3 ways to maximize postmortem spaces in medical facilities
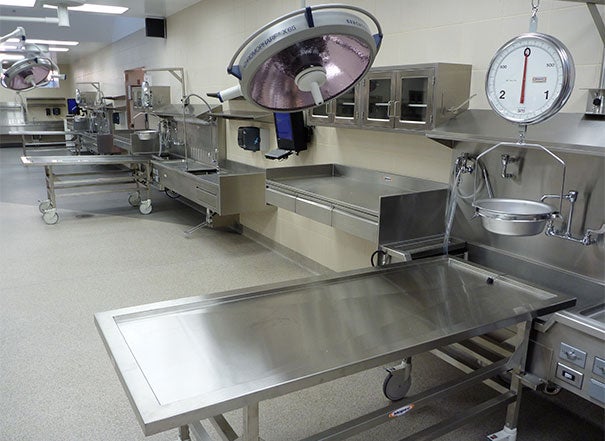
Functional workflow planning is necessary to make the most of postmortem facilities.
In medical facility new construction or renovation projects, the morgue is often considered after higher profile, revenue-producing areas, resulting in a need to efficiently design the layout of limited morgue real estate. Since usable space also can be restricted by building columns or other structural elements, optimizing morgue design and workflow can be particularly difficult.
“Some morgue customization is often required in new construction to improve design layout and function,” says Jennifer Cardettino, a partner in Linea Inc., a Boston-based, full-service architecture firm. “In renovations, customization can be even more important, particularly in older buildings, where space restrictions can lead to challenging floor plans and access.”
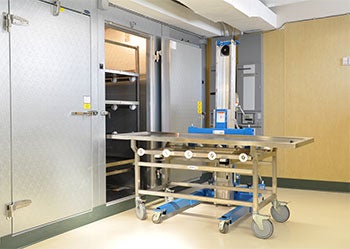
Refrigeration should be tailored to the layout and needs of the facility.
Planning for functional workflow within the morgue and throughout the facility is vital for architects and medical equipment planners. Safe, effective transport of a patient’s remains from the medical facility bed to morgue refrigeration and sometimes to a viewing room and autopsy room, is critical. Yet, most architects have no experience with designing morgues and few will design more than one or two in their careers.
Nevertheless, morgue design must be safely integrated with postmortem storage, transport and processing. The design must also accommodate medical equipment as a complementary system. This is why it is important for architects to partner with medical equipment planners and other resources.
“We do a lot of work in hospitals and laboratories, but do not design morgues and autopsy rooms on a daily basis,” says Cardettino. “So we find it helpful to partner with equipment providers with morgue-specific expertise.”
Fortunately, architects and medical equipment planners today are receiving expert design guidance, along with necessary equipment modification or customization, from a new breed of medical equipment providers. Partnering with vendors to customize products such as refrigeration, autopsy carts or cadaver carriers can improve architectural design, safety and workflow, while reducing the project budget.
Customization is key
At the heart of hospital morgue design is the goal of safely maximizing refrigerated cadaver storage while allowing flexible, productive workflow.
When the morgue is frequently allocated leftover facility space, the question becomes: How can architects and equipment planners fit everything required — including the refrigeration system, autopsy tables, lifts, racks, trays and tools — so it can be efficiently utilized?
The key to making this work is customizing the postmortem refrigeration unit and choosing complementary morgue equipment to develop a total-systems approach.
For instance, manufacturers that specialize in custom postmortem medical equipment solutions for hospitals, morgues and universities offer a range of refrigeration configurations and options such as telescoping, conveyor, walk-in, forensic lab and cadaver lockers that enhance workflow and safety.
Refrigeration units should be configured according to facility needs, with additional considerations that include safety and durability. To conserve space for individual cadaver refrigeration, small door end-opening modular refrigeration units can be used with telescoping or conveyor tray storage. Walk-in refrigeration systems offer the most flexibility in design. Racks, available with up to five tiers, are used to maximize efficient storage within the unit. Cantilever, storage and mortuary racks should be manufactured to complement the walk-in unit design specifications.
To maximize safe storage, the refrigeration units, racks and trays need to accommodate a wide range of body sizes from pediatric to bariatric. For added safety, the refrigeration units should be coated with a special antibacterial material that inhibits germ growth. Many units can open to 180 degrees, offer an optional internal safety release, and come with magnetic seals and heated jambs to enhance worker safety while preserving the cadavers. High-quality refrigeration systems are constructed with stainless steel, urethane foam and cam-lock fasteners to ensure prolonged use.
When Dutchess County, N.Y., outgrew its old morgue, it built a new stand-alone facility. Medical examiners needed a customized solution that could increase capacity, while improving cadaver-handling processes and efficiency. The Dutchess County medical examiner office partnered with Mopec to customize a refrigeration unit that could accommodate up to 12 cadavers.
“The new morgue was designed to increase our workload and improve workflow,” says Dennis Chute, M.D., Dutchess County chief medical examiner. “The office wanted simple access for bringing the remains from outside into the walk-in cooler and then into the morgue suite itself.”
To achieve the design objectives, the county installed a custom stainless steel cooler with a dual-door design that fit within the desired architectural footprint.
“Now remains are brought from outside into a reception area, then through a door into the cooler,” explains Dutchess County Deputy Chief Medical Examiner Kia Newman, M.D. “When we’re ready for autopsy, there’s direct access to bring the remains from the cooler into the morgue through the second door.”
Keeping things flexible
While refrigeration is the main concern when designing and building morgue facilities, the refrigeration unit’s compatibility with transport carriers, lifts, trays and racks also is fundamental.
Due to the obesity epidemic, many facilities have no-lift policies for safety and are even moving toward no-push policies. Consequently, the proper size cadaver lifts and carts must be capable of ergonomic lifting, tilting and movement for safe loading, transport and unloading. Proper-sized trays and racks must also be available.
For the medical examiner office in Macomb County, Mich., postmortem cart customization was required to improve workflow of its new morgue. Daniel Spitz, M.D., the county’s chief medical examiner, wanted to eliminate the hassle of having to maneuver a body from one cart to the next for X-rays during the autopsy process, so Mopec equipped each movable cart with a specially designed fiberglass top. Since there is no longer a need to put X-ray film beneath the body, Spitz can perform an X-ray through the body on the cart with his equipment. The dull, muted-gray surface on the fiberglass top is also lighter, easier to clean and excellent for photography.
To further increase workflow efficiencies, Spitz requested a procedure that allowed a body to remain on a single cart for its entire duration at the morgue, eliminating additional transportation and handling. Cadavers are now brought into the rear of the morgue, placed on a cart, wheeled onto the scale to be weighed, brought into the autopsy room for examination and wheeled back to the cooler until funeral home personnel retrieve the body.
Ventilation is critical to safety
When autopsy or embalming is required, the cadaver is moved out of refrigeration and into a work area where the autopsy table, trays, carts and sinks must be compatible for proper transfer and processing.
As part of a morgue renovation for a hospital on the East Coast, customization was required when architectural firm Linea 5 designed a full autopsy room and pathology lab space.
“One of the rooms had a customized teaching lab requiring stainless steel counter systems, integrated tables with downdraft ventilation and ventilated storage cabinets,” says Cardettino. “The most efficient way of doing this was to have a completely customized layout, so we worked with Mopec to create one that worked.”
Customizing autopsy or embalming equipment can be critical for safety. Now that the preservative formalin is recognized as a carcinogen, control over inhaling its vapors is necessary around autopsy or embalming equipment. Proper ventilation or air recirculation can be built into equipment or customized to suit facility airflow management needs.
For instance, understanding and customizing recirculating autopsy tables can be essential to architects and equipment planners.
“Without ventilation access, project cost can double or triple if ventilation has to be brought to the unit,” says Miguel Bermeo, CEO of Scimedico, a medical equipment distributor. “If the autopsy table is in the middle of a room, how do you ventilate? Where do you get the air from and how do you get it to the unit?”
Bermeo says that when it comes to looking for “custom recirculation or ventilation design, such as backdraft, downdraft, or even front ventilation that effectively creates an air pocket that keeps fumes away from the worker,” it’s important to work with trusted experts in the industry.
Del Williams is a technical writer based in Torrance, Calif. He writes about business, technology, health and educational issues.