Effective safety features begin with facility design
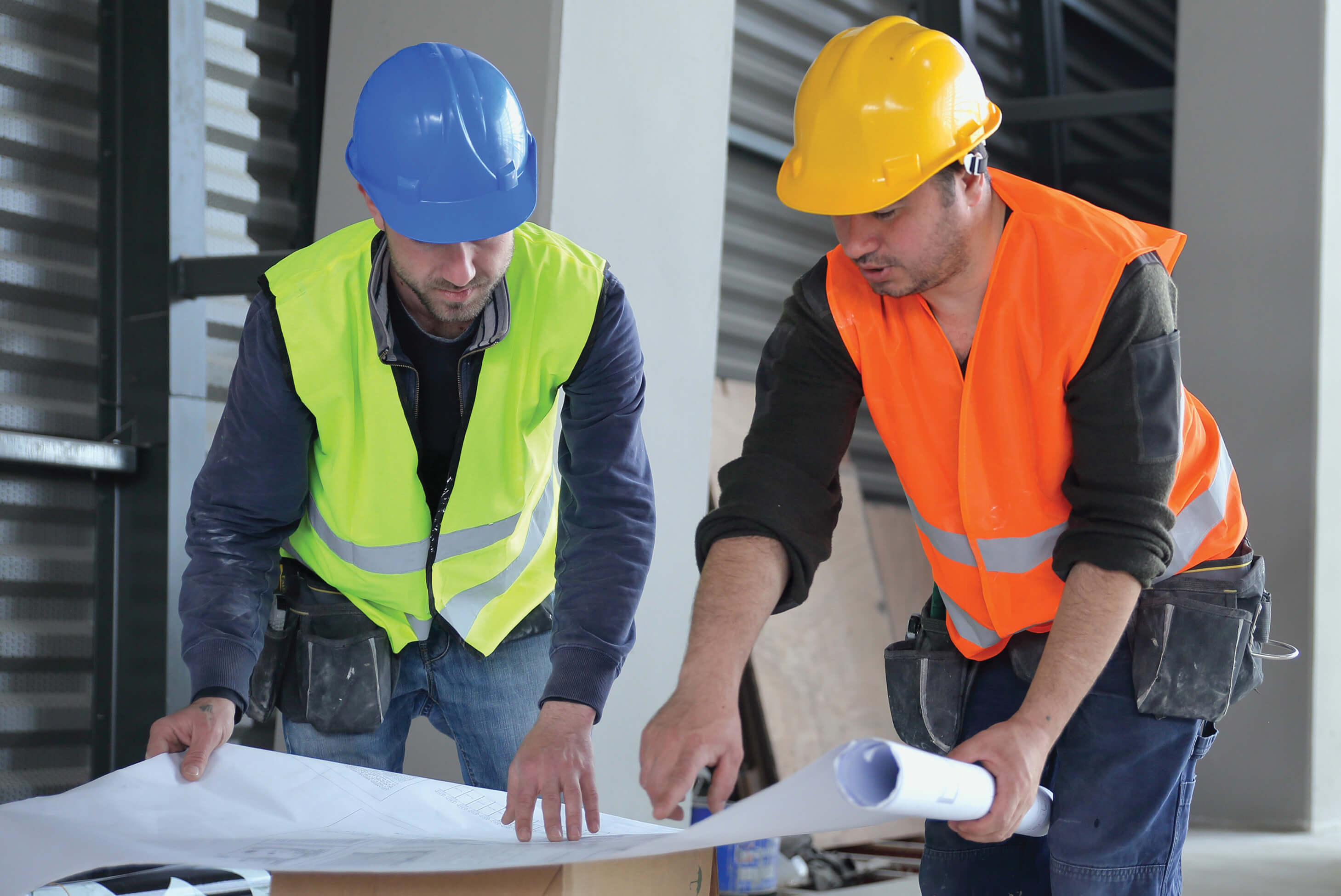
Steps implemented during the planning, design and construction process can help maintain effective fire and smoke barriers in health care facilities.
Image by Getty Images
It is not uncommon for a health care organization to receive one or more findings for a fire or smoke barrier that is not in compliance with the applicable code requirements. Many of the findings are due to an unprotected penetration in the barrier.
While some of these findings are due to penetrations that occurred post-occupancy, some of them are due to conditions that existed from the initial date of occupancy and others are the result of inadequacies within the construction documents.
However, there are steps that can be implemented during the planning, design and construction process and after occupancy to maintain effective fire and smoke barriers in health care facilities.
The design process
The building codes and National Fire Protect Association’s NFPA 101®, Life Safety Code®, prescribe the barriers that are required to provide a minimum level of protection to the people in a health care occupancy.
Construction documents will identify the assemblies that are required to have a fire-resistance rating or to serve as smoke barriers. The construction documents should also provide the details for how these assemblies are to be constructed. In addition, the details will reference the tested assembly that is further detailed in a directory of the tested assemblies.
Plan reviews are generally performed by various authorities having jurisdiction (AHJs) to determine general compliance with the applicable codes and standards. What can go wrong at this phase?
Assuming the construction documents comply with the applicable codes, one source of potential problems is the lack of consideration of the penetrations of the rated assemblies. While 3D models have resulted in fewer penetrations being overlooked, there remain instances in which the means of protecting the penetrations have not been detailed by the design team. Instead, the means to protect the openings is left to one or more contractors.
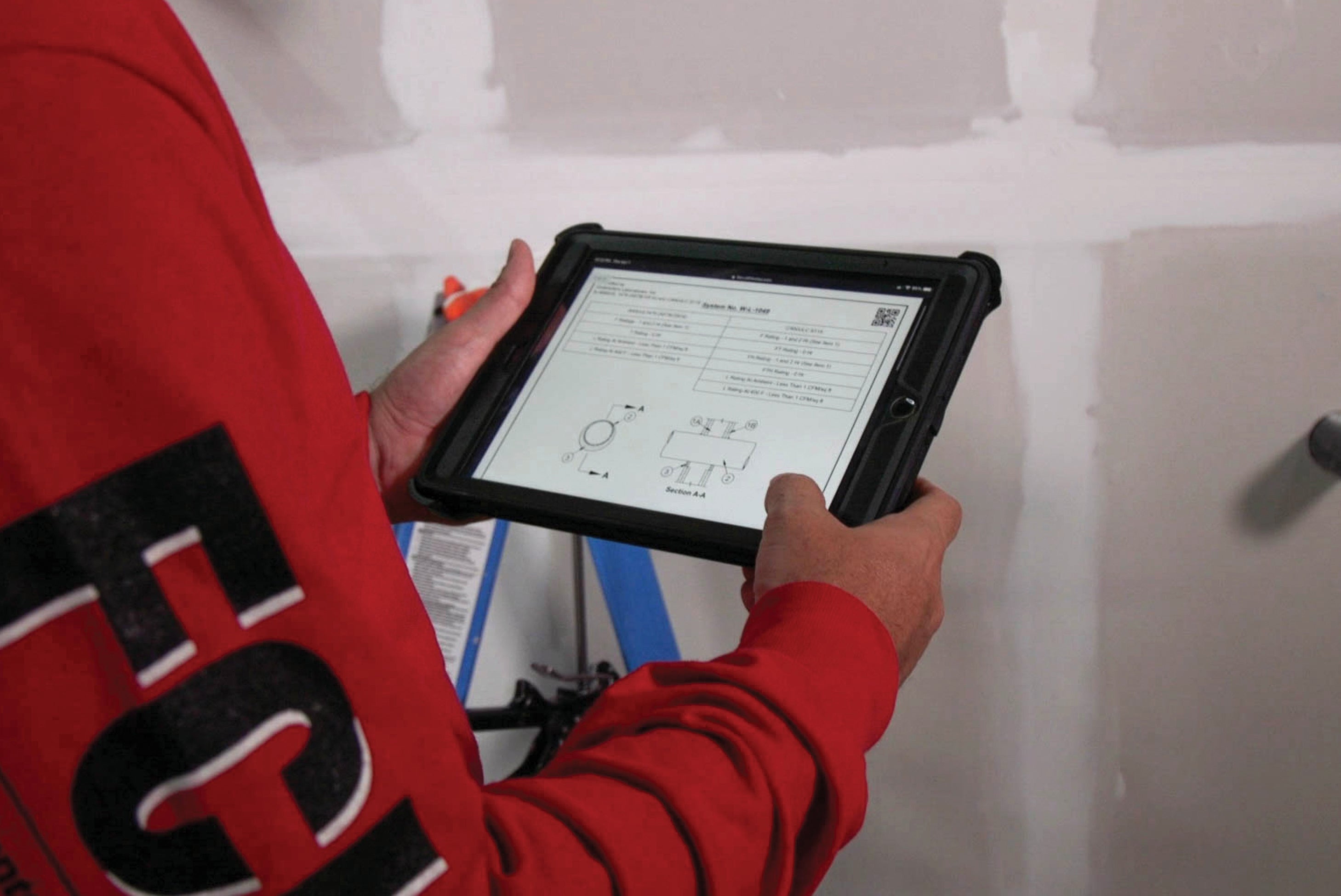
It is critical that the firestop contractor knows and is able to properly select the systems to be used.
Image courtesy of the Firestop Contractors International Association
Because there are certain penetrating items not identified during the design phase or changes are made during construction, details for each penetration are often not included in the construction documents. Generic details might be provided identifying what is expected in the way of tested systems to protect the annular space around penetration items.
Another problem is when firestopping and protection of joints is assigned to contractors who install the penetrating items. These contractors understand the primary discipline or trade, but firestopping is secondary, and potentially incorrect systems may be used.
The lack of knowledge by these contractors, and lack of detailed consideration, could also result in unnecessary penetrations of rated assemblies and penetrations that are not consistent with listed systems, which results in an increased use of engineering judgements (EJs). EJs typically occur when the contractor has determined that a listed system does not exist for the specific penetration and manufacturers are requested to provide an EJ using an alternative, non-tested approach to protect the penetration.
Recognizing that the codes are a minimum, some design professionals make the choice to provide more fire and smoke barriers than are required. Generally speaking, one cannot argue with providing a level of protection higher than the minimum required by the code. However, this should be performed only after consulting the health care organization.
Providing additional fire and smoke barriers will result in increased maintenance cost to the facility, so they should only be provided based upon an appropriate cost-benefit analysis. As such, many health care organizations go through a process of decommissioning the unnecessary barriers to reduce the cost of inspection and maintenance.
It should be noted that some codes, such as the International Code Council’s (ICC’s) International Existing Building Code, require the health care organization to obtain a building permit to decommission rated assemblies even if there is no construction involved. The intent of this requirement is to provide oversight by a regulatory agency to verify that the barriers truly are not required by the applicable codes.
Building correctly
Some design teams or health care organizations require that all firestop and joint systems be installed by a contractor who specializes in such systems. In other instances, the various trades who install the penetrating item are responsible for installing the firestop system to protect the penetration of the fire or smoke barrier.
Regardless of which option is chosen, it is critical that the contractor knows and is able to properly select the systems to be used. In addition, the installing contractor needs to know the material installation in accordance with the listing and the manufacturer’s instructions.
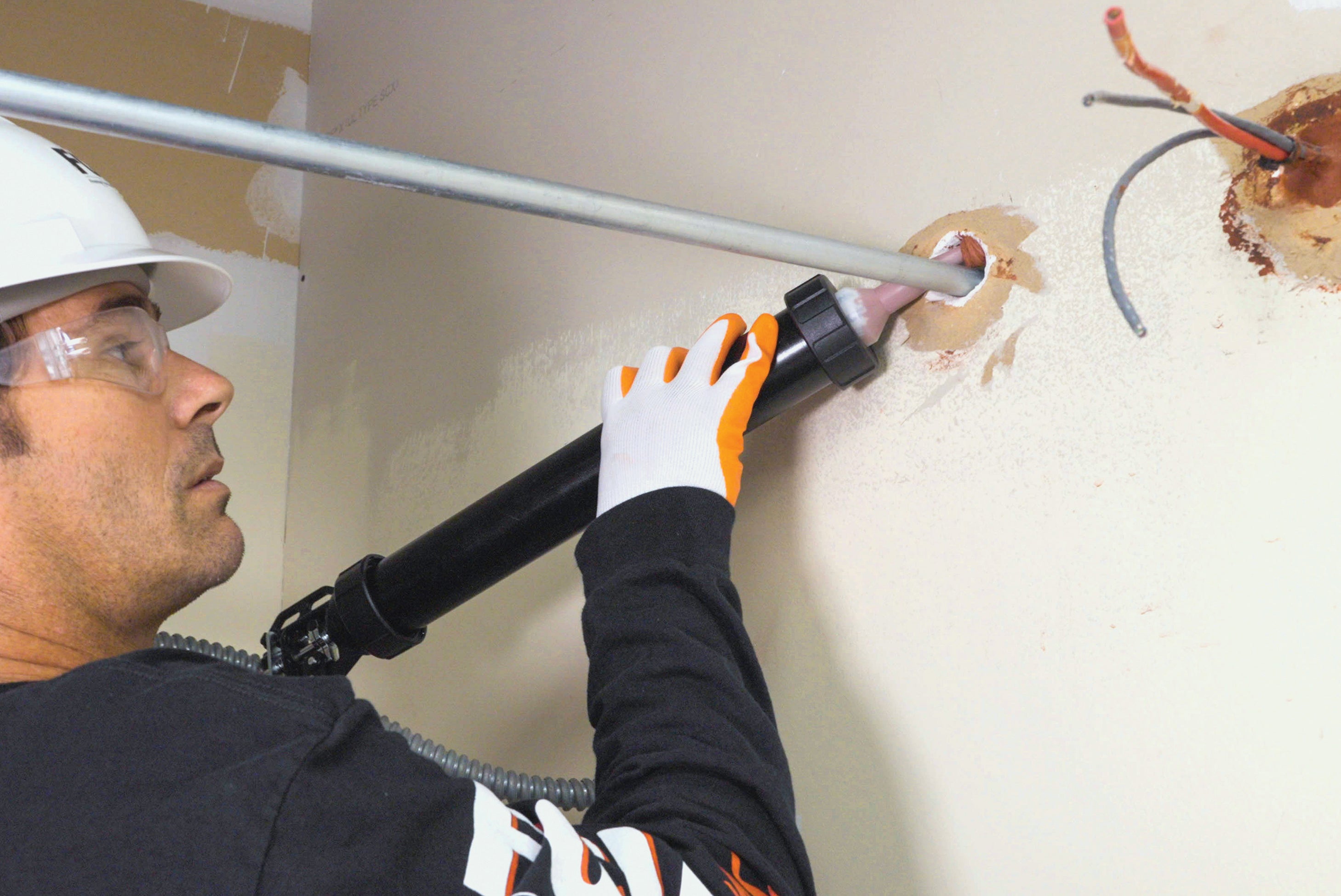
Firestop systems must be installed in accordance with the listing and manufacturer’s instructions.
Image courtesy of the Firestop Contractors International Association
Design professionals or health care organizations can include qualifications for firestop contractors in the project specifications. Those qualifications might include training by the manufacturer and participation in one of the contractor approval programs such as FM Approvals or UL, which were developed in collaboration with the Firestop Contractors International Association (FCIA). In addition, the American Society for Health Care Engineering’s Certified Healthcare Constructor and Certified Health Care Physical Environment Worker programs also should be considered.
The applicable codes do not currently contain firestop contractor qualifications or training by the manufacturers, partly because code officials do not believe it is their responsibility to regulate contractor qualifications. However, design professionals and health care organizations can, and often do, require and verify the qualifications of the contractors performing work on their projects.
Another approach to making sure that firestop and joint systems are installed properly is to require special inspections by an independent third party. Special inspections for firestop and joint systems are now required for most buildings containing a health care occupancy by the ICC’s International Building Code (IBC).
Special inspections should be conducted in accordance with ASTM E2174, Standard Practice for On-Site Inspection of Installed Firestop Systems, or ASTM E2393, Standard Practice for On-Site Inspection of Installed Fire Resistive Joint Systems and Perimeter Fire Barriers. These standards require the special inspector to verify that firestop and joint systems are installed properly, either by witnessing the installation or by a detailed inspection of a percentage of systems installed.
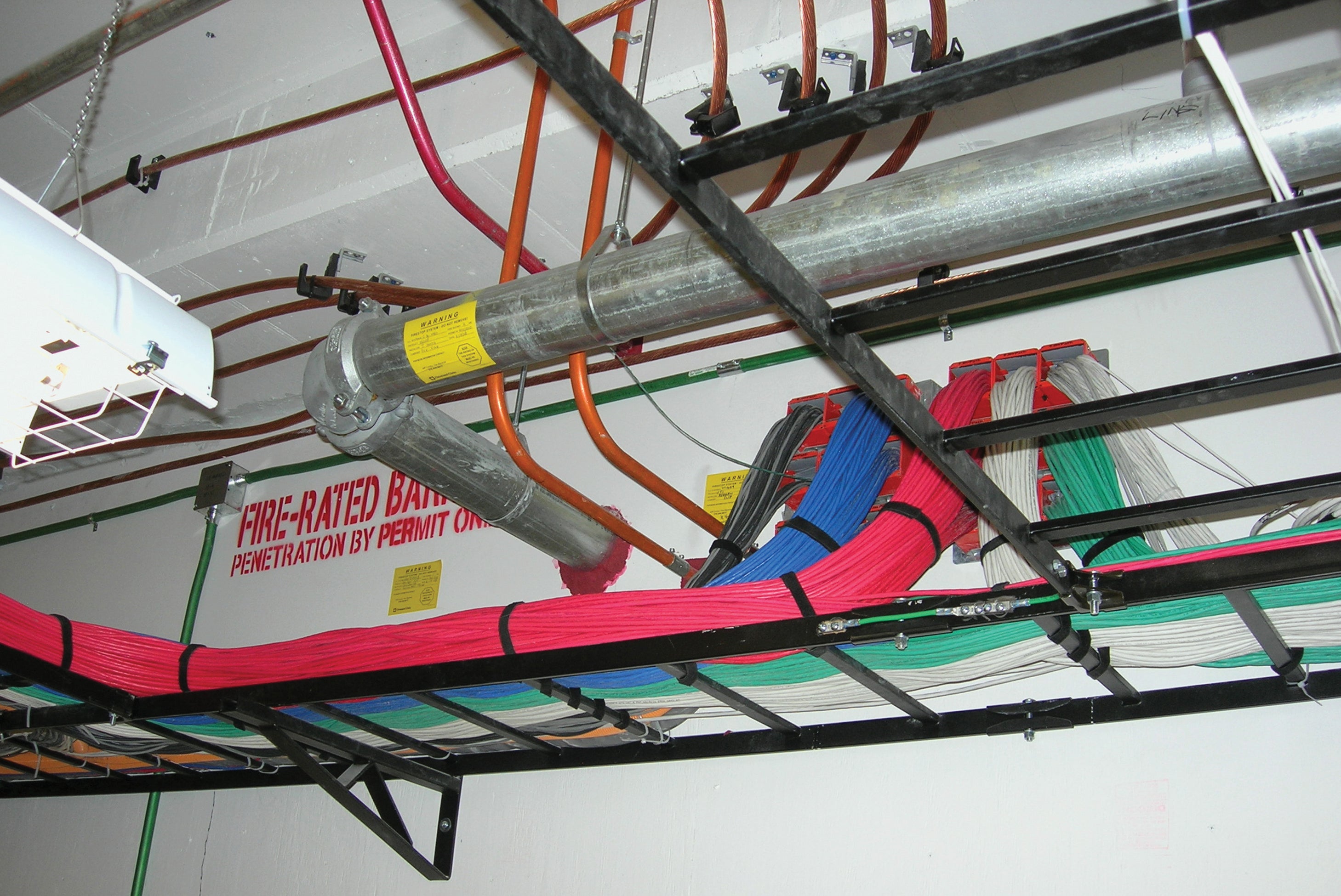
Fire barrier and firestop systems should be clearly identified.
Image courtesy of the author
Another approach that will help health care organizations is to require that the installed systems are identified in the vicinity of the penetrating item or joint. The identification of the systems installed facilitates the special inspection process, or any quality-assurance program verifying that proper systems have been used. This also provides the facility with a means by which the proper inspection and maintenance procedures can be identified.
Manufacturers include in the installation instructions recommendations for how to repair firestop and joint systems. Again, such identification of the system used is not required by the codes applicable to health care facilities but can help facilitate an effective barrier management system.
Existing buildings
New projects are constantly being undertaken in existing health care facilities. In some instances, a design team is involved, and the recommendations discussed earlier in this article would all be applicable to those projects as well.
However, some projects do not require building permits or design professionals. Rather, they are undertaken by internal staff. Facilities need to consider the same issues for those projects, including:
Who decides what assemblies are to be penetrated?
Do facilities personnel know which assemblies are required to have a fire resistance rating or be smoke barriers?
- Who decides which listed systems are to be used for the new penetrations?
- What are the qualifications of the personnel who are installing the firestop system?
- Who oversees the installation of the firestop system to verify that the system has been properly installed?
- Is the installed system identified so that facilities personnel in the future will know what system was used?
One way to make sure that facility personnel can identify fire and smoke barriers is to identify the assembly, typically above the finished ceiling, indicating that the assembly is a fire barrier or smoke barrier. While not required by the 2012 edition of NFPA 101, it is required by the IBC and newer editions of NFPA 101.
Another tool for many health care facilities is accurate life safety drawings that indicate the location and rating of fire and smoke barriers. Whereas the ICC’s International Fire Code and NFPA 1, Fire Code, require periodic inspections of fire and smoke barriers, even in buildings that are not a health care occupancy, it is beneficial to maintain similar drawings or at least an inventory of such assemblies.
Unfortunately, too many health care organizations have to spend significant funds to correct improper installations of firestop and joint systems as they are cited as findings during licensure, certification and accreditation surveys. In some cases, these repairs may not be necessary, but they provide a level of assurance that the facility is in compliance.
For example, NFPA 101 does not require existing, approved penetrations and joint systems to be listed systems. However, there are two considerations with that statement.
First, how does one document that the various AHJs approved that particular method of protecting a penetration or joint? The fact that there are no prior findings does not, in and of itself, demonstrate approval by any AHJ. Second, if the system is not listed, even if it has been approved, how does one determine the level of protection provided by the material that has been installed in the annular space or joint? As such, and at significant cost to the facility, many health care organizations have undertaken detailed firestop evaluation programs to document the condition of each penetration.
The only way to avoid the cost of such inspections needing to be performed in the future is to make sure that what was installed is an acceptable method of protecting the penetration or joint. Once this has been accomplished for either a new or existing building, the health care organization needs to implement a proper program to make sure that all future construction activities result in using proper systems.
Such barrier management programs are often referred to as an above-ceiling permit program, which generally requires that anyone doing work above a ceiling obtain a permit from the facilities management department.
Some effective ways to make sure that such permits are obtained is to require the permit to be on display when work is being performed, issue colored arm bands to personnel authorized to work on a specific project above the ceiling, or identify the ladders that are being used when a permit is issued.
Such steps allow anyone in the facility, including nursing staff, to quickly identify if the person has obtained the appropriate permits. As infection control considerations have become more prevalent, above-ceiling permit programs have also increased in popularity. (For more on above-ceiling programs, see the article "Protecting patient spaces when working overhead" in this issue.)
Facilities management should use such a program as a means of educating the personnel working on the project. The life safety drawings should be reviewed to identify all fire and smoke barriers that are within the work area. The items that will be penetrating such barriers should be identified as well as the size of the hole that will be created.
Documentation should be provided to verify that listed systems are being installed to protect the openings and that the personnel doing the work are familiar with the listings and installation instructions for such systems. If the facility has a requirement that the system protecting penetrations be identified, personnel should be aware of such a requirement.
Finally, before the ceiling is restored to its normal condition, someone should inspect the work that was performed to make sure it complies with the applicable codes and the requirements of the health care organization. Not all of this work is performed by outside personnel. It is not uncommon for facilities personnel to identify their information technology department as a common source of unknown penetrations of fire and smoke barriers.
Increased commitment
Historically, data from the Centers for Medicare & Medicaid Services and the accrediting organizations have identified findings associated with improper fire and smoke barriers as one of the top 10 findings related to building safety. In more recent years, those standards or elements of performance have often just missed the list of top 10 findings.
While this could be the result of increased findings associated with other standards or elements of performance, such as ligature risk, one would also hope that it demonstrates an increased commitment by many facilities to an effective barrier management program.
To reduce the frequency of such findings, ASHE, FCIA, UL and The Joint Commission sponsored barrier management education programs to ASHE affiliated chapters. Handouts from some of the programs can be accessed on FCIA’s website. In addition, ASHE recorded some of the programs that can be viewed on demand.
While there may be some increased cost to making sure the initial and ongoing construction are in compliance with the applicable codes, experience has clearly demonstrated that making sure all new work is accomplished correctly will result in a reduced total cost of ownership. Correcting the errors made during construction activities will always be more expensive and more disruptive to the operation of a facility as compared to making sure it is done correctly initially.
Common firestopping questions
The following two questions are often asked as concerns are identified with existing firestopping. The first deals with remediation of a defect, and the second deals with an improper determination that the existing firestopping was inadequate:
Q: We have been told that the thickness of the sealant installed in our building is inadequate. Can we just add more sealant, or do we need to remove the existing system and install a new system?
A: This question demonstrates the importance of knowing what systems are installed in your facility. The easy answer is that one should consult the manufacturer’s instructions or the manufacturer directly for the proper answer to the question. However, it should also be noted that one needs to know the material that was installed, because if one is allowed to add material, it must be the same material as was originally installed. Second, if the thickness is not correct, are you sure that other components of the system are properly installed? For example, if a packing material is part of the listed system, has the packing material been installed in accordance with the manufacturer’s instructions? One then needs to refer to the manufacturer’s product data sheet for the installation instructions. For example, in addition to a material thickness, the instructions may require that the product be “flush with the wall.” Can additional material be added such that this installation criteria is met? If it is not a new installation, there may also be concerns regarding cleanliness or oxidation that could lead to poor adhesion between the existing and new material. In summary, the short answer is remove and replace, but the manufacturer may provide you with other guidance on a case-by-case basis.
Q: A special inspector indicated that all existing systems needed to be removed and replaced because the thickness was a half inch and not five-eighths of an inch for work that was done several months ago. Was the special inspector correct?
A: It is possible that the half-inch thickness of a cured system may be acceptable. The thickness shown in the listing is based upon a wet thickness. As the sealant cures, it may be susceptible to shrinkage. The manufacturer can provide guidance on what the actual thickness should be once the sealant has cured. This happened on a hospital construction project, resulting in significant cost overruns and a delayed occupancy when most of the existing systems were properly installed.
William E. Koffel, PE, FSFPE, SASHE, is senior director for special projects at Koffel Associates, Columbia, Md. He is active in the development process of the industry’s governing codes, standards and design guidelines including ICC, NFPA, UL and Society of Fire Protection Engineers. He can be contacted at wkoffel@koffel.com.