Building a community and a new health facility
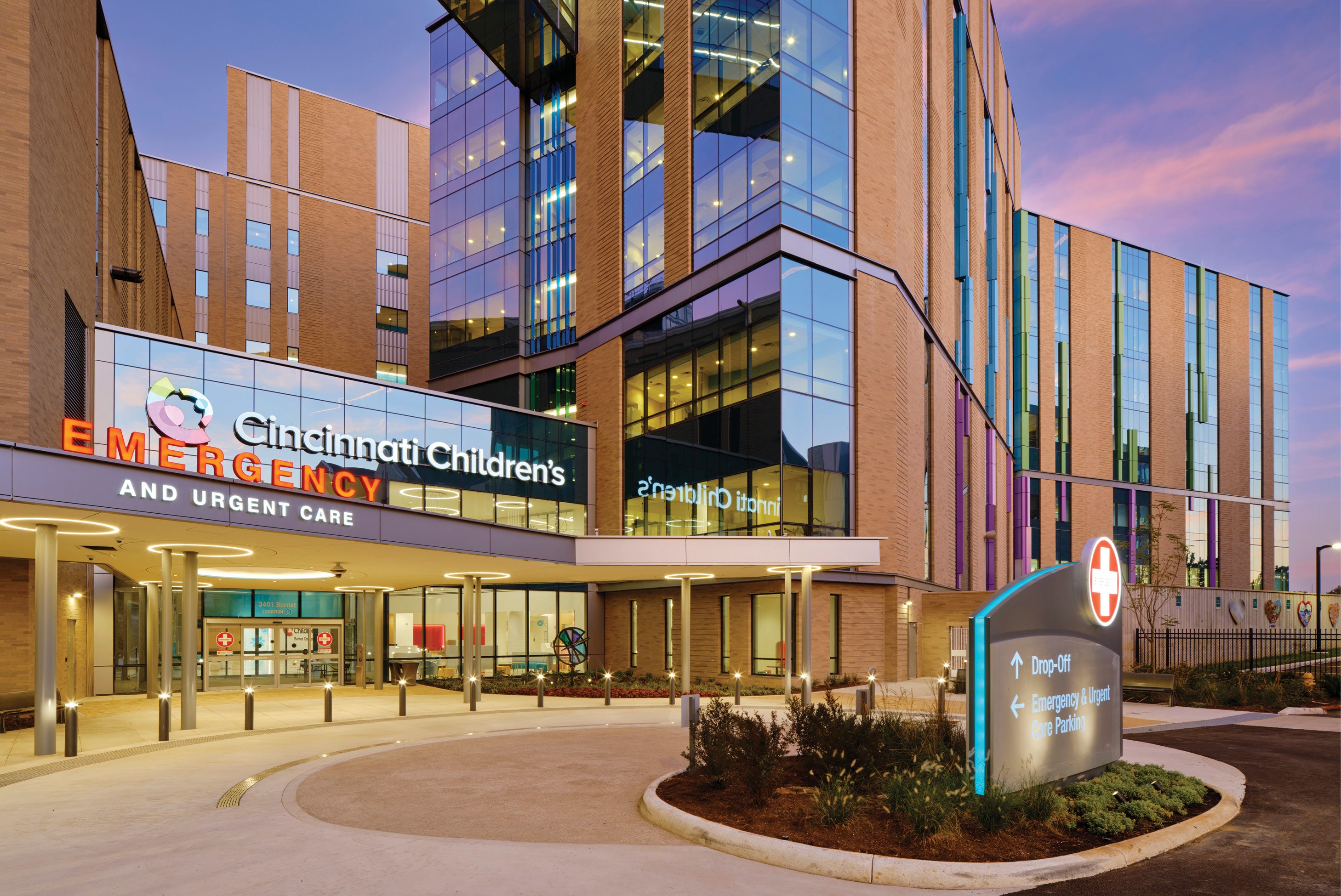
Cincinnati Children’s 650,000-square-foot critical care building encompasses 249 patient beds, an emergency department, operating rooms, intensive care units and more amid an urban neighborhood campus.
Photo by Ryan Hurtz Photography and courtesy of Messer Construction Co.
As a pillar of the Uptown Cincinnati community, Cincinnati Children’s Hospital Medical Center is home to 16,000 employees and serves more than 60,000 patients annually. The flurry of activity doesn’t stop outside the hospital’s doors, as the campus is adjacent to a residential neighborhood, two other active hospitals, the Cincinnati Zoo & Botanical Gardens and the world’s largest Ronald McDonald House.
Given the busy location, safety, schedule and logistics undoubtedly are key priorities anytime Cincinnati Children’s takes on an expansion or renovation project. But what about looking at a construction project through a wider lens? Is it possible to positively impact the economic outlook of residents throughout and beyond the construction process, just as the resulting building will positively impact patients, families and medical staff for years to come?
The answer is yes — when collaboration and innovation align through a shared vision.
Transformational vision
When Cincinnati Children’s released a request for proposal (RFP) for a new critical care building (CCB) in 2015 — the beginning of the hospital’s largest expansion ever — it was with a vision of transforming the lives of people in the community through both quality of care and quality of life via career training and sustainable employment.
The first part of that vision is evident in the 650,000-square-foot tower that integrates seamlessly into the hospital’s existing campus in the center of a densely populated neighborhood.
Emphasizing continuity within every floor, the new CCB encompasses 249 patient beds; a 90,000-square-foot emergency department with a new entry/drop-off and parking garage; operating rooms, cardiovascular intensive care units and wet labs; pediatric and neonatal intensive care units; and a pharmacy, central sterile department and bone marrow transplant center.
The second part of that vision focused on building a pipeline of diverse candidates to enter sustainable, full-time careers through career training and professional development. This stemmed from an RFP challenge Cincinnati Children’s posed to potential construction partners: What ideas did local construction managers have for leveraging the project as a catalyst for sustainable job creation and investment in economic development among the hospital’s direct neighbors and the region’s subcontractors and suppliers?
The winning construction management (CM) team brought a threefold solution with defined goals to meet this challenge, including 30% spending with diverse suppliers; 25% workforce diversity employed on the project; and a new partnership with Cincinnati’s Easterseals Redwood’s Building Value program, which served as the genesis of the Uptown Workforce Development Initiative (UWDI), a program that works to break the cycle of poverty and build a pipeline of diverse talent.
The $600 million transformation opened in November 2021 as the largest private development in Cincinnati history — finishing ahead of schedule while also achieving many other goals, even with most of the work taking place during the pandemic. With the CCB now up and running, and UWDI continuing to expand, it’s remarkable to look back and see how this vision came to fruition through successful collaboration and innovation.
Innovation on the inside
To better care for critically ill patients from around the world, the project team mocked up areas of the building more than a year in advance of breaking ground so that physicians, nurses, researchers, staff, patients and families could feel the space and provide input to the project team, which included ZGF Architects LLP.
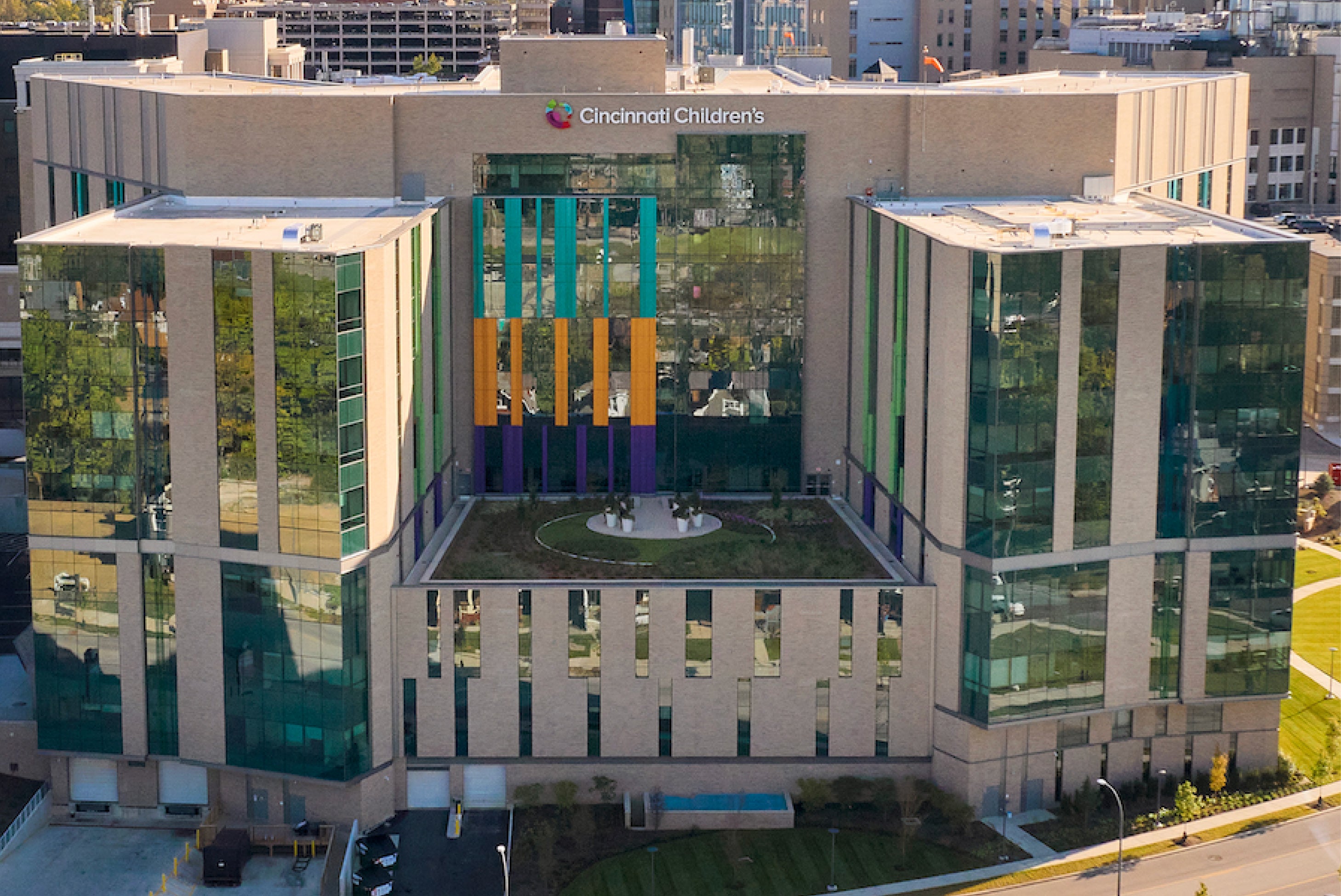
In addition to larger patient rooms, the critical care building includes family support spaces, four garden areas, expansive windows for natural light and more than 1,100 pieces of art.
Photo by Ryan Hurtz Photography and courtesy of Messer Construction Co.
In a rented warehouse, these stakeholders tested furniture, simulated procedures and walked through a 12-bed unit made up of more than 2,500 pieces of foam. This extensive feedback process kicked off in 2018, resulting in a space today that works for all users of the CCB. Plus, it saved Cincinnati Children’s at least $10 million in potential post-build changes.
Shortly after construction got under way, and well before COVID-19 became part of the equation, Cincinnati Children’s sought to shave four months off the schedule so that high-risk patients could be in the new building ahead of peak flu season. Prefabrication and flow scheduling were crucial to achieving the aggressive schedule goal.
More than half of the project was completed using prefabrication and off-site construction, including exterior wall panels; bathroom pods; mechanical, electrical and plumbing racks/medical gas racks; nurse stations; pass-through cabinets; zone valve box assemblies; duct risers/pipe risers; casing panels; electrical room in-box rough-ins; interior metal studs; a unitized curtain wall system; and a 110-foot connector bridge.
Flow scheduling consists of breaking a construction project down into similarly sized areas instead of covering an entire floor, determining the best sequence of subcontractor activities and then setting a rhythm (or “takt time”) for trade partners to complete the work.
For example, there were 66 total flow areas on the CCB, roughly nine per floor, that ranged from 8,000 square feet to 10,000 square feet. Flow areas started with above-ceiling rough-in activities and transitioned quickly to in-wall, rough-in activities and culminated in final finishes. This allowed Cincinnati Children’s and the design team to perform punch lists and final reviews in the same sequence to reduce the final push at the end of the project.
Rather than competing for space, flow scheduling allowed each subcontractor and their materials and equipment to move through each portion of the project at a predetermined pace — bringing predictability and enhanced safety to the construction process. All activities were completed on time for all key construction milestones.
The CM team’s unique approach to scheduling also drove safety and quality on the project and helped ensure everyone on-site could safely work throughout the pandemic.
All of this work behind the scenes set the stage for what the expansion offers patients, doctors, nurses and staff today: a net increase of about 100 beds with 30% more square footage for inpatient and outpatient care. Additionally, the emergency department is now three times larger and incorporates embedded imaging services.
Patient rooms are 50% larger in response to the typical length of stay for a patient. Additional areas of focus include family support spaces, four garden areas, expansive windows for natural light and more than 1,100 pieces of art in the hallways.
In short, the expansion is designed for how medicine is practiced today and reflects Cincinnati Children’s continued growth as one of the top pediatric medical centers in the country.
Innovation on the outside
In addition to delivering an innovative building, the project team committed to positively impacting the surrounding community and ensuring diverse participation on the project.
From a contractual standpoint, more than 35% of construction spending was with minority- and women-owned business enterprises (exceeding the 30% goal). From a workforce standpoint, 27% of on-the-job staff was diverse (exceeding the 25% goal). Two great outcomes, yet the community impact was far from over.
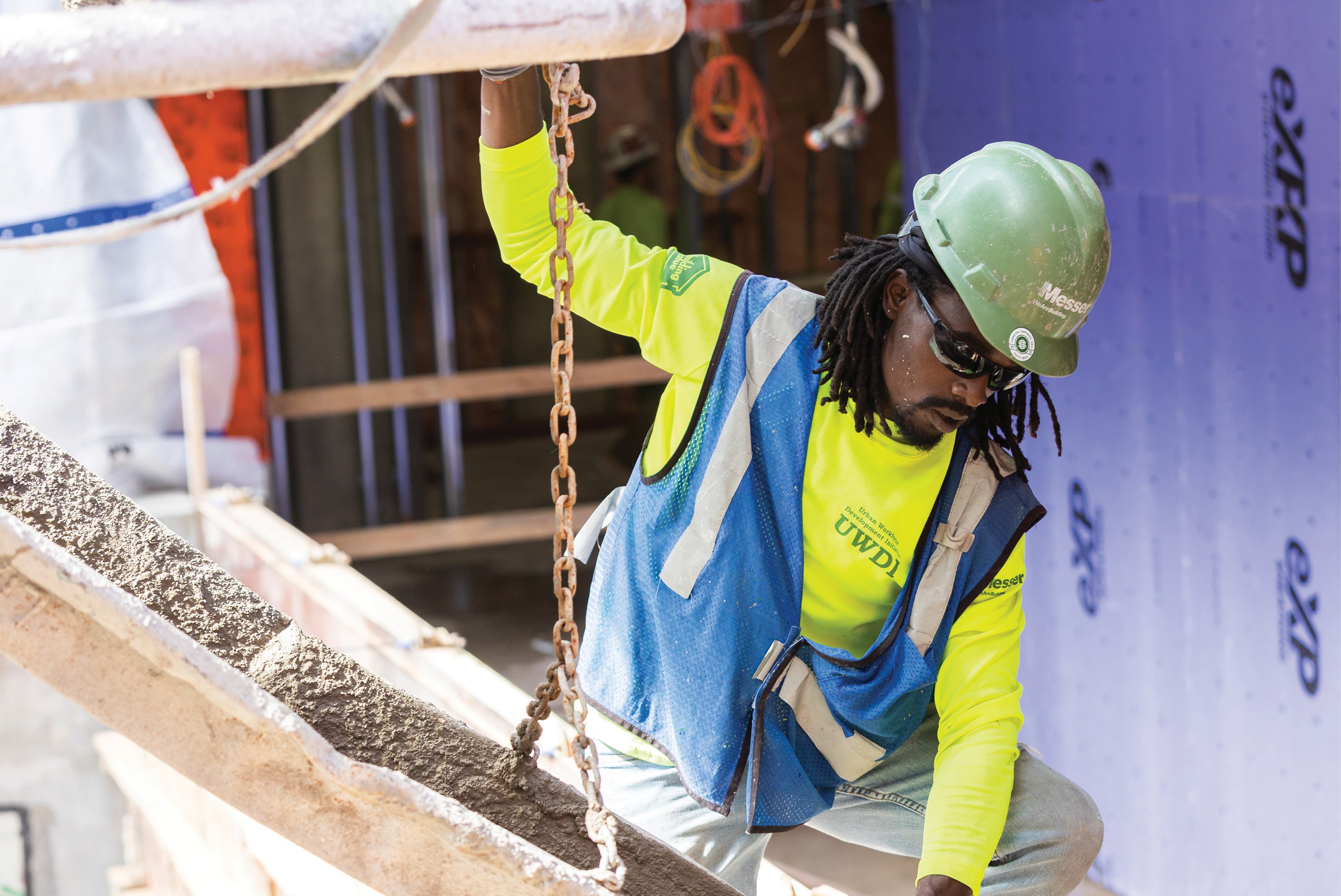
UWDI is focused on making a significant community impact by breaking the cycle of poverty and building a pipeline of diverse talent for the construction industry.
Photo courtesy of Messer Construction Co.
Consider the many talented individuals who work on a project anywhere on any given day and how many live in the neighborhood where they work. There are residents who watch construction happening where they live and they, too, have a vision to be part of it and to gain upward career mobility for themselves and their families. But there’s a fine line between wanting more and having the tools to do something to make it happen.
That’s why one of the biggest questions the project team had to answer was: Is it possible to position a construction project as an opportunity to move underemployed and unemployed diverse community members into full-time sustainable construction careers?
The answer is yes, when local partners aiming for the same target are brought together. UWDI sought to break the cycle of poverty while building a diverse pipeline in the construction trades, which have been experiencing a steady decline in talent acquisition over the past decade.
Here’s how UWDI worked on the Cincinnati Children’s project:
- Qualified members of the community who were interested in expanding their skill sets and having access to a guaranteed job placement were recruited into a 12-week “work hardening” program through Easterseals Redwood’s Building Value. It is a paid training program where their learning included nontechnical job skills, such as the value of teamwork, the importance of punctuality, following safety guidelines and having the right tools each day.
- Upon graduation, they received three months of additional paid hands-on training, mentorship, professional development and growth opportunities while working for the CM organization or a subcontractor partner as a co-op on the CCB project.
- At the conclusion of the co-op period, successful individuals were hired as full-time employees with Messer Construction Co. or with subcontractors, earning a competitive wage and receiving health, dental and pension benefits. There was also the option for graduates to move to other industries for those who decided not to stay in the construction field.
The initial goal was to create 50 sustainable careers and, as of January 2022, UWDI achieved that goal with 50 people employed by the CM organization and 16 different subcontractors.
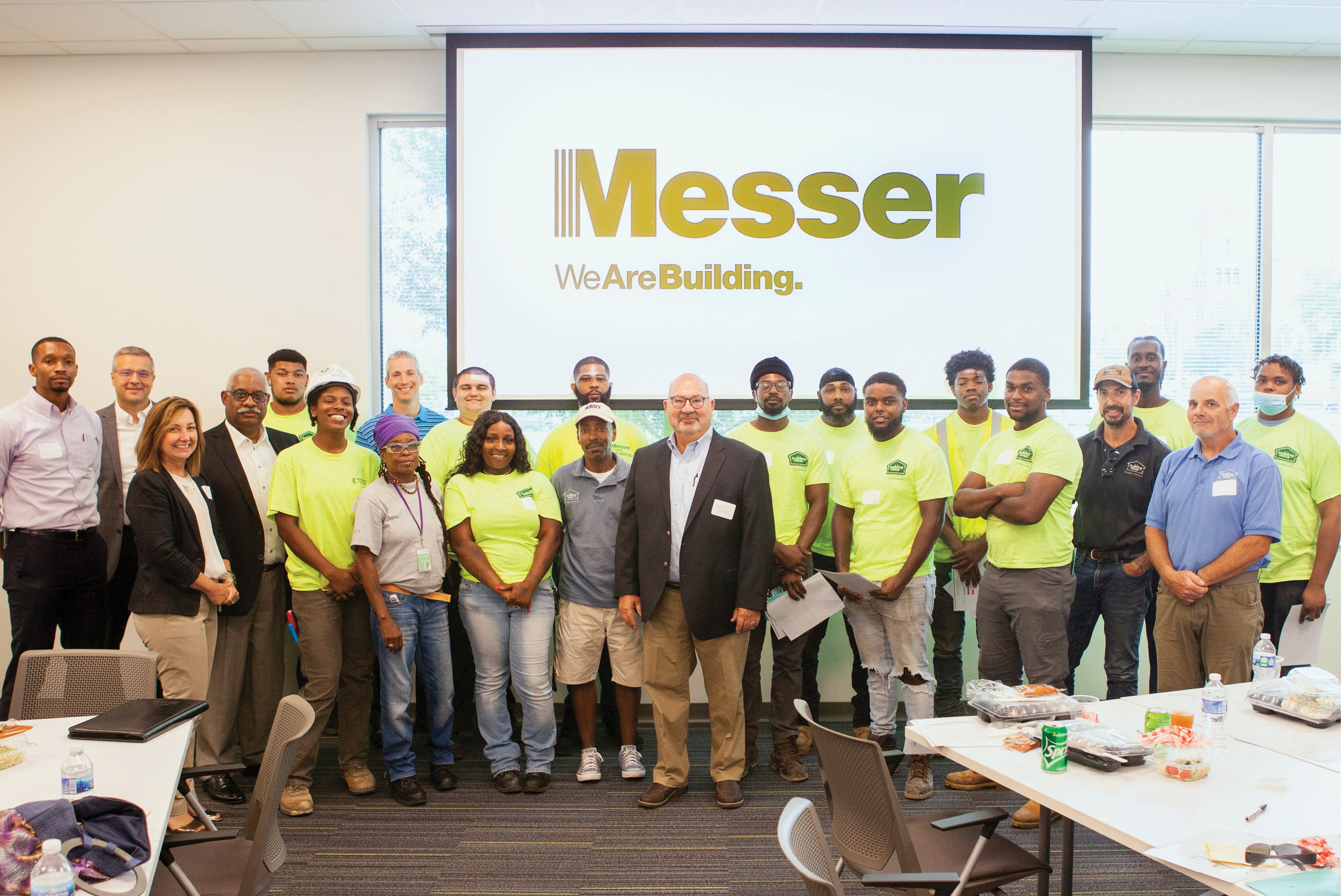
UWDI achieved the initial goal of creating 50 sustainable construction careers, and it continues to open up opportunities to turn individuals’ dreams for upward mobility into reality.
Photo courtesy of Messer Construction Co.
“We need to expose students to the construction industry, especially those in underserved neighborhoods,” says Michele O’Rourke, CEO of Cincinnati-based O’Rourke Wrecking Co., a subcontractor on the CCB project. “A career in any trade can be extremely lucrative as well as fulfilling. It is critical to the future of our industry to make inclusion of all these potential candidates a priority.”
“I like the role I have because it allows me to give back to my community, as well as improve the living environment for all the children and families inside Children’s hospital,” says Alesha Colson, a laborer who was hired by Messer.
Adds another UWDI graduate who had been stuck in a cycle of restaurant and retail jobs: “I needed to move toward another career. I always wanted to do construction; I just didn’t know how.”
There are two key differentiators for UWDI. The first is having a one-on-one case manager to help UWDI participants overcome barriers to consistent, full-time work, such as issues with housing, transportation, financial literacy, education, health care and child care. The case manager is committed to follow along for a year, regardless of which company hires the candidate, so there’s no abrupt drop-off in support. One graduate described his case manager as “real nice, upbeat and upfront … It was like I knew him my whole life.” The second differentiator is work hardening, which helped reduce attrition by exposing individuals to the conditions of a job site prior to being on one. Through this, it was possible to identify each person’s strengths and weaknesses to place them in positions where they would flourish. Work hardening also helped several individuals realize construction wasn’t for them, and they were supported to redirect into a different career path.
The participants’ most important takeaway is that their future is limitless. With what they’ve accomplished through UWDI, they know they can do anything they put their minds to. Plus, that message gets passed along to the next generation, which is key to lifting families out of poverty. “People see me in the neighborhood now with my uniform on and they say, ‘He did it!’” shared Russel Suttle, a laborer journeyperson.
Broadening the initiative
While Cincinnati Children’s was resolute about meeting its commitment to the Uptown community, perhaps the most exciting aspect of UWDI is that it’s outlasting the construction project.
UWDI is evolving to apply to a variety of other communities — opening up more opportunities to turn individuals’ dreams for upward mobility into reality.
Thus, its name has been broadened to the Urban Workforce Development Initiative. In partnership with community groups and subcontractors, Messer will lead UWDI throughout the Midwest and Southeast.
Turning construction projects into catalysts for social change
The Uptown Workforce Development Initiative model has the potential to be impactful in other cities across the country. In fact, it has already expanded to other projects in Cincinnati and other regions of the country under the expanded name Urban Workforce Development Initiative.
The following parameters help assess what’s needed to be successful:
- Reasonable goals and metrics. Construction managers shouldn’t expect to have 50 new hires in five months; it takes time to establish relationships, identify quality participants and nurture them through the process.
- A nonprofit organization that does quality work hardening. Beyond growing participants’ technical skills, it’s crucial to focus on enhancing their soft skills, such as communication and punctuality.
- A case manager who cares. This individual must be passionate about making a difference, embrace the process and understand the needs/nuances of the community.
- A supportive project owner. Having the owner be the biggest cheerleader in the marketplace truly validates the effort being invested in the initiative and amplifies the outcomes.
- A general contractor that can work with subcontractors to be part of the process. Strong subcontractor relationships are a must, including coaching and mentoring participants during the process and once they are hired.
- An open mind. Construction managers should be fluid enough to make changes as needed and be receptive to feedback from community stakeholders, participants and subcontractors.
About this article
This article is based on a presentation the authors gave at the 2021 International Summit & Exhibition on Health Facility Planning, Design & Construction (PDC Summit), which was held virtually.
Michael Browning is vice president of facility planning, design, construction and real estate at Cincinnati Children’s Hospital Medical Center; Stanford T. Williams is vice president and chief inclusion and diversity officer at Messer Construction Co. and Stanley Warrenhuffman is Messer’s economic inclusion manager responsible for the Urban Workforce Development Initiative.