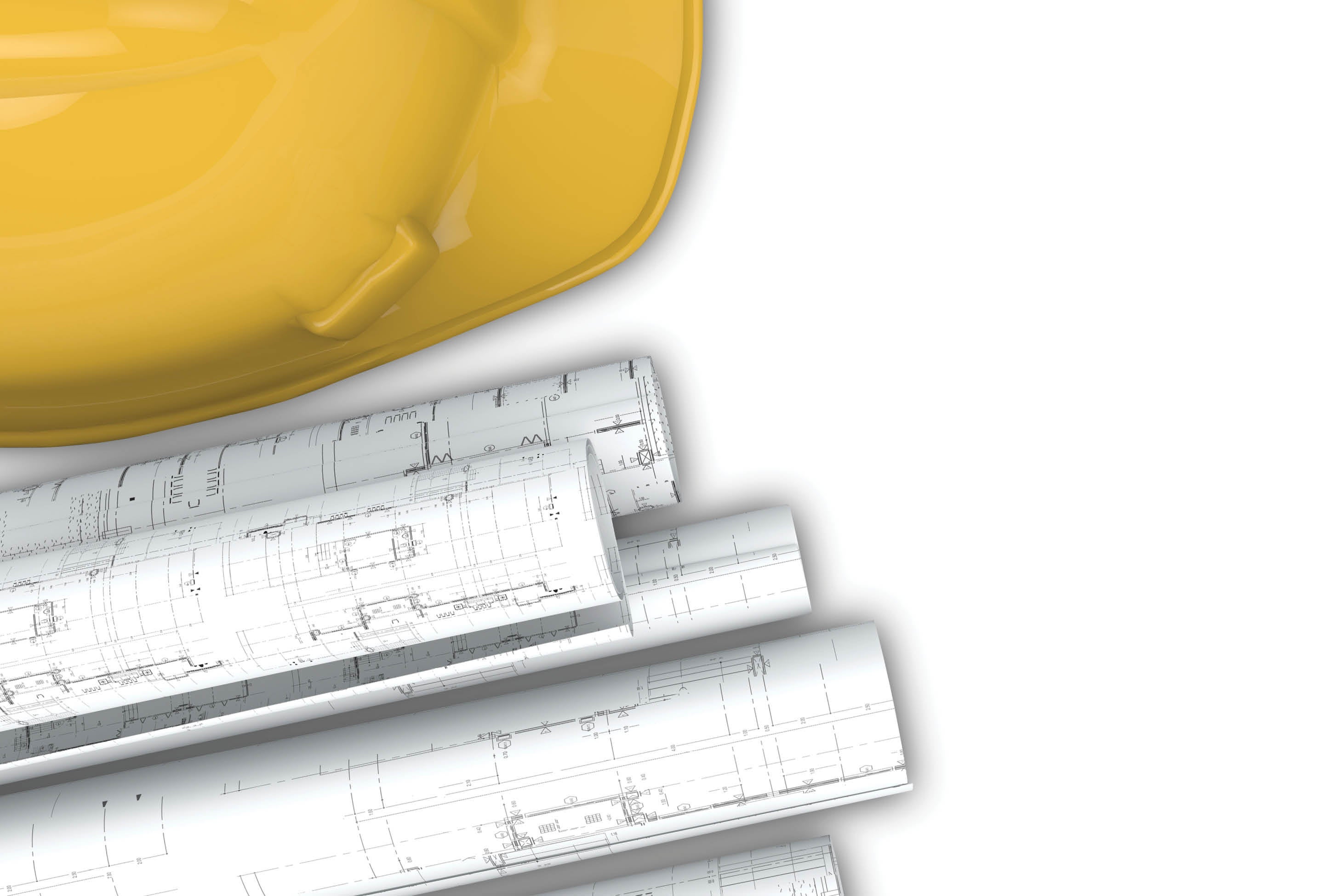
Image from Getty Images
Like a lot of hospitals, Samaritan Healthcare in Moses Lake, Wash., postponed construction plans when COVID-19 hit in 2020. And when the economy began rebounding, the facility resumed plans for its $157 million facility to replace the original structure built in 1947.
Because the original building was landlocked, the hospital needed a larger, new facility at a new location with room to grow. Samaritan secured funding and finalized designs for the new 160,000-square-foot facility in 2019. After two years of a turbulent economy, Joe Kunkel, a consultant on the project, began updating plans to reflect the current construction market. The news was not good. In spring 2022, inflation hit a 40-year high.
“Inflation has hit health care construction hard, and that’s consistent with what I am seeing with my clients across the board,” says Kunkel, owner of The Healthcare Collaborative Group, Portland, Ore. “Supply and workforce shortages were already huge challenges in a rural area like Moses Lake. Inflation intensifies all the other challenges with supply and worker shortages.”
Samaritan Healthcare will not break ground this summer as anticipated and is evaluating next steps on the project. But planning is difficult with supply and labor fluctuations and long lead times. Kunkel has been waiting almost two years for an electric generator and a year for an air handler. “It puts you in the position of having to make decisions early, knowing designs may need to change accordingly.”
And, at time of this publication, inflation continues to escalate. Kunkel estimates that rates are rising 2% a month.
Theresa Sullivan, chief executive officer at Samaritan Hospital, says this economy is unlike any she’s seen in her 30 years in health care. “We have gone through difficulties in health care, but I don’t think I’ve seen so many challenges at the same time in our economy at this level,” Sullivan says.
Supply and worker shortages
Nevertheless, construction teams are getting projects done. They are developing workarounds, finding creative ways to cut costs, substituting materials and products, and relying heavily on procurement. Teams are doing as much work in preconstruction as possible. They are ordering early and locking in prices. Teams are doing more work in-house. And more than ever, CEOs, designers, architects, engineers, contractors and laborers are working cohesively to save time, money and steps wherever possible.
But obstacles are significant. Existing workforce shortages exacerbated during COVID-19 haven’t leveled off. Hospitals resuming construction post-COVID-19 are creating a high demand for materials. Supply chain interruptions, triggered in part by labor shortages, are causing major delays and cost overruns. And health care is competing with other industries for the same workers and supplies — another cost driver. The rise in fuel costs is driving up the cost of shipping worldwide. As of August, the U.S. rate of inflation was 9.1%.
With so many variables, hospitals are approaching construction and renovations from various angles.
“We are actually seeing a strong rebound in procurement nationwide for the health care sector with more opportunities for larger health care construction projects emerging,” says Mark Howell, senior vice president at Skanska USA in Seattle. “At the same time, we are also seeing health care projects being paused and pushed out as organizations work to recover from the pandemic financially.”
And whether planning current or long-term projects, hospitals are taking the economic hit today. Projects planned for two or three years down the road are often bid with today’s exorbitant prices. Most suppliers are also only guaranteeing prices for shorter windows of time, so there is a need to lock prices and contracts in place now.
Hospitals are turning to experts to navigate the turbulent economic waters, says Dan Squiers, senior vice president and health care market lead at JLL, Orange County, Calif. “Hospitals are reaching out to firms like us to understand how escalating inflation will impact projects,” he says. “More are open to prepurchasing materials that have long lead times. They are starting to budget projects that may not happen for a year or more.”
According to 2022 data from the Associated General Contractors of America (AGC), the cost of construction materials jumped more than 20% from January 2021 to January 2022. In the last year, the cost of steel has increased 12%, paint has increased 20% and concrete has gone up 20%, according to Dan Haupt, CHFM, CHC, director of the health care division at AG|CM Inc., a construction management and estimating firm in Texas.
“Concrete prices cannot be guaranteed past one week,” Haupt says. “Or even daily. Sometimes the price is given on the day of the pour.”
Prices are driven by shortages in materials like copper, steel, concrete, lumber, glass, paint and roofing materials. There is a global shortage of computer microchips critical to electronic equipment like HVAC direct digital controls, creating lengthy lead times. “Air conditioning equipment is being delayed up to 14 months with cost increases of 12% to 15%,” says Haupt. “Some electrical equipment is sitting on ships up to four months waiting for access to ports.”
Even a missing part — no matter how small — can cause big setbacks. Waiting for roof fasteners can hold up an entire project. Previously easy-to-access materials are causing logjams.
“The shortage in electrical equipment is undoubtedly a huge issue, but basic materials are causing delays as well,” says Randy Keiser, national health care director at Turner Construction Co. “In one case, we had all the other necessary materials, but we couldn’t get the paint. It’s the first time I’ve ever had a job put on hold because of paint! And the problem is not just with manufacturers, it’s with their suppliers. Shortages start downstream.”
Products made outside of the U.S. are harder to get overall. And rising fuel costs are impacting projects across the board, says Mark Kenneday, director of strategy and market development for health care at Gordian, a Greenville, S.C.-based provider of insights, technology and comprehensive services for all phases of the building life cycle. “It may sound like inflation is an over-the-table kind of index, but it impacts certain commodities more than others. Right now, you can’t say there’s a 9% inflation rate for oil and gas, because the rate is much higher for those industries,” says Kenneday, a past president of the American Society for Health Care Engineering (ASHE).
Labor shortages are a huge problem. Manufacturers are lacking workers to make supplies, driving up prices. Contractors short of skilled trade workers are passing the cost onto hospitals. “My organization is experiencing a 15% to 25% increase in outsourced labor costs, and a 10% to 30% increase in contract renewals,” says Michael Huff, CHFM, CHC, CHCPE, CPMM, CRCST, CHL, facility manager at Baylor Scott & White Medical Center, Temple, Texas.
Workforce shortages also fluctuate based on geography, says ASHE President Shadie (Shay) R. Rankhorn Jr., SASHE, CHFM, CHC. “In rural areas, it is harder to find qualified contractors who aren’t already booked out for several months to a year or who don’t want to leave urban areas for tighter-margin projects in rural areas.”
Budget and schedule headaches
Not surprisingly, many health care construction projects are over budget and behind schedule. Haupt has seen preconstruction costs for projects skyrocket in cities like San Antonio, Houston and Dallas. In the past year, the preconstruction estimated cost of $52 million for a 50-bed rural hospital in South Texas has increased by 17%. The $150 million preconstruction cost of a 250-bed acute care hospital increased by 15%, Haupt says.
Even small projects are running up big price tags. A pharmacy project at Pennsylvania Hospital for Penn Medicine in Philadelphia ended up doubling its cost due to supply chain issues and time and space constraints, says Jeff O’Neill, who was senior director of facilities at Pennsylvania Hospital at the time of the project. The renovation was required to comply with USP General Chapter <800>, which regulates the safe handling of hazardous drugs.
The project was designed in 2019 but delayed in 2020 by COVID-19. When construction was set to launch, supplies were short and lead times were long. The wait for the air handlers alone was 12 to 16 weeks. Because of pandemic requirements and the size of the space, only limited trade personnel could work together in the space, extending the schedule and overhead costs. Ultimately, the project ended up costing approximately $4,000 per square foot for a total of $2 million — double the original projected cost.
“With a larger project, a $1 million increase wouldn’t be unusual, but increasing a small project by $1 million and such a high percentage increase really gets the attention of the C-suite,” O’Neill says. “Obviously, the dollar per square foot figure is alarming, but that is not always an accurate measure. The small area, combined with the higher-cost air systems, skews the dollar-per-square-foot metric.”
In the past two years, the University of Maryland Medical System, headquartered in Baltimore, designed three free-standing medical facilities ranging from $30 to $60 million. While the projects were challenging and there were some delays, for the most part they finished on time and within budget, says Darryl Mealy, vice president of construction and facilities planning. But the economy is unpredictable. “We bid a job last year and then rebid it this spring and in about 15 months the cost of the project increased by 13%. That’s almost 1% a month,” he says.
At Brattleboro Memorial Hospital in Vermont, the team purchased materials for a three-operating room replacement and medical office space before COVID-19 but faced cost hikes down the line, according to Rob Prohaska, CHFM, director of plant services.
“There is only so much buying in advance that can be expected,” Prohaska says. “We had large mechanical equipment committed through purchase orders. However, as the project progressed, material costs escalated for materials like ductwork and wire. So, we granted one-time material cost escalations to electrical and mechanical contracts.”
Collaboration is crucial
Hospitals in their second year of a turbulent economy are relying on creativity, innovation and hard work to finish projects rife with challenges. Kenneday recommends a collaborative project delivery approach that involves the entire construction team in planning from day one. The one-team, one-contract approach helps to avoid changes — and cost overruns — down the road.
“In a collaborative delivery model, all team members are sitting at the table from the beginning,” Kenneday says. “The contractor has a good idea of what they can and can’t buy or build, and can tell the design team up front. This way, a contractor won’t step in several months into the project and tell the team certain materials aren’t available. Or, if an architect suggests a change at a time when materials aren’t available or are too costly, it can slow the project down and increase costs. Those situations are avoided through a collaborative project delivery process.”
Mike Bruskin, vice president and chief procurement officer at Turner Construction Co., says these unsteady financial times call for cohesive teamwork to avoid the back and forth that can cause serious setbacks.
“We have to work together with trade partners and designers to expedite the review and approval process,” says Bruskin. “We recommend shop drawings and submittals be reviewed collaboratively, changes be made at the review table, and returned at least ‘Approved as noted’ because ‘Revise and resubmit’ often results in losing our place in the manufacturing line. Bottom line: release early, ensure it is approved and maintain the production slot.”
And hospitals are finding ways to cut through lengthy supply lead times, including tracking down supply and material alternatives.
“Clients are asking us to analyze alternative material sources and options to mitigate supply chain and cost impacts to the budgets,” Howell says. During construction of the UNC Health surgical tower in Chapel Hill, N.C., the mechanical subcontractor notified the team that under-slab CPVC pipe wouldn’t be available in time to reach a scheduled milestone. The Skanska USA team turned to a longtime supplier to provide an alternative source in time to meet the deadline.
Some hospitals are relying on custom manufacturers to get materials quicker. Teams are expanding options for products and materials to work around shortages, Bruskin says. “If a designer is married to just one idea, I guarantee there will be problems,” he says.
Preparing for potential delays in advance was central to the recent construction of an outreach clinic by Iowa Specialty Hospitals & Clinics, Clarion, Iowa.
“We planned to have everything on-site before the project started, which really helped us meet our goals,” says Steve Simonin, president and CEO. “We did experience delays and shortages with some projects, including doors, but we got as many materials as possible on-site before we started.” Webster Clinic, one of 11 outreach clinics in the hospital’s system, opened in spring 2022 on time and within budget.
Finally, some teams are improvising solutions on the fly. O’Neill’s team installed temporary wood doors while waiting for the specified high-impact doors. On one construction job, Keiser says they brought in a temporary generator to keep the project on schedule until the final products arrived. “We are creating a lot of workarounds to keep projects moving,” Keiser says. “We work extremely hard to track down materials. Supply chain issues have not derailed us, they have just made things tougher.”
Big-picture approach
Amid skyrocketing inflation and post-COVID-19 setbacks, health care leaders are cautious about predicting the future. But they believe construction demand will not taper off anytime soon.
“We are seeing a high demand for bed tower expansions, cancer centers, women’s and children’s hospitals, replacement hospitals, ambulatory surgery centers and facility infrastructure upgrades,” Howell says. “This is partly driven by pent-up demand for facilities after two-plus years of pandemic impacts and health care clients wanting to build now to lock in prices and get ahead of further cost escalation.”
Adds O’Neill: “I’ve never seen costs go down once they are up, but the market is still hot enough that construction will continue growing in health care.”
While this is a challenging time in health care construction, hospitals can learn from their experiences, Keiser says. One major takeaway: hospitals can’t expect a supply chain to run perfectly. And as hard as it might be, hospitals need to maintain a big-picture approach to design at a time when day-to-day decisions are so urgent.
“Hospitals we are designing today are much more complex,” Keiser says. “We need to build hospitals that are COVID-19-resistant, environmentally sustainable and that meet continually changing regulations. While we have major concerns about getting equipment like air handlers, we still need to keep the bigger picture in mind.”
Beth Burmahl is a freelance writer based in Carbon Cliff, Ill., and a regular Health Facilities Management contributor.