Protecting patient spaces when working overhead
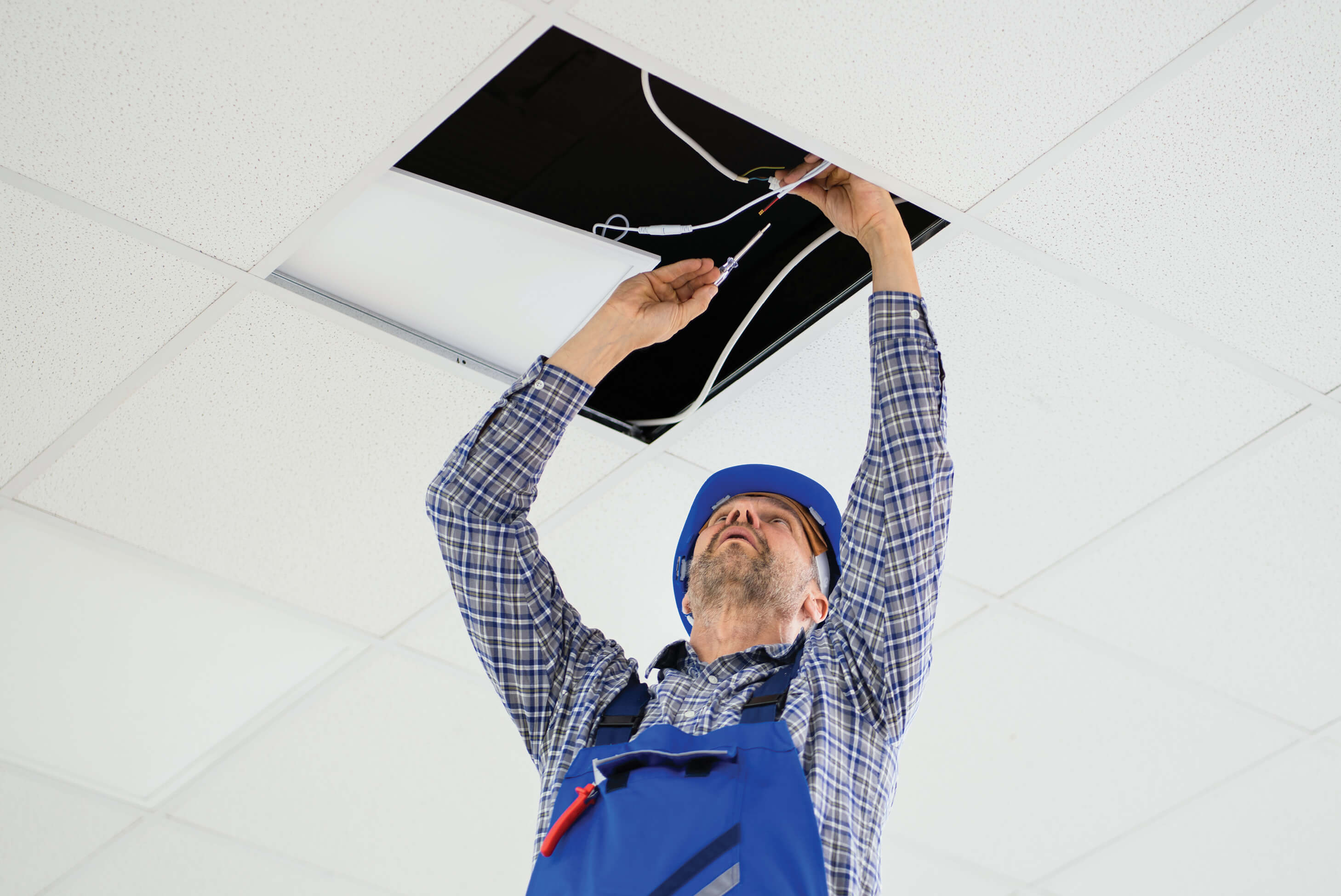
Facilities professionals must be able to access the utilities and wiring routed above the finished ceiling.
Image by Getty Images
To properly maintain the health care physical environment, facilities professionals must be able to access the utilities and wiring routed above the finished ceiling. However, this may disturb dust and debris located above the ceiling. While this may not impact most individuals, it can be a danger to many patients, especially those who are immunocompromised.
Patients with immune system issues and those undergoing organ and stem cell transplants require carefully monitored environments to prevent infections. Because the environment of care is especially vulnerable, a greater level of protection and separation is needed between construction and renovation activities.
Resources
When work is performed above the ceiling, there is an increased risk to patients contracting a health care-associated infection, which could affect the organization’s financial bottom line as well as harm its public image. The challenge is to be able to determine the increased risk.
One of the major modifications to the American Society for Health Care Engineering’s (ASHE’s) Infection Control Risk Assessment (ICRA) tool, ASHE ICRA 2.0™, is a standing-order process. Routine work above the ceiling should be evaluated using the ASHE ICRA 2.0 standing-order process to determine mitigation strategies to help reduce or eliminate the risk.
Standing practices
Fortunately, health care organizations have learned much about how to prevent these hazards and minimize the risks in the physical environment. Codes and standards require an organization to carefully manage its environment during demolition, renovation, construction and routine above-ceiling inspections.
By partnering with infection prevention (IP) professionals to create standing orders through the ASHE ICRA 2.0 process, practices can be developed for permit-required, containment-required or, possibly, no-restriction workspaces that front-line staff can reference before performing any work above the ceiling.
Moreover, establishing basic guidelines with IP of actions that can be taken above the ceiling during an emergency, such as closing an isolation valve to stop an area from flooding from a broken water line, can be developed and agreed upon for those rare occasions when an emergency response is needed above the finished ceiling. Additionally, facilities managers can incorporate a process in their computerized maintenance management system to create a corrective work order once an issue is identified that cannot be corrected at the time of discovery.
Facilities have always had a focus on above-ceiling penetrations related to fire- and smoke-rated walls, but what about the remaining ceiling space that is typically not inspected by a regulatory authority? As technicians and trade staff work on building components above the ceiling, they also should be encouraged to perform an inspection of the ceiling space.
Proper training and understanding of the culture of a healing environment is imperative for staff and contractors when performing any work in and around a patient care environment. Having an established above-ceiling permit policy and procedure will help to provide oversight for work that has to be performed above the finished ceiling.
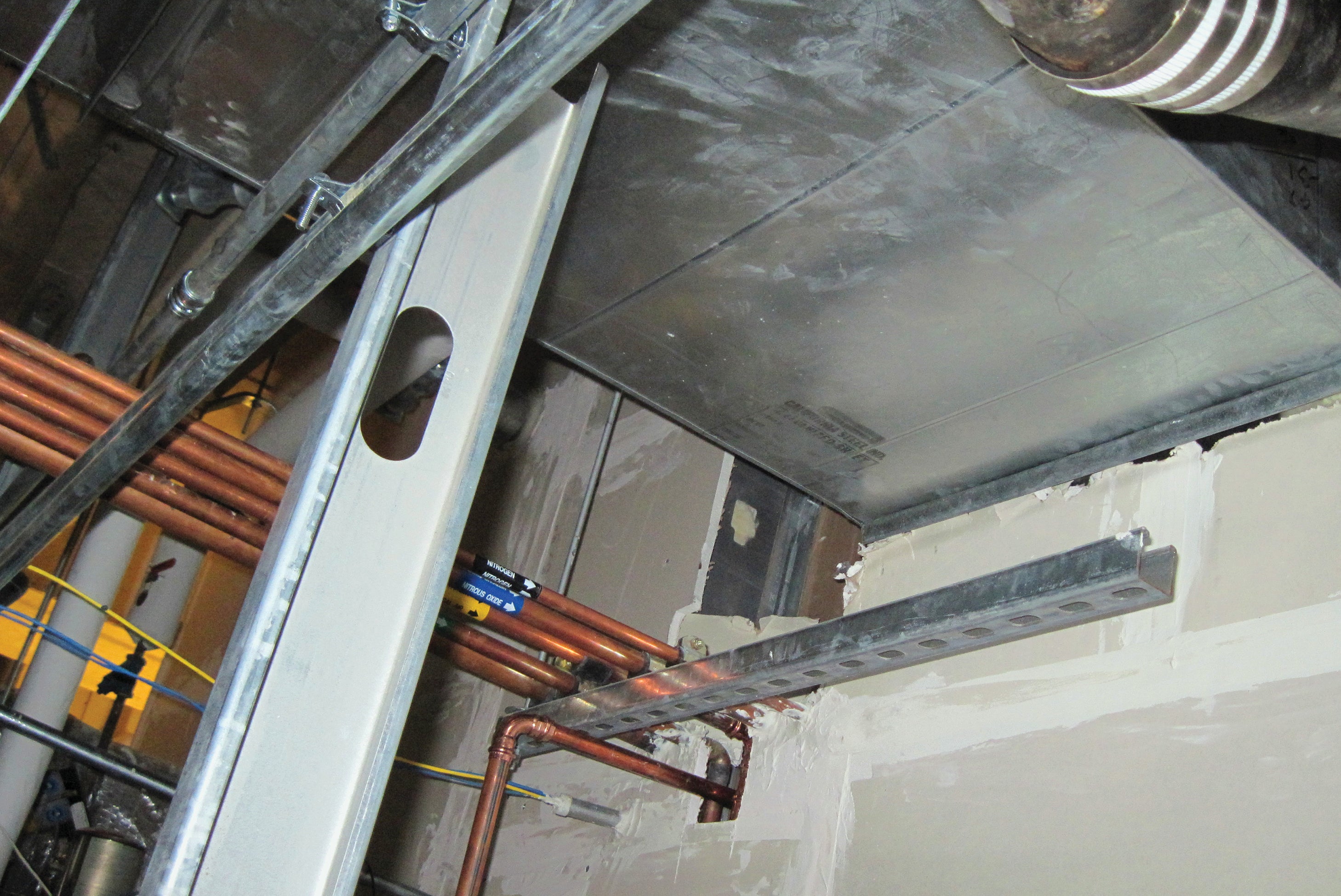
A 1-hour wall penetration and improperly supported piping trapeze.
Image courtesy of the author
Another issue that must be addressed is the integrity of the finished ceiling. Ceilings are commonly used as a smoke barrier and, as such, special attention must be given to gaps and penetrations that must be sealed to prevent the passage of smoke. Conduit or piping that passes through the ceiling plane is typically difficult to seal to prevent passage of smoke. Access panels must also be properly secured to minimize passage of smoke in monolithic walls and ceilings.
The facilities staff is the best resource to identify issues with ceiling tiles. If a ceiling tile is damaged or stained, that alone is a good indicator that something is happening above the ceiling. Staff should investigate exactly how it got damaged. Perhaps work was performed by a vendor and the facilities staff was unaware, or perhaps the tile was damaged by staff and not reported or replaced.
A stained ceiling tile is another indicator of something happening above the ceiling. Many infrastructure systems exist above the ceiling, and identifying what or where might be the cause of a leak can be difficult. A leak from the floor above, uninsulated piping, cracked or broken drain piping, HVAC ductwork, fire sprinkler piping, hot water reheat lines and steam piping are just a few of the possible sources of a leak.
Water travels to the point of least resistance or lowest point before becoming a hazard. Finding the origination point of a leak can be difficult and time-consuming for facilities staff. Yet, wet ceiling tiles or drywall will create an environment favorable for bacterial growth that has the potential to affect the physical environment.
Another common finding is anything resting on or supported by fire sprinkler piping. In older facilities, it is not uncommon to find all-thread supporting the piping trapeze and sprinkler piping. While it may be impractical to change this installation and support sprinkler piping separately, an assessment should be performed to identify the location and the risk it may present to the building and systems.
Open conduit and junction boxes are not only a potential electrical shock hazard, but also may create a way for smoke to travel. All penetrations in electrical junction boxes, such as open knockouts, must be sealed to prevent electrical shorts and contain arc flashes within the enclosure. Automatic doors also present a unique hazard above ceilings because of fire-alarm wiring, low-voltage control wiring, security wiring and power wiring, all contained within a small footprint and interfaced.
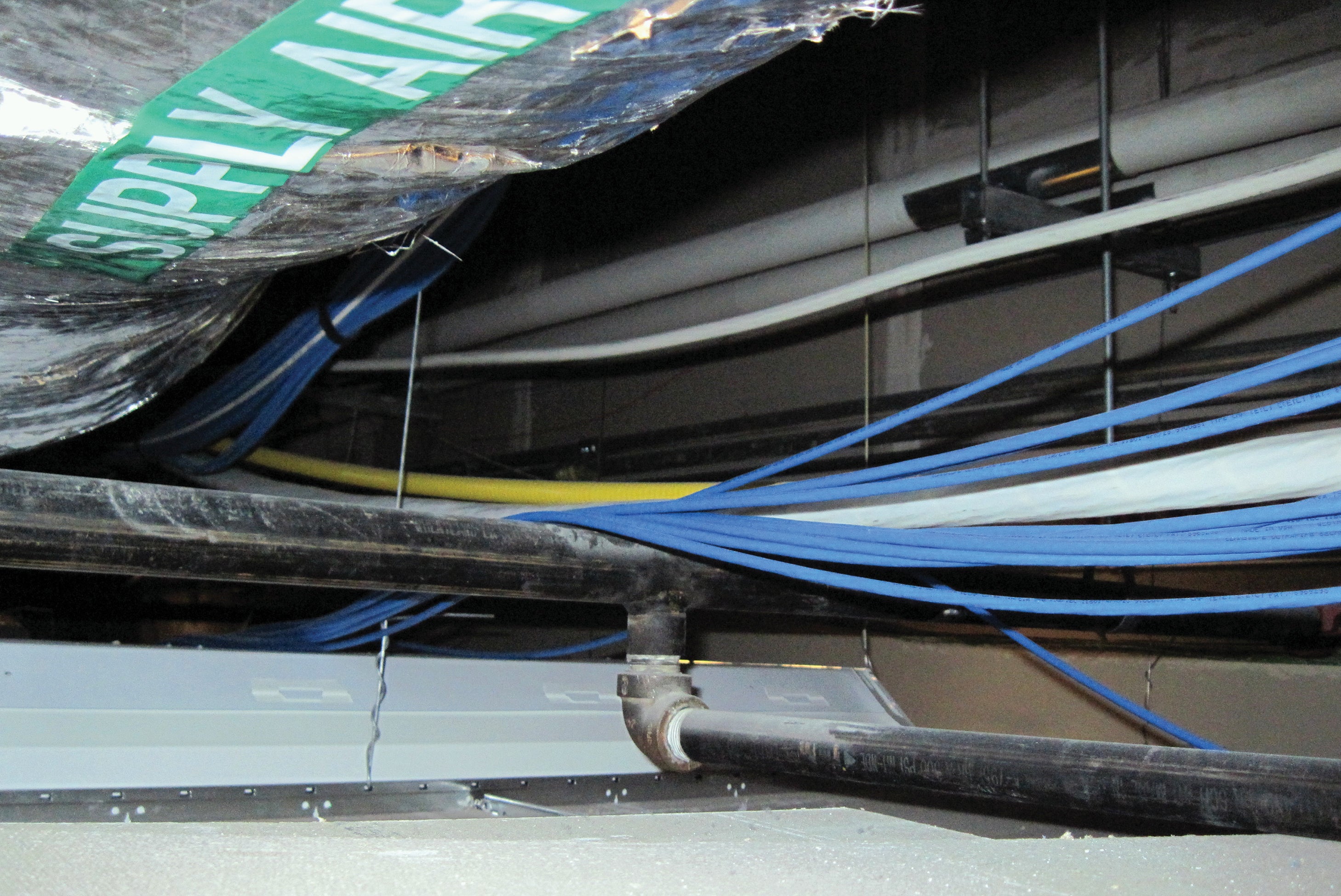
Network cables improperly resting on fire sprinkler piping.
Image courtesy of the author
Low-voltage cabling creates its own unique issue of being properly supported by either a cable tray or J hooks as opposed to being run across the ceiling, or not being supported at all. As technicians remove tiles to access systems above the ceiling, it is difficult to perform work in a maze of loose and disorganized cables. Low-voltage cabling can consist of network, nurse call, security, building automation, telemetry, infant abduction, fire alarm and even tube system communication cabling.
Developing a program
Regardless of a hospital’s particular situation, a robust training program for staff and contractors is imperative for maintaining the ceiling space within the built environment. Examining fire- and smoke-rated wall penetrations, smoke barrier compliance and items resting on or supported by fire sprinkler piping; installing systems to facilitate maintenance and operations; and properly following up documentation after any above-ceiling work are keys to a successful compliance program.
As health care facilities staff perform work above the ceiling, they should be trained to complete a 360-degree visual inspection of the space in which they are working. A simple checklist attached to a tool cart with the necessary repair components is a recommended practice for an efficient, organized above-ceiling program. A few items to furnish with every tool cart can include, but are not limited to, a ladder, flashlight, J box covers, knockout seals, firestopping material, J hooks, cable ties, trash bags, latex hand-protection gloves, a soft-bristle paintbrush to clean sprinkler heads and a battery-powered, HEPA-filtered vacuum.
The ceiling space in any building is typically filled with ductwork and piping so tight it may be difficult to even replace a ceiling tile. Compounding the tight space and creating further inaccessibility can be a leaking waste pipe fitting that is run on top of the ductwork. Special consideration must be given on how to access such leaks and repair them properly without endangering staff or vendors in the process.
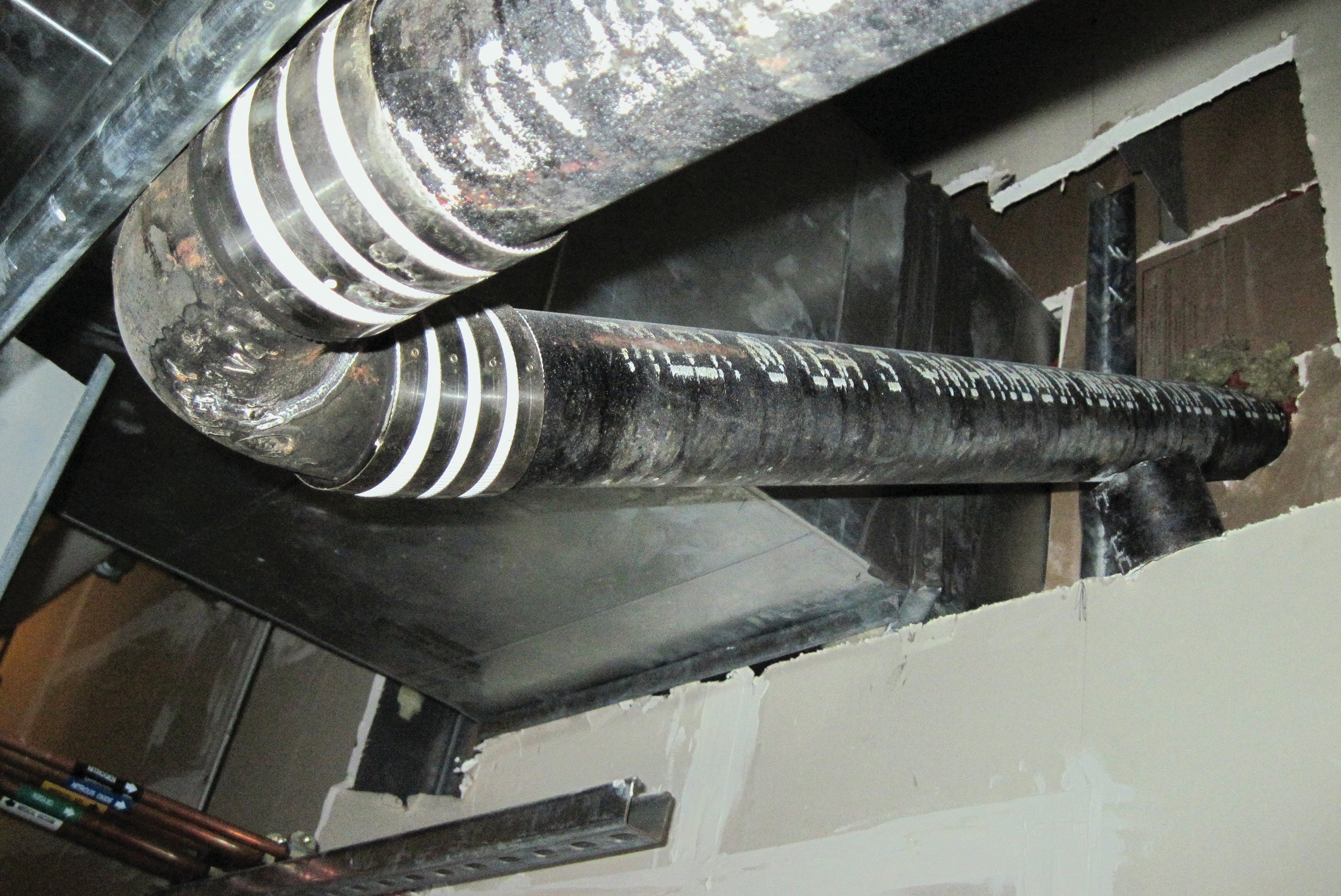
A 1-hour wall penetration and improperly supported drain-waste-vent piping.
Image courtesy of the author
A best practice for vendors and contractors may be to not only issue an above-ceiling permit, but also indicate on a set of drawings the proposed pathway, and any smoke or fire walls they will be penetrating during the pathway. These drawings can also include the products to be used for firestopping, pictures before and after the installation, IP requirements during the process, the times and dates of the process to reduce patient care exposure, and the primary point of contact for follow-up.
Questions that should be answered in an above-ceiling program include:
- Are ceiling tiles damaged or stained?
- Are there any holes or gaps in ceiling tiles, and are they smoke tight?
- Are fire- and smoke-rated walls missing proper identification above the ceiling by stenciling or other specific rating identifications?
- Is there any evidence of mixed fire- and smoke-stopping material?
- Are there any improper scab patches?
- Are all seams on drywall of rated walls sealed by either drywall finishing or proper material?
- Is there any fireproofing missing from structural components?
- Are there any items resting, attached to or supported by fire sprinkler piping and components?
- Are fire sprinkler heads dirty, corroded, painted or leaking?
- Are there any items running through fire and smoke dampers that might hinder their operation?
- Are access panels properly secured and sealed?
- Are there any electrical junction boxes missing covers or any open knockouts that need to be sealed by plugs?
- Are light fixtures properly secured and supported independently?
- Are there any low-voltage or network cables that need to be properly supported and secured?
- Is there any wiring above 50 volts that needs to be properly supported, and are there any open wiring connections?
- Is the medical gas piping properly identified and labeled every 20 feet?
- Are there any variable air volume box covers missing or improperly secured?
- Is there any mechanical-electrical-plumbing and steam piping insulation missing?
- Is there any evidence of water or other moisture from piping or ductwork?
- Is there trash or debris above the ceiling?
- Are there any wood or wood products above the ceiling?
- Are there any abandoned devices, cabling, ceiling tiles, temporary barricades, temporary lighting or any other items that do not belong above the ceiling?
- Can repairs be addressed now, or must a corrective work order be opened to facilitate the complete repair?
Under construction
Health care organizations often perform construction and renovation to accommodate changes or improve services. These changes may include adding, upgrading or altering the services required for a new piece of equipment, or a potential clinical service line.
Most construction and renovation activities occur near the clinical and operational health care environment. Construction and renovation activities release airborne contaminants and present an increased risk of tracking contaminants like dirt and dust into the area by workers, or as supplies, tools and materials are introduced from outdoors.
When working with new construction, facilities staff should partner with the planning, design and construction team and contractors to ensure items above the ceiling are easily accessible and subsystems are not obstructed by other means during the construction phase.
Coordination between tradespeople during the construction phase is imperative to achieve a solution above the ceiling that can be maintained throughout the lifespan of the building. Many times, the different tradespeople do not work together on projects due to scheduling and staffing assignments. Thus, many conflicts can occur over which tradespeople have priority of the pathway above the ceiling.
Such conflicts may be reduced via 3D building modeling and construction software to streamline field installation and reduce overall costs. It will also provide facilities staff with a better-defined overall situation of which systems are above the ceiling and where they are located.
Finally, the ASHE Certified Health Care Physical Environment Worker program is suggested training for anyone performing work in a health care setting. ASHE has also developed other tools to assist with comprehensive compliance from assessing risk to ICRA education.
A robust program
Many maintenance activities performed above finished ceilings can increase the risk to patients, staff and visitors. In fact, the above-ceiling environment is just as important, if not more important, to maintain than the space below the ceiling that everyone can observe.
Developing a robust above-ceiling access program or reviewing an existing program and performing periodic follow-up inspections to validate program success is imperative to maintaining the physical environment for patient care.
Accurate life safety plans are key to an above-ceiling permit program
A key attribute of a comprehensive above-ceiling permit program is accurate life safety plans (LSPs). Specific to above-ceiling management, LSPs should clearly define and delineate various barrier types and passive fire protection systems. (For more information on these requirements, see the article “Navigating IBC and NFPA differences” from the May 2022 issue.)
Facilities professionals should think of these barrier types and systems as if they were on a ship to provide water-tight integrity. The smallest penetration could sink the vessel or put the entire crew at risk. This is also true for health care facilities.
Protecting patients and staff is accomplished by a defend-in-place strategy to minimize fire and smoke migration. An effective barrier management and above-ceiling permit program is vital to maintaining barrier integrity. Barrier systems include walls, floors, ceilings and dampers. Each has a very specific process and remedy to maintain its designed integrity. (For more information on maintaining an LSP, see the article “Maintaining life safety drawings” in the June 2021 issue.)
The work on fire and smoke barriers in health care is disproportionately high due to having to defend in place. Facilities managers should know in advance where the penetrations in these barriers will be, how they will be made and what UL-listed systems will be utilized to bring the barrier back to its intended integrity.
A copy of the affected area of the LSPs should be attached to the above-ceiling permit. The drawing should display the affected area(s) and gain facilities management’s approval before any penetrations or modifications are made.
Once the work is complete, inspected and UL listings are verified, the LSP should be updated to reflect any changes. If there are no changes to the barrier, the marked-up drawings should be filed with the above-ceiling permit denoting the work that was performed, when, by whom, and who verified and approved the work should there be a question in the future.
About this article
This is one of a series of monthly articles submitted by members of the American Society for Health Care Engineering’s Member Tools Task Force.
Michael Huff, CHFM, CHC, CHCPE, CPMM, CRCST, CHL, is director of plant operations at Baylor Scott & White Health. He can be reached at autoclave1@hotmail.com.