Cleveland Clinic powers forward with major upgrades
The main campus of Cleveland Clinic encompasses 51 buildings and spans approximately 12.6 million square feet, where patients, staff and visitors rely on dependable and safe power distribution. But when one of a campus’s legacy buildings is 49 years old and filled with aging electrical infrastructure, the clock is ticking on reliability.
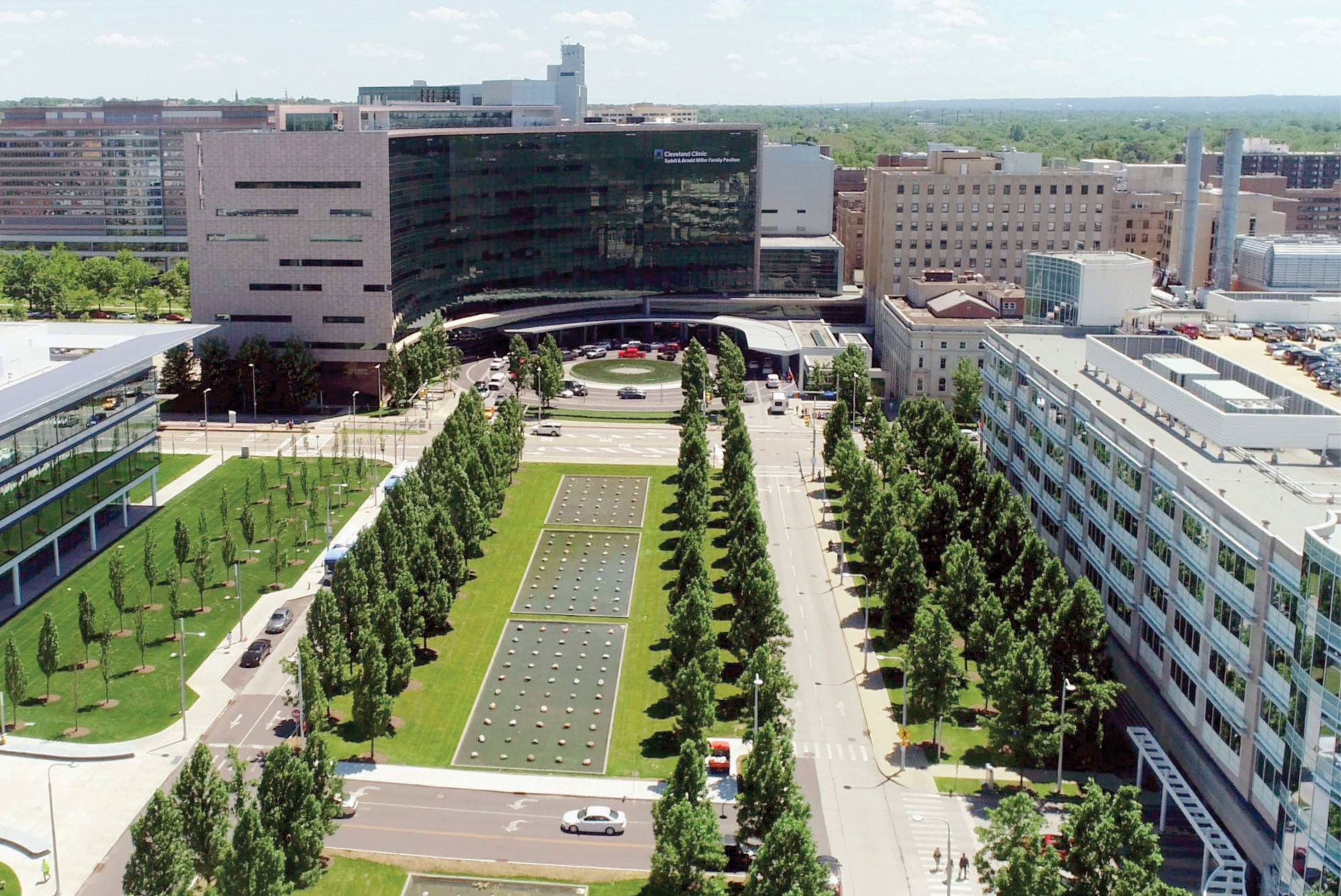
2023 Excellence in Health Care Facility Management Award winner
Winning entry
- Project: Cleveland Clinic building infrastructure upgrades.
- Location: Cleveland.
- Start date: March 2018.
- Completion date: April 2022.
- Budget: $31,535,979.
- Actual cost: $29,652,234.
Project team
- Robert Wiemels, electrical shop manager, Cleveland Clinic.
- Tony Hlavaty, high energy electrician lead foreman, Lake Erie Electric.
- Leon Rozic, owner’s representative, Concord Healthcare Development.
- Jim Senick, regional director of construction, Cleveland Clinic.
- Jerry DeCesare, facilities electrical engineer, Cleveland Clinic.
- Rocco Gallo, electrical engineer lead design principal, Karpinski Engineering.
- Frank Eddy, project manager, Lake Erie Electric.
- Eric Campbell, project executive, Whiting-Turner Contracting Company.
- Rodolfo Soto, project manager, Whiting-Turner Contracting Company.
- Marvin Echols, project manager, Whiting-Turner Contracting Company.
- Ron Knight, project superintendent, Whiting-Turner Contracting Company.
- Chad Hull, project manager, Relmec Mechanical.
- Aaron Parker, project lead pipe fitter, Relmec Mechanical.
- Monica Erikson, commissioning agent, Heapy Engineering.
- Stephanie Drenten Ferro, commissioning agent, Heapy Engineering.
- Steve Seifried, HVAC mechanical shop facilities manager, Cleveland Clinic.
Awards and recognition task force
- Matt Snow (chair)
- Eric Petrus (co-chair)
- Anthony Moiso
- Troy Ledet
- Eric Krause
- Jamey Lynn Greer
- Scott Burcroff
- Jeremy Bechtold
Such was the dilemma facing Cleveland Clinic and its H Building. Built in 1974, the H Building is a vital 500,000-square-foot structure that offers neurology, radiology and urology services. It also houses critical care units as well as a pharmacy, main cafeteria and automatic guided vehicle robot systems. The building also serves as an essential power cog across the main campus. The facilities engineering and construction team faced the challenge of modernizing and replacing the outdated electrical components without disrupting patient care or taking the crucial building offline.
“In 2018, the H Building’s transformers, generators, circuit breakers and automatic transfer switches (ATSs) were all reaching the end of their lifespan,” says Jerry DeCesare, facilities electrical engineer at Cleveland Clinic. “This situation posed a significant risk, as an outage could severely impact multiple critical equipment pieces within the building.”
Due to the obsolescence of the original infrastructure, finding compatible parts for equipment repair was challenging, with limited availability and lengthy delivery lead times. Any attempts at expedited repair work ran the risk of requiring rework or causing further damage to the equipment. Consequently, there were substantial concerns about potential electrical infrastructure failures prior to the upgrades performed on the H Building.
Replacing the power system of a legacy hospital building while ensuring continuous operations is inherently complex. In such buildings, numerous existing conditions are difficult for the design team to access, and the accuracy of existing documentation may be questionable. These uncertainties could lead to significant change orders or unexpected shutdowns, posing potential risks to patients. Every aspect of the design and construction had to align with this primary objective, emphasizing the need for meticulous planning and execution to guarantee seamless patient care throughout the upgrade process.
Award-winning project
In March 2018, the Cleveland Clinic Foundation, along with Whiting-Turner Contracting Company and Karpinski Engineering, both Cleveland-based, embarked on this endeavor. The project included significant improvements such as the creation of a main normal medium voltage system, the replacement of the main emergency electrical system and the refurbishment of the building’s four main air handlers.
Amazingly, all of this was accomplished while the facility remained operational. The upgrades substantially enhanced patient safety, system reliability and ease of maintenance. And, despite the challenges involved, including those posed by the COVID-19 pandemic, the team successfully executed the project without major disruptions to patient care.
In April 2022, their efforts were completed, and the H Building’s new electrical distribution system — a model of reliability and redundancy — is expected to last up to 40 years. What’s more, the team saved an impressive $1.9 million, equivalent to 7.5% of the total projected budget, for the upgrades. This cost savings allowed Cleveland Clinic to donate a portion of the remaining contingency funds — approximately $15,000 — to the nearby East 100th St. project, which is an innovative project that adds apartments and a grocery store to the community.
These impressive achievements helped Cleveland Clinic earn the American Society for Health Care Engineering’s (ASHE’s) 2023 Excellence in Health Care Facility Management Award, which recognizes individuals or facility management departments that implement new or innovative programs or processes to optimize the physical environment and improve patient care.
“There was strong competition for this award, yet the Cleveland Clinic Foundation stood apart from the rest with their incredibly complicated infrastructure upgrade project,” says Matt Snow, PE, MBA, FACHE, CEM, LEED AP, system vice president of support services for Louisville, Ky.-headquartered Baptist Health System of Kentucky and Southern Indiana, and chair of the ASHE awards and recognition task force that chose the winning award recipient.
“This type of project is a difficult undertaking, and it was apparent that this organization handled the project with professionalism and excellence,” Snow says. “What helped this organization stand apart was how much the health care engineering leadership team had to be involved to make this project happen. The infrastructure improvements were critically important. And we all understand how difficult it can be to get a project like this approved and executed well, considering the hospital has to continue functioning during the project.”
Improved collaboration
Recognizing that the traditional design-bid-build paradigm wouldn’t suffice to manage the project’s risks, the project team proposed implementing an integrated project delivery (IPD)/owner-controlled team project delivery model. This innovative approach allowed for a level of collaboration that matched the complexity of the tasks involved, facilitating collaboration between the design and construction teams, and resulting in accurate design and construction plans. Both the design and construction teams were actively involved from the project’s inception, working together to develop the design and construction plan.
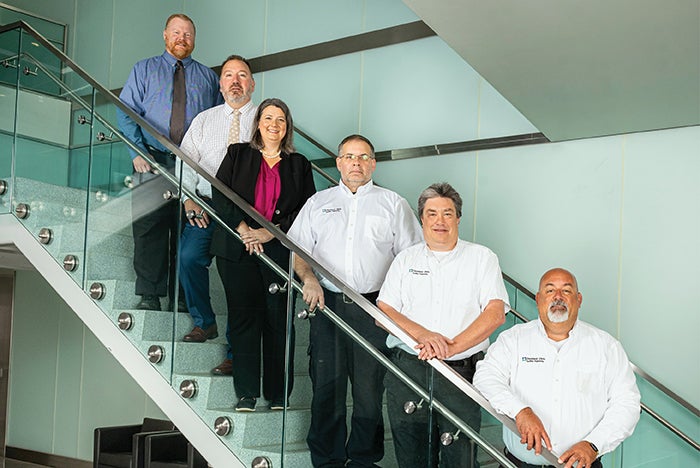
FROM LEFT: Project leadership members include Mike Jira, assistant director of facilities management; Blake Ody, director of facilities management; Danette Hauck, senior director of facilities operations and maintenance; Fred Borkey, first shift electric shop supervisor; Robert Wiemels, electrical shop manager; and Dan Ontko, third shift electric shop supervisor.
Photo courtesy of Cleveland Clinic.
“This project was important because it showcases the versatility of IPD beyond new construction or architecturally advanced projects,” says Leon Rozic, owner’s representative at Nashville, Tenn.-headquartered Concord Healthcare Development, responsible for assisting Cleveland Clinic with project management. “It demonstrates how IPD can effectively be employed in high-intensity infrastructure projects, proving its adaptability and value in diverse and complex undertakings. From the beginning, this project was a collaborative effort involving multiple parties.”
The camaraderie began when Cleveland Clinic approached Eaton, a global intelligent power management enterprise serving the electrical, mobility and aerospace markets, to discuss replacing the H Building’s transformers.
“Eaton sought input from Lake Erie Electric (Cleveland) — the electrical contractor — which recognized the need for more expertise. Subsequently, Karpinski Engineering and Whiting-Turner were invited to contribute their insights,” says Rocco Gallo, principal design lead at Karpinski Engineering. “The team fully acknowledged the inherent risks and complexities of the project, and they recognized that IPD offered the best opportunity for success. By coming together and leveraging their expertise, they ensured a robust plan and a collaborative approach to tackle the challenges of the H Building upgrade.”
The project achieved improved accuracy and enhanced constructability by involving the construction manager and contractors during the design phase. Through intensive fieldwork and design-assist support, the design team benefited from reduced guesswork and gained accurate information for sizing equipment and loads. They investigated existing conditions, minimizing unknowns and increasing overall accuracy. The electrical contractor played a vital role in assessing energized electrical systems and advising on the feasibility of the design.
Also, by utilizing advanced 3D scanning technology, the electrical contractor facilitated the creation of an accurate Revit model for the existing rooms. This meticulous approach accounted for various ceiling and floor components, whether they were retained or removed during specific phases of work. The 3D model in Revit by Autodesk Inc., San Francisco, provided precise equipment locations and conduit routing information. Contractors took advantage of the detailed Revit-coordination model to fabricate most conduits at a separate on-site location before installation. This streamlined process significantly improved efficiency and minimized on-site adjustments. Remarkably, only one conduit in the entire project needed relocation due to a minor conflict, demonstrating the exceptional accuracy and effectiveness of the 3D scanning and Revit modeling approach.
“Effective coordination between the contractor and architect ensured seamless collaboration during the construction phase,” Gallo says. “The construction manager’s input on construction logistics was invaluable in streamlining the project’s progress.”
Robust and regular communication was crucial to overall project success. Cleveland Clinic hosted town hall meetings throughout the project, providing an open forum for caregivers to ask questions and share their opinions about the timing of shutdowns. This allowed the project team to accommodate caregiver needs, aligning the timing of shutdowns with medical procedures and services. The caregivers’ support was crucial, as they actively approved the timing of shutdowns, contributing to the overall success of the project.
Electrical enhancements
In its significant overhaul, the Karpinski team designed a new main normal medium voltage system, which was absent in the previous setup. This new system included 15,000-volt (V) switchgear and transformers, drawing power from the campus electrical infrastructure. The switchgear and transformers were designed as double-ended substations, enabling maintenance on one side without disrupting power downstream. This design choice significantly reduced risks to operations and patient care, ensuring an uninterrupted power supply.
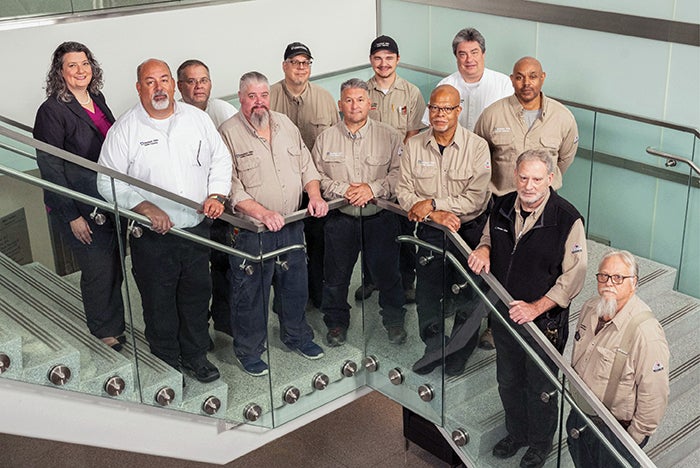
FRONT ROW, FROM LEFT: Dan Ontko, third shift electric shop supervisor; Joe Makar, first shift electrician; Bryan Dell, third shift electrician; Gary King, first shift electrician; Greg Grubb, third shift electrician; and Chris Shepherd, third shift electrician. BACK ROW, FROM LEFT: Danette Hauck, senior director of facilities operations and maintenance; Fred Borkey, first shift electric shop supervisor; Michael Brown, third shift electrician; Mike Jira Jr., intern; Robert Wiemels, electrical shop manager; and Ralph Owens, third shift electrician.
Photo courtesy of Cleveland Clinic
In addition, the main emergency electrical system was completely revamped. The team replaced the existing three 600-kilowatt (kW) generators with two new 2,000-kW generators, providing increased capacity and N+1 redundancy for added reliability. They also streamlined and replaced the existing transfer switches, opting for bypass-isolate type switches, and the number of ATSs was reduced from 21 units to 10 units. Careful attention was paid to fault current and coordination, as the replacement of old equipment with larger, new equipment could impact existing conditions. By meticulously addressing these considerations, the group ensured a seamless integration of the new electrical systems, improving overall efficiency and safety.
The team’s design ingenuity was put to the test when finding space for the new equipment. They successfully replaced six single-ended substations with two double-ended substations, all located in the same third-floor electrical room. Additionally, due to code requirements, the room had to be split into two separate rooms, each dedicated to normal and emergency power systems.
On the third floor, the substations were replaced one by one, with the remaining substations taking on the building’s electrical load during each replacement. This meticulous approach ensured a smooth transition without interrupting the power supply to critical areas.
To accommodate the new generators, double-ended substation, 15,000-V main distribution, paralleling switchgear and transfer switches, a penthouse addition was designed and constructed. The team further enhanced safety by adding a pre-action fire protection system to these rooms.
“The electrical system’s design and construction were strategically phased, spanning across 10 phases,” says Robert Wiemels, electrical shop manager for Cleveland Clinic. “This well-organized approach allowed the project to progress smoothly and efficiently, enabling the successful integration of the new electrical systems into the existing infrastructure.”
AHU upgrades
During the design phase, Cleveland Clinic decided to include an air-handling unit (AHU) refurbishment as part of the project scope. The Karpinski team took on the task of replacing sections of the building’s four main AHUs, collectively handling more than 410,000 cubic feet per minute of air. These four air handlers function as one large unit, providing inherent redundancy, and they play a crucial role in serving various essential areas, including operating rooms, a pharmacy, post-anesthesia care unit/intensive care unit spaces, patient rooms and general patient areas.
Karpinski Engineering made significant improvements to the AHUs, enhancing their functionality and efficiency. They provided new fans with N+1 redundancy, new preheat coils and new prefilters. Moreover, they allocated space for a future energy recovery coil, ensuring future sustainability. By installing a new heat exchanger pump package and converting the preheat coil from steam to hot water, they addressed existing system deficiencies and ensured a more effective operation. The team also transitioned the pneumatic AHU controls to electronic direct digital controls, upgrading the control system to enhance overall performance.
“The AHU refurbishment was carefully phased to maintain continuity of operation. At any given time, three AHUs remained operational, ensuring uninterrupted service during the upgrade process,” says Jim Senick, regional director of construction at Cleveland Clinic. “The upgrades significantly improved system resiliency and AHU controllability for Cleveland Clinic, providing anticipated operational benefits for more than 40 years. These enhancements contribute to the overall efficiency and reliability of the facility’s air-handling systems, ultimately supporting the quality of patient care and facility operations.”
The extra mile
To ensure precision in the design, the team utilized extensive design-assist support to verify existing conditions, leading to a high level of design accuracy. Live cost estimating enabled them to provide accurate estimates. Constructability was integrated into the design through joint efforts.
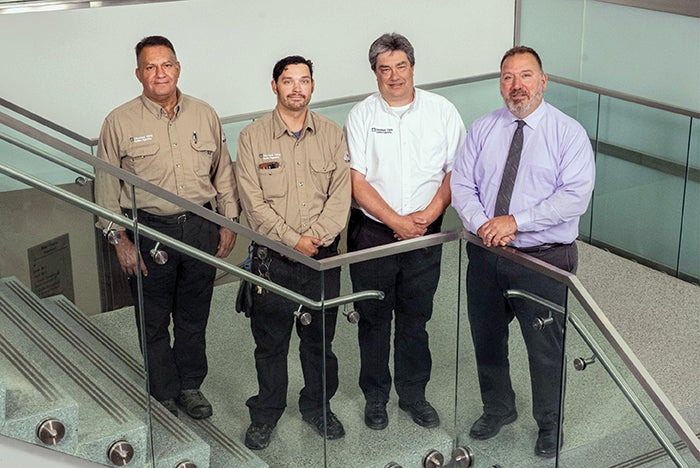
FROM LEFT: Juan Cintron, second shift electrician; Clifton Rife, first shift electrician; Robert Wiemels, electrical shop manager; and Blake Ody, director of facilities management.
Photo courtesy of Cleveland Clinic
Impressively, out of the 77 official requests for information, only nine were related to the mechanical, plumbing and fire protection scope, and none were associated with the electrical scope. This showcased the effectiveness of the IPD approach in streamlining collaboration and minimizing complications during the project’s execution.
Accurate building information modeling was achieved through the contractor’s meticulous scanning of existing electrical rooms. This allowed for the precise placement of conduits, even with existing obstacles in the rooms, and enabled the creation of prefabricated conduit bends, streamlining the installation process.
DeCesare says Eaton’s involvement from the project’s inception was crucial, too. “They provided equipment specifications, physical size, layout and a complete bill of material, which were ready for review at the project’s end, ensuring a well-prepared and efficient execution,” he says.
The project team also employed live cost estimating, which enabled them to make pre-purchases and secure significant savings on materials, equivalent to around 10% of the budgeted value. This proactive approach proved highly advantageous. Moreover, by involving the mechanical contractor during project validation, the team gained valuable insights into the actual cost of air handler construction. These real cost figures were factored into the life cycle cost analysis, leading to a more precise payback assessment.
Additionally, amid the COVID-19 lockdown, the team ingeniously navigated ways to continue construction, which significantly impacted not just the patient care team but the entire design and construction team as well. The utmost consideration was given to pandemic patients located below the construction area, ensuring their well-being was unaffected by any construction noise from above. Through noise measurements and regular communication with nurse managers, it was evident that patients remained blissfully unaware of the construction noise.
The entire team, including designers, construction managers and contractors, collaborated to devise installation methods that minimized the use of loud tools. They willingly opted for quieter tools, even if it meant the tasks took longer to complete. Some shutdowns were deliberately scheduled during the day when noise could be better tolerated. This strategic decision allowed patients to rest better at night and ensured more health care staff were available during the day to address patient concerns and maintain uninterrupted patient care activities. The squad’s resourcefulness and adaptability played a pivotal role in mitigating any disturbances to patient care during the construction phase.
“Many hospitals across the county and world have aging infrastructure that is past its expected service life. Major upgrades to an occupied hospital are difficult but can be done with proper planning and a multidisciplinary team,” says Danette Hauck, senior director of facilities operations and maintenance at Cleveland Clinic. “The key to a project like this is to work together as a team; plan, plan, plan and check your plan again; and communicate, then over-communicate.”
Wiemels says he’s humbled to be on the team receiving the ASHE 2023 Excellence in Health Care Facility Management Award. “As an electrician for over 25 years, this project was the most complex I had ever been involved with. Replacing the electrical backbone in a hospital while it continued to provide patient care was something I believe had never been attempted. It is an honor for ASHE to recognize these achievements and choose this project.”
Hauck also takes pride in the received accolade. “Being honored by our fellow peers in health care who understand facilities maintenance validates our processes and diligence while rewarding our constant drive for patient, employee and visitor safety,” she says. “We are grateful for the recognition of our electrical team and this project.”
Hybrid project delivery model helps reduce potential risks
Utilizing the integrated project delivery/owner-controlled team project delivery model led to significant risk reduction and improved outcomes for all involved in the Cleveland Clinic H Building project.
At the job’s outset, the design team developed a comprehensive risk matrix, identifying numerous potential risks and evaluating them based on probability, cost impact and schedule impact. They also devised effective strategies to mitigate these risks.
Design-assist played a crucial role in identifying and mitigating risks too, particularly in dealing with legacy buildings.
“Many existing conditions were in hard-to-access areas, and the accuracy of existing documentation was questionable,” says Frank Eddy, project manager at Lake Erie Electric, Cleveland. “By involving contractors during the design phase, the team conducted intensive field examinations to identify existing conditions and incorporate them into the design seamlessly.”
For example, the team:
- Conducted investigations on energized electrical systems and provided valuable insights on constructability.
- Identified all conduits and feeders with source, destination and conductor design to facilitate phasing design and verify existing conditions.
- Located and resolved conflicting conduits on the roof.
- Located actual splices, improving cost accuracy by reducing guesswork in electrical drawings.
- Performed thorough on-site evaluations to gain a deep understanding of the existing electrical systems and devised temporary connections to minimize disruptions during shutdowns.
- Facilitated direct coordination between the mechanical and electrical contractors and the architect, collectively taking charge of sizing vertical shafts instead of relying solely on the mechanical, electrical and plumbing design team, which helped prevent potential issues and costly change orders, safeguarding patient care.
- Implemented metered loads, enabling accurate measurement of actual electrical equipment usage and resulting in reduced replacements and appropriately sized equipment capacity, thereby saving resources and improving efficiency.
Coordination keeps building operational during upgrade
The Cleveland Clinic H Building infrastructure project placed patient care and safety as its top priority throughout its development and completion. A remarkable achievement was the ability to keep patient care areas in the H Building operational during the 100 cutovers and 48 shutdowns carried out during the project. This success was a result of meticulous planning and research by the integrated project delivery team, working in close collaboration with the clinical care teams responsible for the H Building. To foster trust and effective communication, the project team maintained transparent and consistent updates with the clinical teams, sharing progress and scope of work openly.
The scheduling of shutdowns was thoughtfully coordinated to minimize disruptions to patient care. The electrical team performed shutdowns during off-shift hours on weekends, from 6 p.m. Saturday evening to 4 a.m. Sunday morning, requiring significant overtime dedication.
Every member of the H Building infrastructure upgrades team was fully committed to maintaining the H Building’s functionality for patient care throughout the entire project.
“Our facilities electric shop worked closely with the construction team and applied best practices,” says Robert Wiemels, electrical shop manager for Cleveland Clinic. “We would provide temporary alternate power to the critical areas and essential equipment, which allowed us to reduce outages to less than 30 minutes while the cutover of the load lasted eight to 10 hours.”
Jim Senick, regional director of construction for Cleveland Clinic, says that, throughout the construction process, the crew implemented a series of meticulous checks and balances to ensure flawless execution.
“The team conducted comprehensive shutdown preparations, carefully scrutinizing each step of the sequence before its actual implementation,” he says. “This rigorous approach allowed them to verify that every step occurred in the correct order, leaving no room for errors or oversights.”
Erik J. Martin is a freelance writer based in Oak Lawn, Ill.